The steel industry has undergone numerous transformations over the centuries, but few innovations have had as profound an impact as the Bessemer Process. Developed in the mid-19th century, this revolutionary method made steel production faster, cheaper, and more efficient. Before its invention, steel was a luxury material, reserved for high-end tools and weapons. However, the Bessemer Process changed everything, paving the way for modern infrastructure, transportation, and industrialization.
The Origins of the Bessemer Process
Before the Bessemer Process, steel was produced through slow and labor-intensive methods. The most common technique, known as the crucible process, involved melting wrought iron with charcoal in small batches. While effective, this method was expensive and couldn’t meet the growing demand for steel during the Industrial Revolution.
Enter Sir Henry Bessemer, a British inventor who sought a more efficient way to produce steel. In 1856, he introduced his groundbreaking method at a meeting of the British Association for the Advancement of Science. His process involved blowing air through molten iron to remove impurities, drastically reducing production time and cost.
At first, Bessemer faced skepticism. Many manufacturers doubted his claims, but after refining his technique, the process quickly gained acceptance. By the 1860s, Bessemer converters were being used worldwide, revolutionizing the steel industry.
How the Bessemer Process Works
The Bessemer Process is a method of decarburizing molten iron to produce steel. Here’s a step-by-step breakdown of how it works:
- Melting the Iron – First, pig iron (a crude form of iron) is melted in a furnace at extremely high temperatures.
- Transfer to the Converter – The molten iron is then poured into a large, pear-shaped vessel called a Bessemer converter.
- Blowing Air Through the Molten Iron – A blast of air is forced through the bottom of the converter. The oxygen in the air reacts with impurities like carbon, silicon, and manganese, burning them off as gases or slag.
- Controlling the Carbon Content – Once most impurities are removed, the desired amount of carbon is added to achieve the right steel composition.
- Pouring the Steel – The purified steel is then poured into molds to cool and solidify.
This entire process took just 20 to 30 minutes, a dramatic improvement over older methods that required hours or even days.
Advantages of the Bessemer Process
The Bessemer Process brought several key benefits to steel production:
Faster Production
Unlike traditional methods, the Bessemer Process could convert iron into steel in under half an hour. This speed allowed factories to produce steel on an unprecedented scale.
Lower Costs
Since the process required less fuel and labor, steel became much more affordable. This cost reduction made steel accessible for railroads, bridges, and buildings.
High-Quality Steel
By removing impurities more efficiently, the Bessemer Process produced stronger and more durable steel. This improvement was crucial for heavy machinery and construction projects.
Mass Production Capabilities
The ability to produce large quantities of steel quickly supported the rapid industrialization of the 19th century. Factories, railroads, and ships all benefited from this innovation.
Limitations and Challenges
Despite its advantages, the Bessemer Process had some significant drawbacks:
Dependence on Low-Phosphorus Iron
The process struggled with iron ores containing high phosphorus levels, which made the steel brittle. This limitation forced manufacturers to source specific types of iron ore.
Inconsistent Quality
Since the process relied on manual control, the final steel quality sometimes varied. Without precise measurements, some batches were weaker than others.
Competition from Newer Methods
By the late 19th century, the open-hearth process began replacing the Bessemer method. Open-hearth furnaces could handle high-phosphorus ores and produced more consistent results.
The Legacy of the Bessemer Process
Although modern steel production has moved beyond the Bessemer Process, its impact remains undeniable. It laid the foundation for the mass production of steel, enabling advancements in construction, transportation, and manufacturing.
Railroads and Infrastructure
The expansion of railroads in the 19th century relied heavily on Bessemer steel. Strong, affordable steel tracks made long-distance travel and freight transport possible.
Skyscrapers and Bridges
The durability of Bessemer steel allowed engineers to design taller buildings and longer bridges. Structures like the Brooklyn Bridge utilized this innovation.
Industrial Growth
Steel became the backbone of industrialization, supporting factories, machines, and tools. Without the Bessemer Process, the Second Industrial Revolution might have progressed much slower.
Conclusion
The Bessemer Process was a game-changer for steel production, making it faster, cheaper, and more efficient. While newer technologies have since replaced it, its influence on modern industry cannot be overstated. From railroads to skyscrapers, the world we live in today was shaped by this revolutionary method.
Even though the Bessemer Process is no longer in widespread use, its legacy lives on. It proved that innovation could transform an entire industry, setting the stage for future advancements in metallurgy and manufacturing. Without it, the steel-driven progress of the 19th and 20th centuries might never have happened.
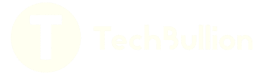