The global demand for bottled water has surged over the past few decades, driven by increasing consumer preference for convenience, health awareness, and the scarcity of safe drinking water in some regions. This boom has led to the expansion of water bottle production across the globe, compelling manufacturers to seek ways to improve production efficiency. The role of technology in achieving this goal has been transformative, affecting every stage of the production process—from material sourcing and bottle design to manufacturing, quality control, and distribution.
In this article, we will explore the impact of various technological advancements on water bottle production efficiency, focusing on key areas such as automation, materials science, sustainability, and energy optimization.
- Automation in Water Bottle Manufacturing
Automation has been one of the most significant drivers of efficiency in the water bottle industry. The use of robotic systems, advanced conveyor belts, and automated assembly lines has significantly increased production speed while reducing the need for manual labor. This shift towards automated manufacturing has numerous benefits:
Increased Production Speed: Automated machines can produce bottles at a much faster rate compared to manual operations. Modern systems are capable of producing tens of thousands of bottles per hour, enabling companies to meet growing demand
more easily.
Consistency and Precision: Automated systems ensure a higher level of consistency in bottle shapes, sizes, and designs, minimizing the chances of defects and wastage. With precision engineering, the thickness of the bottles can be controlled to optimize material usage without compromising durability.
Reduced Labor Costs: The implementation of automated machinery reduces reliance on human workers for repetitive tasks, leading to a decrease in labor costs and fewer human errors. Employees can be redirected to more value-added tasks such as quality control and maintenance.
Real-Time Monitoring: Automation enables real-time monitoring of production lines, helping companies detect and address issues like equipment malfunctions or material shortages immediately, reducing downtime and further improving efficiency.
- Materials Science and Lightweighting
Advances in materials science have had a profound impact on the production of water bottles, especially in terms of reducing raw material usage and enhancing production sustainability. One such innovation is the development of lightweight plastic materials.
PET (Polyethylene Terephthalate): PET remains the most common material used for water bottles due to its lightweight, durable, and recyclable nature. Recent advancements in PET technology have allowed manufacturers to reduce the weight of bottles without sacrificing strength, a process known as “lightweighting.” By producing thinner bottles, companies can significantly lower their material costs and reduce their environmental footprint.
Alternative Materials: Innovations in biodegradable and plant-based plastics are also emerging, such as PLA (Polylactic Acid), which is made from renewable resources like corn starch. These eco-friendly materials are gaining popularity as companies strive to meet consumer demand for sustainable packaging.
Recycled Materials: The use of post-consumer recycled (PCR) plastic has become more common, allowing companies to reduce their reliance on virgin plastic materials. This not only cuts costs but also supports circular economy initiatives aimed at reducing plastic waste.
- Sustainable Practices and Energy Efficiency
Sustainability has become a central focus for water bottle manufacturers as concerns about environmental impact and resource depletion continue to grow. Technological innovations have played a crucial role in making water bottle production more eco-friendly and energy-efficient.
Energy-Efficient Equipment: Modern machinery is designed to be more energy-efficient, reducing power consumption during the production process. For instance, blow molding machines, which are used to shape the bottles, now come with advanced energy-saving features that allow them to operate at lower temperatures and use less electricity.
Water Conservation: The production of water bottles traditionally requires significant amounts of water, both for the creation of the bottles and for cooling during the manufacturing process. New technologies have been developed to recycle water used in the production process, drastically reducing water consumption and the environmental footprint of water bottle manufacturing.
Renewable Energy Integration: Some manufacturers have integrated renewable energy sources like solar or wind power into their production facilities. This not only reduces the dependency on non-renewable energy but also aligns with growing industry standards for sustainability.
- Digital Twins and Predictive Maintenance
The concept of digital twins—virtual models of physical production lines—has gained traction in water bottle manufacturing. By creating a digital replica of the production process, manufacturers can simulate different scenarios and optimize their operations before making real-world changes.
Predictive Maintenance: By using data collected from sensors installed in production machinery, companies can implement predictive maintenance strategies. These sensors monitor equipment health and predict potential failures before they occur, allowing manufacturers to carry out maintenance during planned downtimes rather than experiencing costly unexpected shutdowns. This maximizes equipment uptime and improves overall production efficiency.
Process Optimization: Digital twins allow manufacturers to analyze bottlenecks, test the impact of different materials or equipment settings, and make adjustments to enhance efficiency without interrupting the actual production line. This ability to experiment in a virtual environment reduces risk and accelerates the implementation of process improvements.
- 3D Printing and Prototyping
3D printing technology has revolutionized the prototyping process for water bottles. Instead of relying on traditional mold-making methods that are costly and time-consuming, manufacturers can now use 3D printers to rapidly create and test new bottle designs.
Rapid Prototyping: 3D printing enables companies to produce prototypes of new water bottle designs quickly and at a fraction of the cost of traditional methods. This accelerates the development of new products and reduces the time to market.
Customization and Innovation: 3D printing allows for greater design flexibility, enabling the creation of complex, lightweight, or ergonomically superior bottle designs. This not only enhances the consumer experience but also optimizes the use of raw materials, contributing to production efficiency.
- Quality Control and Smart Manufacturing
Advances in sensor technology, AI, and machine learning have significantly improved quality control in water bottle manufacturing. These technologies ensure that each bottle meets stringent quality standards while minimizing waste.
AI-Powered Inspection Systems: Smart cameras and AI-driven inspection systems are now capable of detecting even the smallest defects in bottles, such as cracks, improper sealing, or deformation. This allows for early detection and removal of defective products before they reach consumers, reducing the overall defect rate and material waste.
Data-Driven Decision Making: Machine learning algorithms analyze production data in real-time, providing actionable insights that help manufacturers optimize their operations. This can include recommendations on temperature settings, material mixing ratios, or even bottling speeds to ensure that production is both fast and efficient while maintaining high-quality standards.
Conclusion
Technology has fundamentally transformed the water bottle manufacturing industry by improving production efficiency, reducing costs, and driving sustainability. From automation and materials science to energy-efficient equipment and advanced quality control, these innovations have enabled water bottle manufacturing companies to meet growing consumer demand while minimizing their environmental footprint. As technology continues to advance, we can expect even greater improvements in efficiency, paving the way for more sustainable and cost-effective water bottle production in the future.
For manufacturers, staying ahead of technological advancements is key to maintaining competitiveness in an increasingly eco-conscious and cost-sensitive market.
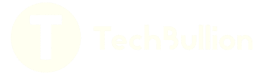