Medical equipment tends to be in a flux of development just as much as pharmaceuticals. However, unlike drugs, equipment tends to get less fanfare and glossy attention. In most cases, some of the biggest breakthroughs in medical equipment are never even seen, working consistently and reliably inside patients and only seeing the light of day again when surgically removed. Probably the only medical equipment most people are familiar with at first blush tends to be prosthetic devices, but even these are part of the technology development curve advancing today.
Testing Made Easier
Of course, like any product, prototyping matters greatly. It puts into real-time action designs and ideas about what equipment could look like and how it could work. This is made even more possible today with medical injection molding fabrication. Just like other plastics, injection molding processes are used to create devices, parts and components for medical equipment at single or mass production levels. The beauty of the process choices come in its low cost, easy adaption to new designs, and the ability to work with different levels of design thickness.
The Difference in Manufacturing Processes
With a standard injection molding company, the fabrication process is held to the specs provided by the client’s order. Spot inspection, samples or starting runs are produced and measured to confirm their accuracy in detail. The client and producer agree on a level of fault tolerance, and then the order is confirmed for the mass production.
With medical injection molding companies, a far greater amount of testing is involved. This is because of the pressure and expectation put on medical equipment to perform with a high level of reliability and consistency. After all, if medical equipment can fail, that can harm a patient it is used on, put in or relied on by the patient. So, no surprise, what is produced has to be manufactured at a high level of quality and must be audited and tested regularly as well and randomly to confirm constant performance in production levels. It’s an incredible difference from standard injection molding without such expectations.
Fabrication Processes are Under Scrutiny As Well
The quality expectations aren’t just on the end product. Injection mold fabricators also need to maintain a high quality level with the equipment they use as well. Contaminants have to be prevented at very high technical levels of non-tolerance, similar to the stringent standards required in probiotic tablet manufacturing. This ensures that the product created is as accurate as possible without other elements that can create a corruption in applied design. Why does this matter? When medical equipment has to work at a microscopic accuracy level, contaminants just as small can produce molding errors that could end up causing a serious injury or worse, especially if the equipment is applied internally within a patient.
Not Just Plastics Anymore
So, in the 1950s, plastics were joked about as the new industry that was going to change the world. As it turns out, injection molding for medical equipment may be going a lot further, especially in helping save lives and prolonging the same for other patients.
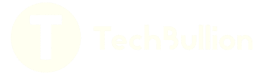