Introduction
Finite Element Analysis (FEA) has become an indispensable tool in mechanical engineering, enabling engineers to predict the behavior of structures and components under real-world conditions. By using numerical simulation, FEA helps optimize product designs, enhance safety, and reduce costs associated with physical testing. As technology evolves, FEA is becoming more powerful, integrating with artificial intelligence (AI), cloud computing, and computational fluid dynamics (CFD) to improve accuracy and accessibility.
This article explores the latest advancements in Finite Element Analysis services, how it is revolutionizing stress analysis, and its future in mechanical engineering.
What is Finite Element Analysis (FEA)?
Finite Element Analysis (FEA) is a numerical simulation technique used to predict the structural response of materials and components under various loading conditions. By breaking down a complex structure into smaller, finite elements, engineers can analyze factors such as stress analysis, fatigue, strain, vibration, heat transfer, and fluid interactions with high precision.
FEA is widely used across industries including aerospace, automotive, power generation, oil & gas, and heavy machinery to improve structural integrity assessment and meet safety compliance standards such as ASME, ISO, and API.
Key Advancements in FEA Technology
1️. Artificial Intelligence (AI) & Machine Learning in FEA
- AI-driven automation is transforming Finite Element Analysis services by automating meshing processes, optimizing computational efficiency, and detecting potential design flaws faster than traditional methods.
- AI-based predictive models analyse large datasets to suggest optimal material properties and structural modifications, reducing manual input.
- Example: Automotive companies are using AI-driven FEA stress analysis to enhance crash test simulations, improving both accuracy and speed.
2️. Cloud Computing for High-Performance Simulations
- Cloud-based FEA engineering services provide on-demand access to powerful computing resources, allowing engineers to run complex stress and fatigue analysis simulations without investing in expensive hardware.
- Collaboration is improved as multiple teams across different locations can access the same FEA models in real time.
- Example: Engineers in the oil & gas industry use cloud computing for FEA to analyse offshore pipeline integrity remotely.
3️. Integration of FEA with Computational Fluid Dynamics (CFD)
- Combining FEA stress analysis with CFD simulation enables engineers to simultaneously analyse mechanical stress and fluid interactions, leading to a comprehensive understanding of system performance.
- Example: In heat exchanger design, engineers use FEA for thermal stress analysis while CFD helps optimize fluid dynamics, ensuring efficiency and durability.
4️. Additive Manufacturing (3D Printing) & FEA
- FEA in 3D printing plays a key role by validating structural integrity before printing, ensuring that complex geometries meet strength and durability requirements.
- Example: Aerospace companies use Finite Element Analysis services to validate lightweight titanium components before 3D printing them for aircraft applications.
The Impact of FEA on Mechanical Engineering
- FEA stress analysis helps in design optimization, reducing material wastage by optimizing high-strength material design.
- Virtual Prototyping: Reduces the need for multiple physical prototypes, cutting costs and development time.
- Regulatory Compliance: Helps industries comply with ASME, API, ISO, and TEMA standards by validating pressure vessel optimization.
- Reliability & Safety: Identifies potential failures early, preventing catastrophic failures in piping systems, heat exchangers, and pressure vessels.
The Growing Role of FEA Services
Many companies now outsource FEA services instead of purchasing expensive software and training in-house teams. Engineering service providers like Ideametrics offer specialized simulations, including:
- Stress & Fatigue Analysis (predicting material failure over time)
- Crack Propagation Studies (analyzing fracture behavior)
- Fitness-for-Service (FFS) Assessments (ensuring continued safe operation)
- Thermal & Vibration Analysis (predicting heat distribution and dynamic response)
These services allow businesses to accelerate development cycles, reduce errors, and ensure compliance with international safety standards.
Conclusion
The future of FEA in mechanical engineering is exciting and transformative. As AI, cloud computing, and CFD integration continue to evolve, Finite Element Analysis services will become faster, more accurate, and widely accessible. Companies that leverage advanced FEA techniques will gain a competitive advantage by reducing costs, improving product performance, and ensuring regulatory compliance.
At Ideametrics, we specialize in cutting-edge FEA engineering services for industries ranging from oil & gas to aerospace and heavy machinery. Whether you need structural optimization, fatigue life prediction, or failure analysis, our expert team is ready to assist.
📌 Get in touch with us today to discuss your project and see how our expertise in FEA can help your business succeed!
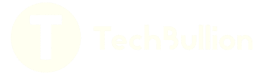