Conveyor rollers stand as the unsung heroes within the realms of logistics and production, playing a pivotal role in the smooth and efficient movement of goods across diverse industrial landscapes. At the heart of these systems lies the Conveyor Impact Roller, a critical component designed to absorb the shock and impact at loading zones, thereby safeguarding the conveyor belt against premature wear and damage. Working in unison, the Heavy Duty Roller Conveyor systems are engineered to withstand the rigors of heavy loads and high-speed operations, epitomizing strength and durability. Complementing these robust systems are the Nylon Conveyor Rollers, lauded for their lightweight design and minimal maintenance needs, offering seamless and noise-reduced operations ideal for a wide array of applications. Together, these sophisticated components form an integral framework, ensuring the continuous, safe, and effective transport of goods, hallmarking their indispensability in modern industry.
Maximizing Conveyor System Longevity
An integral component in the harmonious operation of Heavy Duty Roller Conveyor systems and Nylon Conveyor Rollers, the Conveyor Impact Roller functions as a protective shield for the conveyor system. It possesses the crucial task of absorbing the intense impact created during material handling, thereby preventing unwanted wear and tear on the conveyor belts.
Providing a more profound look into its functionality, the Conveyor Impact Roller performs five critical roles:
Shock Absorption: By leveraging its special design and material make-up, the impact roller efficiently absorbs kinetic energy, mitigating any possible damage to the belt due to heavy and abrasive goods.
Load Distribution: Impact rollers uniformly distribute the load across the conveyor belt, duly preventing stress concentration which can lead to unexpected ruptures or premature wear.
Vibration Reduction: The shock-absorbent properties of impact rollers have a secondary advantage in vibration reduction. Less vibration directly translates into reduced stress on other components, further extending the lifespan of parts of Heavy Duty Roller Conveyor systems and Nylon Conveyor Rollers.
Belt Tracking: Excessive vibration or impact can misalign the belt, impairing efficient functioning. Impact rollers help keep the belt on track, ensuring a smoother operation.
Spill Prevention: Impact rollers stabilize the load at the points of impact, thereby reducing material spillage that can cause additional wear on the conveyor system and require rigorous cleanup.
As the backbone of the transporting system, maintaining the conveyor belt’s health is of the utmost importance – it significantly affects the operating efficiency, safety, and upkeep costs. Keeping conveyor belt wear to a minimum with the help of a Conveyor Impact Roller preserves the lifespan of the entire system, including Heavy Duty Roller Conveyor and Nylon Conveyor Rollers, demonstrating the indispensable role these rollers play in any high-stakes industrial environment.
Building Resilience: Conveyor Systems for Heavy-Duty Industrial Applications
Characteristics Suitable for Intensive Industrial Use
Heavy-duty roller conveyors are engineered to withstand rigorous conditions, making them ideal for intensive industrial applications. The compatibility with Conveyor Impact Roller and Nylon Conveyor Rollers further elevates their status as the backbone of high-volume transport. Key characteristics include:
- Robust Construction: Built from high-grade materials, these conveyors are capable of carrying substantial loads, essential for industries where heavy materials are the norm.
- High-Efficiency Operation: Enhanced by Nylon Conveyor Rollers, these systems offer low resistance, ensuring smooth operations and minimal energy expenditures.
- Adaptability: Customizable to fit specific industrial needs, including size, shape, and roller type, providing flexibility across different applications.
- Versatility: The inclusion of Conveyor Impact Rollers allows these systems to handle a variety of materials, from heavy-duty equipment to delicate items, without compromising on speed or safety.
Importance of Specifications on Durability
The longevity and performance of heavy-duty roller conveyors are directly influenced by their specifications, namely the diameter, wall thickness, and frame design.
- Diameter of Rollers: Larger diameters typically bear heavier loads. In coordination with Conveyor Impact Rollers, a sizable diameter ensures that the conveyor can handle the initial impact of loading heavy materials, distributing the weight evenly across the system.
- Wall Thickness of Rollers: A thicker wall equates to a stronger roller. This is particularly crucial for Nylon Conveyor Rollers, as it determines their ability to withstand the weight and pressure of transported goods without warping or failing.
- Frame Design: The structural integrity of the conveyor system hinges on its frame design. A robust frame supports the rollers, maintains alignment, and absorbs operational stresses, ensuring the system can endure the demands of constant, high-volume usage.
This intricate integration of the Conveyor Impact Roller, Heavy Duty Roller Conveyor, and Nylon Conveyor Rollers epitomizes the pinnacle of conveyor technology tailored for high-volume industrial transport. Ensuring these conveyors are built and maintained with the right specifications in mind is paramount. It not only guarantees the system’s longevity but also safeguards the efficiency, reliability, and safety of the whole operation, making it a critical infrastructure in any high-performing industrial setting.
Revolutionizing Material Handling
In the industrial sector, where the smooth facilitation of materials and products defines the efficiency of operations. It not only enhances the performance of conveyor systems but also significantly trims down maintenance demands, marking a pivotal shift in how industries manage their conveyor operations.
Advantages of Nylon Conveyor Rollers in Various Industry Environments
Nylon Conveyor Rollers are celebrated for their lightweight nature, durability, and resistance to wear and tear, making them an ideal choice across a broad spectrum of industry environments. Their integration into systems alongside Conveyor Impact Rollers and within Heavy Duty Roller Conveyor setups presents multiple advantages:
- Corrosion Resistance: Nylon’s inherent resistance to chemicals and moisture negates the corrosion concerns that plague conventional metal rollers, making them suitable for harsh industrial environments.
- Noise Reduction: Nylon rollers operate considerably quieter than their metal counterparts, contributing to a more pleasant and compliant working environment.
- Decreased Wear on Equipment: The reduced friction between nylon rollers and conveyor belts extends the lifespan of the belts, highlighting the critical synergy between Nylon Conveyor Rollers and Conveyor Impact Rollers in preserving system integrity.
- Energy Efficiency: The lightweight nature of nylon reduces the load on the conveyor’s drive system, resulting in lower energy consumption.
Comparison to Other Materials
When juxtaposed with materials like steel or rubber, Nylon Conveyor Rollers offer a compelling case based on weight, noise, maintenance, and versatility of application:
- Weight: Nylon rollers are significantly lighter, reducing the overall load and strain on the conveyor system. This characteristic is particularly beneficial in Heavy Duty Roller Conveyor setups, where the efficiency and smooth operation of Conveyor Impact Rollers are paramount.
- Noise: Unlike metal rollers that can generate considerable noise, nylon offers a quieter operation, imperative in maintaining a conducive working environment.
- Maintenance: Nylon’s durability and resistance to many forms of degradation (including rust, chemical erosion, and wear) markedly lower the maintenance needs and associated costs.
- Application Versatility: The versatility of nylon to be engineered to suit specific industry requirements, such as varying levels of hardness and resilience, makes it an adaptable option across many sectors. This adaptability ensures that systems utilizing Nylon Conveyor Rollers can be tailored to meet the demands of Heavy Duty Roller Conveyor and Conveyor Impact Roller requirements effectively.
By integrating Conveyor Impact Roller, Heavy Duty Roller Conveyor, and Nylon Conveyor Rollers, industries can unlock a higher level of efficiency and operational smoothness. This synergy not only brings forth a reduction in maintenance requirements but also propels the utility and longevity of the conveyor systems to new heights, setting a benchmark in the material handling domain.
Achieving Optimal System Performance
In the dynamic environment of material handling and logistics, achieving an optimal balance in conveyor system performance involves a sophisticated integration of various components. Particularly, the collaboration of Conveyor Impact Roller, Heavy Duty Roller Conveyor, and Nylon Conveyor Rollers serves as a blueprint for designing a system that not only meets diverse operational demands but also enhances efficiency and sustainability.
Combining Conveyor Impact Rollers with Heavy-Duty Nylon Rollers
The integration process starts with a strategic placement of Conveyor Impact Rollers at points where the conveyor system encounters the greatest stresses, such as loading areas. These rollers are engineered to absorb the shock and distribute the load, thereby preventing damage to the conveyor belt and system overall.
Following the impact zones, incorporating Nylon Conveyor Rollers within the framework of a Heavy Duty Roller Conveyor system caters to several critical needs. Firstly, the nylon rollers, recognized for their durability and low friction, facilitate a smooth and efficient movement of goods. This is particularly beneficial in the middle segments of the conveyor, where maintaining momentum with minimal energy expenditure is crucial.
In heavy-duty applications, these nylon rollers offer the added advantage of reduced noise levels and resistance against corrosive substances, which can significantly prolong the lifespan of the system. This combination ensures that the system is not only robust, capable of handling high-volume and heavy loads, but also operates efficiently and quietly, contributing to a more productive working environment.
Selection of Rollers Based on Operational Needs and Cost-Effectiveness
The decision to integrate Conveyor Impact Rollers, Heavy Duty Roller Conveyors, and Nylon Conveyor Rollers should be guided by a thorough analysis of operational requirements and a clear understanding of long-term financial implications. Factors such as the nature of materials being transported, the environment of operation (such as exposure to chemicals or moisture), load capacity, and the expected frequency of use play a pivotal role in selecting the right components.
- Operational Needs: For systems that handle delicate or high-impact loads, Conveyor Impact Rollers are indispensable at the loading zones to mitigate damage. In contrast, for operations focusing on high-speed or long-distance transport, Nylon Conveyor Rollers offer an efficient solution by reducing friction and wear.
- Cost-Effectiveness: While the initial investment in specialized rollers such as impact-resistant or high-durability nylon might be higher, the return on investment materializes through reduced maintenance costs, lower downtime, and extended system longevity. Therefore, a careful cost-benefit analysis, keeping in mind both direct and indirect costs, should inform the selection process.
Integrating Conveyor Impact Rollers with Heavy Duty Roller Conveyor systems, complemented by Nylon Conveyor Rollers, requires a nuanced understanding of both the operational landscape and the unique benefits each component offers. This strategic approach not only optimizes system performance but also ensures a balance between operational efficiency and cost-effectiveness, paving the way for a future where adaptable, resilient, and efficient conveyor systems are the standard.
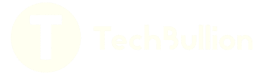