Non-Destructive Testing (NDT) is rapidly evolving, driven by technological advancements and the increasing need for efficiency, accuracy, and safety across various industries. As industries continue to adopt smarter and more automated processes, the future of NDT looks promising, with new trends and cutting-edge technologies shaping the way inspections are conducted. But what can we expect from the future of NDT, and how will emerging technologies redefine quality control?
Emerging Trends in NDT
- Automation and Robotics
The adoption of robotics and automation is transforming NDT processes, enabling faster, more reliable inspections with minimal human intervention. Automated systems equipped with advanced sensors and artificial intelligence (AI) can perform inspections in hazardous or hard-to-reach areas, reducing risk and enhancing efficiency.
Robotic systems are particularly useful in industries such as oil and gas, aerospace, and manufacturing, where they can inspect pipelines, aircraft structures, and production lines with greater precision and consistency.
- Artificial Intelligence and Machine Learning
AI and machine learning are revolutionizing NDT by improving data analysis, defect recognition, and predictive maintenance capabilities. These technologies can analyze vast amounts of inspection data, identify patterns, and provide actionable insights, helping businesses make informed decisions about equipment health and maintenance schedules.
Machine learning algorithms are being integrated into various NDT methods, including ultrasonic testing and NDT X-ray inspections, enhancing their ability to detect and classify defects with greater accuracy and efficiency.
- Digital Twins
The concept of digital twins—virtual replicas of physical assets—is becoming increasingly popular in NDT. These digital models allow for real-time monitoring and predictive maintenance, providing a comprehensive view of an asset’s condition over its lifecycle.
By combining real-time inspection data with historical performance data, digital twins enable engineers to identify potential issues before they become critical, improving operational efficiency and reducing downtime.
- Advanced Imaging Techniques
NDT X-ray and other advanced imaging methods, such as computed tomography (CT) and thermography, are becoming more sophisticated and widely used. These technologies provide highly detailed 3D images of internal structures, allowing for more accurate defect detection and analysis.
X-ray technology, in particular, is experiencing significant advancements, with portable and digital X-ray systems offering improved mobility and faster results, making them ideal for on-site inspections.
- Internet of Things (IoT) Integration
The integration of IoT in NDT is enhancing remote monitoring and data collection capabilities. Sensors embedded in industrial equipment can continuously monitor critical parameters and send real-time data to centralized systems for analysis.
IoT-enabled NDT systems can detect potential issues early, enabling proactive maintenance and reducing unexpected failures, ultimately saving costs and improving safety.
Technologies Shaping the Future of NDT
Several groundbreaking technologies are poised to redefine the NDT landscape in the coming years. Some of the most notable ones include:
- Phased Array Ultrasonic Testing (PAUT): This technology allows for highly detailed imaging and precise flaw detection by using multiple ultrasonic beams that can be steered and focused electronically.
- 3D Laser Scanning: Providing high-resolution scans of complex geometries, 3D laser scanning is revolutionizing inspections in construction, automotive, and aerospace industries.
- Portable Inspection Devices: Advances in portable NDT equipment are making it easier for inspectors to perform field inspections with greater accuracy and speed.
- Augmented Reality (AR) and Virtual Reality (VR): These technologies are being used for training purposes and real-time data visualization, enhancing the effectiveness of inspections and improving decision-making.
Challenges and Considerations
While the future of NDT is promising, it does come with challenges that industries must address to fully leverage new technologies. Some of these challenges include:
- Skill Gap: The increasing complexity of NDT technologies requires skilled personnel with expertise in AI, robotics, and data analysis.
- Data Security: With the rise of connected NDT systems, ensuring data security and privacy is becoming a critical concern.
- Cost of Implementation: Advanced NDT technologies often come with high initial costs, requiring businesses to evaluate long-term benefits and ROI.
Conclusion
The future of non-destructive testing is being shaped by automation, AI, advanced imaging, and digitalization. As industries embrace these innovations, NDT will continue to play a vital role in ensuring safety, quality, and efficiency across a wide range of applications.
With advancements in NDT X-ray technology, IoT integration, and predictive analytics, businesses can look forward to more reliable and cost-effective inspection solutions. As we move forward, the key to success will be adapting to these changes, investing in workforce training, and staying informed about the latest technological developments.
Are you ready to embrace the future of NDT and stay ahead in a rapidly evolving industry?
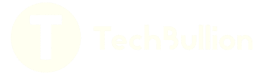