Investment casting is a widely used and revered method in the world of metal casting. Its precision and versatility have made it a go-to choice for many industries. However, like any manufacturing process, investment casting has its drawbacks that should be considered. In this article, we will explore the downsides of investment casting to provide you with a comprehensive understanding of its limitations.
1. Cost Considerations
Investment casting can be a costly process compared to other casting methods. The intricate nature of the wax patterns and the multiple steps involved in creating the ceramic shell contribute to higher production costs. The specialized equipment and skilled labor required for investment casting also add to the overall expenses. It’s important to carefully evaluate the cost-benefit ratio when considering investment casting for a particular project.
2. Production Time
Due to the complexity of investment casting, it often requires longer production lead times compared to other casting methods. The creation of wax patterns, the assembly of clusters, and the application of the ceramic shell all demand meticulous attention and time-consuming processes. If time is a critical factor for your project, alternative casting methods with quicker turnaround times may be more suitable.
3. Limitations in Part Size and Weight
Investment casting is better suited for producing small to medium-sized parts. The size and weight limitations of the ceramic shell and the handling capabilities during the casting process restrict the production of larger components. If your project requires casting larger parts, exploring other casting techniques such as sand casting or die casting might be necessary.
4. Material Restrictions
While investment casting offers a wide range of material options, including various metals and alloys, it does have some limitations. Certain materials with extremely high melting points or highly reactive properties may pose challenges during the casting process. It’s crucial to consult with experienced casting professionals to determine the feasibility of using specific materials in investment casting.
5. Surface Finish
Although investment casting typically provides excellent surface finish and dimensional accuracy, it may not be suitable for applications that require exceptionally smooth or polished surfaces. Some post-casting processes like grinding and polishing may be required to achieve the desired surface quality. Consider the surface finish requirements of your project when deciding on the casting method.
Conclusion
Understanding the cost considerations, production time, limitations in part size and weight, material restrictions, and surface finish challenges will allow you to make informed decisions when choosing the appropriate casting method for your specific needs.
Remember, investment casting remains a valuable and widely utilized process in many industries. By weighing the advantages and disadvantages, you can effectively leverage its strengths while mitigating potential drawbacks. Whether it’s creating intricate components for aerospace, medical devices, or automotive applications, investment casting continues to play a vital role in shaping the world of casting.
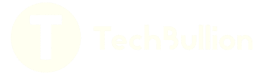