The automotive industry’s push for sustainability has made eco-friendly plastic welding a priority. Auto body plastic welding now focuses on reducing energy use, waste, and improving recycling to meet global environmental goals.
This article explores how advancements in welding technologies are transforming auto body welding practices, reducing their environmental footprint, and enhancing the recyclability of plastic welding car parts.
Energy Efficiency in Automotive Plastic Welding
Energy efficiency is a major consideration in automotive plastic welding. Welding methods such as hot plate welding and friction welding require precise heat and pressure, which can be energy intensive. Optimizing these processes is essential for achieving sustainable car plastic welding.
- Ultrasonic and Laser Welding: These methods have lower energy requirements compared to traditional techniques. Ultrasonic welding generates heat through high-frequency vibrations, while laser welding focuses energy precisely, making car plastic welding more efficient.
- Advanced Control Systems: The integration of IoT and programmable logic controllers (PLCs) in automotive body welding systems ensures real-time monitoring and energy optimization. This minimizes energy waste and enhances operational efficiency.
Adopting advanced technologies and optimizing existing methods can significantly reduce energy consumption in automotive plastic welding. For instance, integrating real-time monitoring systems ensures the precise application of heat and pressure, minimizing unnecessary energy use.
Reducing Waste in Automotive Plastic Welding
Waste management is another key aspect of sustainability in automotive plastic welding. Traditional welding methods can generate excess material and defective components, contributing to waste. Innovations in auto body welding are addressing this issue effectively.
- Precision Welding: Technologies like laser welding provide highly controlled welds, reducing material spillage and defects. This ensures that plastic welding car parts meet quality standards with minimal waste.
- Joint Design Optimization: Improved designs for welded joints reduce overlap and excess material, contributing to waste reduction in car plastic welding.
- Defect Recovery: In cases where welds are defective, processes such as ultrasonic re-welding enable repairs instead of scrapping the parts, reducing overall waste in auto body plastic welding.
These practices not only lower the environmental impact of auto body welding but also improve cost efficiency for manufacturers.
Recycling Potential of Welded Plastic Components
Recycling is a significant challenge in automotive plastic welding, as many components combine different plastic types, complicating the recycling process. However, recent advancements are improving the recyclability of plastic welding car parts.
- Material Selection: Using single-polymer systems or compatible plastic blends simplifies the recycling of welded components. This approach is increasingly being implemented in auto body plastic welding.
- Advanced Separation Technologies: Innovations such as density-based separation and chemical recycling make it possible to recover usable materials from complex car plastic welding assemblies.
- Closed-Loop Systems: Some manufacturers are adopting systems where scrap from automotive body welding is collected, reprocessed, and reused, creating a circular economy for plastic welding car parts.
For industries looking to adopt these sustainable practices, investing in the right plastic welding machine can make a significant difference by supporting both precision and eco-friendly operations.
Alternative Materials in Automotive Plastic Welding
The materials used in automotive plastic welding significantly impact sustainability. Bio-based plastics and recycled polymers are gaining traction as alternatives to conventional plastics in car plastic welding.
- Bio-Based Plastics: Made from renewable sources like sugarcane or corn starch, these materials offer a lower carbon footprint compared to petroleum-based plastics. They are increasingly being used in plastic welding car parts.
- Recycled Polymers: Integrating recycled materials into new components reduces the demand for virgin plastics. In auto body plastic welding, recycled polymers provide both structural integrity and environmental benefits.
These sustainable materials, combined with efficient auto body welding practices, contribute to a greener automotive industry.
Sustainability Metrics in Automotive Plastic Welding
To measure the environmental impact of automotive plastic welding, manufacturers often rely on key performance indicators (KPIs). These metrics help evaluate the efficiency and sustainability of auto body welding processes.
- Energy Intensity: Tracking energy use per weld highlights opportunities for optimization in car plastic welding systems. For instance, replacing traditional welding methods with energy-efficient technologies such as ultrasonic or laser welding can significantly reduce overall energy consumption, lowering both costs and carbon emissions
- Waste Generation: Monitoring scraps and defective components from auto body plastic welding provides insights into process inefficiencies. High waste levels indicate process inefficiencies, such as inaccurate heat application or poor material alignment.
- Recycling Rates: Measuring the proportion of recycled plastic welding car parts reflects the effectiveness of sustainability efforts. Manufacturers achieving this metric often focus on selecting compatible plastics and implementing closed-loop recycling programs to reduce dependence on virgin materials.
These metrics guide manufacturers in refining automotive body welding practices to ensure that sustainability becomes an integral part of their operations. This approach not only meets environmental goals but also boosts operational efficiency and brand reputation in an increasingly eco-conscious market.
Innovations Enhancing Sustainability in Automotive Plastic Welding
Advancements in technology are driving sustainability in automotive plastic welding. These innovations include:
- Smart Welding Systems: IoT-enabled systems optimize energy use and minimize waste during auto body plastic welding. These systems continuously monitor parameters such as heat, pressure, and timing to ensure precision. By reducing errors and defective welds, they not only conserve resources but also improve production efficiency.
- Renewable Energy Integration: Using solar or wind power to operate car plastic welding equipment reduces greenhouse gas emissions. This transition reduces dependency on fossil fuels, significantly lowering greenhouse gas emissions associated with auto body welding operations.
- AI and Machine Learning: AI-driven tools analyze data from auto body welding processes to improve efficiency and predict maintenance needs, further enhancing sustainability. This proactive approach extends the lifespan of machinery while reducing waste.
These innovations collectively enhance the sustainability of automotive plastic welding, aligning the industry with global efforts to decarbonize manufacturing and reduce its environmental impact. As these technologies continue to evolve, their role in creating a greener future for automotive production will only grow.
Challenges and Opportunities in Automotive Plastic Welding
Despite advancements in technology and materials, achieving sustainability in automotive plastic welding is not without its challenges. These hurdles are particularly significant as manufacturers seek to balance performance, cost, and environmental considerations.
The challenges include:
- Material Limitations: Not all bio-based or recycled plastics meet the performance standards required for car plastic welding. This can restrict their use in high-stress components like fuel tanks or structural assemblies, requiring further innovation in material science to bridge the performance gap.
- Cost Barriers: Advanced technologies and sustainable materials can be expensive, hindering widespread adoption in auto body welding. For example, integrating AI-driven systems or using renewable energy for auto body welding operations requires significant capital investment.
- Regulatory Complexities: Regulations around plastic use and recycling vary, complicating the implementation of sustainable practices in auto body plastic welding. Ensuring that auto body plastic welding processes meet these diverse requirements demands careful planning and adaptation.
However, these challenges also bring opportunities for innovation. Cross-industry collaboration can drive advancements in material engineering, process efficiency, and regulatory alignment.
By addressing these issues collectively, manufacturers can unlock new possibilities for enhancing the sustainability of plastic welding car parts, paving the way for a more eco-friendly automotive industry.
Conclusion
Sustainability in automotive plastic welding is essential as the automotive industry works to reduce its environmental impact. By focusing on energy efficiency, waste reduction, and the recyclability of plastic welding car parts, manufacturers can align with global sustainability goals.
Innovative technologies and alternative materials are making auto body plastic welding more eco-friendly. As these advancements continue, they will redefine automotive body welding, ensuring that the industry meets its environmental commitments without compromising quality or performance.
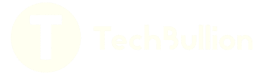