Plastic recycling has become a cornerstone of sustainable development, with equipment efficiency being a key factor in meeting the increasing demand for eco-friendly operations. Servo motors, known for their precision and energy efficiency, are transforming the landscape of plastic recycling equipment. This article explores how servo motors are applied in plastic recycling machine, highlighting their technical advantages, operational benefits, and real-world impact.
Technical Explanation: Servo Motors in Plastic RecyclingUnderstanding Servo Motors
Servo motors are advanced motors designed to deliver precision and efficiency through their feedback control systems. These motors are pivotal in applications where accuracy, responsiveness, and adaptability are required. They consist of three main components:
- Motor Unit: The primary device that generates motion. It converts electrical energy into mechanical energy to perform specific tasks.
- Controller: Acts as the “brain” of the motor. It monitors the desired operation and makes real-time adjustments through feedback loops to maintain precision.
- Encoder: A sensor that tracks the motor’s position, speed, and direction. It ensures that even the smallest deviations are corrected to achieve the intended movement.
Servo motors excel in tasks where high torque at low speeds or extremely precise movements are required, making them ideal for modern plastic recycling machinery.
Applications in Plastic Recycling EquipmentPlastic Extrusion Machines
In extrusion machines, raw plastic is melted and forced through a die to create shapes like pipes, films, or sheets. Here, servo motors are critical for:
- Precise Screw Control:
- The rotation and linear motion of the screw determine the pressure and flow of molten plastic.
- Servo motors adjust the screw speed and pressure dynamically, ensuring uniform melting and consistent extrusion quality.
- This reduces defects such as air bubbles or uneven wall thickness in the final product.
- Energy Optimization:
- By operating only at necessary speeds and loads, servo motors minimize energy wastage during extrusion.
Pelletizing Systems
Pelletizing involves cutting plastic strands into small pellets, which are the raw material for manufacturing. Servo motors play a vital role in:
- Blade Synchronization:
- The cutting blades must operate at precise speeds to cut evenly while avoiding damage to the material.
- Servo motors ensure the blades remain synchronized with the speed of the plastic strands, producing pellets of uniform size and shape.
- Load Management:
- The motor dynamically adjusts torque to handle varying strand thicknesses or material densities without halting the operation.
Conveyor Systems
In recycling plants, conveyors are used to transport materials between different processing stages. Servo motors improve these systems by:
- Accurate Speed Control:
- Servo motors ensure materials move at consistent speeds, preventing jams or overflow in downstream processes.
- Synchronization with Other Equipment:
- By coordinating with extrusion or crushing units, they ensure a seamless flow of materials, enhancing overall efficiency.
Compacting and Crushing Units
Recycling often begins with compacting or crushing waste plastic into manageable sizes. Servo motors enhance these processes by:
- Controlled Crushing:
- They apply just the right amount of force required to crush the material efficiently, avoiding overuse of energy or damage to the equipment.
- Energy Efficiency:
- Unlike traditional motors that operate continuously, servo motors adjust their energy consumption based on real-time load requirements.
Advantages: Servo Motors vs. Traditional Motors
Criteria
Servo Motors
Traditional Motors
Energy Efficiency
High, with adaptive power usage based on load
Lower, with constant energy consumption
Precision
Sub-millimeter level accuracy for complex tasks
Limited accuracy for variable operations
Speed Control
Instantaneous response to speed adjustments
Slower response times
Maintenance
Lower, with fewer mechanical parts
Higher, due to wear and tear
Durability in Load Variance
Consistently high performance in varying loads
Performance drops under inconsistent loads
Real-World ImpactCase Study: Energy Savings in Plastic Extrusion
- Setup: A plastic recycling company replaced traditional motors in its extrusion system with servo motors.
- Outcome:
- Energy Savings: Reduced power consumption by 30%.
- Production Efficiency: Achieved 15% faster processing speeds.
- Quality Improvement: Enhanced uniformity in extruded plastic products.
Market Adoption
- Servo motor adoption in plastic recycling is estimated to grow at a CAGR of 8% (2023-2030), driven by increasing demand for high-efficiency, low-maintenance solutions.
Conclusion
Servo motors are revolutionizing plastic recycling equipment with their precision, energy efficiency, and adaptability. By addressing the limitations of traditional motors, they not only optimize operational performance but also contribute to sustainability goals. As industries prioritize eco-friendly solutions, the role of servo motors in plastic recycling will continue to expand, driving both innovation and efficiency.
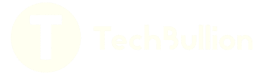