Teleoperated robots are transforming various industries by extending human capabilities into remote and hazardous environments. These advanced systems merge human intelligence with robotic precision, revolutionizing operations in sectors such as healthcare, space exploration, and disaster response. This comprehensive exploration, rooted in the work of Mahesh Jain, delves into the critical components of these robotic systems and the emerging technologies driving their evolution.
Building Blocks of Teleoperation
At the core of teleoperated robots lie several essential components. Robot Hardware consists of actuators, sensors, end-effectors, and onboard computers that execute commands. Sensors are the “eyes” and “ears” of these robots, providing awareness of their surroundings, while actuators are their “muscles,” driving precise movements. The hardware design varies significantly based on use, whether for bomb disposal or surgical precision.
The Control Station is where operators interact with robots. Equipped with input devices like joysticks or advanced haptic systems, and display tools such as VR headsets, it translates human instructions into robotic actions. Communication Links ensure a secure, fast connection between operators and machines, managing data transfers critical for real-time control. User Interfaces tie everything together, offering intuitive visual feeds, haptic feedback, and status updates, often using predictive technologies to offset delays.
Haptic Technology: Enhancing Tactile Precision
Haptic feedback is transforming teleoperation by allowing operators to feel remote sensations like pressure, texture, and weight. Using robotic sensors that detect environmental forces and relay these tactile sensations, operators gain a heightened level of control essential in fields such as medicine. In robotic-assisted surgery, for instance, haptic technology enhances precision, reduces errors, and improves patient outcomes. It is also invaluable in manufacturing and underwater operations, where nuanced object manipulation is required. By bridging the gap between physical and virtual experiences, haptic feedback enhances intuitive control, reduces fatigue, and boosts safety and effectiveness across various sectors.
Metaverse Integration: A New Dimension in Control
The integration of teleoperation with the metaverse is gaining momentum. Using virtual reality (VR) and augmented reality (AR) interfaces, operators can immerse themselves in a robot’s environment, enhancing spatial awareness and decision-making. Features like VR headsets and AR displays overlay crucial data onto real-world views, improving collaboration and training. Simulated environments allow operators to practice complex tasks safely and efficiently, while 3D data visualization boosts understanding and responsiveness. Though challenges like latency and hardware limitations persist, advancements in 5G and edge computing are making these integrations increasingly effective.
Diverse Applications Across Industries
Teleoperated robots are revolutionizing various critical fields through cutting-edge applications. In Military and Defense, they handle bomb disposal and reconnaissance, protecting personnel by inspecting explosive devices and collecting intelligence in dangerous areas with high-resolution cameras and manipulator arms. In Hazardous Environments, robots conduct essential tasks in nuclear facilities, such as inspections and decontamination, reducing human radiation exposure, while remotely operated vehicles (ROVs) manage offshore oil rig maintenance, replacing hazardous diving operations. The Healthcare sector benefits from telesurgery, where surgeons remotely perform precise operations using 3D visualization and tremor-filtration technology, and telepresence robots support remote consultations and monitoring. In Space Exploration, teleoperated robots facilitate extraterrestrial data collection and experimentation, and are being developed for satellite servicing and repair.
The Future of Work and Remote Operations
Teleoperated robots are transforming the workplace, enabling remote task execution and enhancing safety by minimizing human exposure to hazardous environments. They provide access to a global talent pool, allowing experts to contribute without relocating and promoting diversity. Teleoperation reduces travel, saving time and resources while supporting sustainability. Businesses can operate continuously by leveraging time zone differences for consistent productivity. However, challenges like establishing robust communication infrastructure and addressing security and regulatory concerns remain crucial to fully realizing their potential.
In conclusion, Mahesh Jain highlights that the future of teleoperated robotics holds immense promise, fueled by advancements in AI, mixed reality, and biointegrated control systems. These innovations will enhance the efficiency and intuitiveness of remote operations, bridging human expertise and robotic capabilities. As technology evolves, its applications will reshape industries and redefine human interaction. More than mere technological progress, these advancements signify a transformative shift in work, safety, and global collaboration, paving the way for a more connected and efficient future.
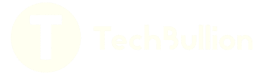