Warehouse docks are hubs of activity. Inbound trucks arrive with raw materials and inventory. Outbound trucks depart with finished products for customers. Efficient scheduling of arrivals and departures is critical.
Effective coordination optimizes dock operations. It reduces delays, prevents congestion and bottlenecks. Labor and resources are used effectively. Inbound loads are received and processed smoothly. Outbound orders ship on time. Supply chain efficiency improves. Customer service levels increase. Efficient dock scheduling brings tremendous benefits.
This blog post shares key strategies and best practices. These insights help streamline warehouse docks. They provide tips to coordinate inbound and outbound flows. Efficient docks are the key to supply chain success.
The Importance of Dock Scheduling
Dock scheduling involves coordinating and sequencing the arrivals and departures of trucks to maximize the usage of loading docks. Proper scheduling reduces wait times for trucks, avoids congestion, and enhances turnaround.
According to industry estimates, inefficient dock operations cost companies nearly $25,000 per dock door per year. Effective scheduling, supported by loading dock scheduling software, can help recoup these losses.
Dock scheduling provides the following key benefits:
- Optimized warehouse labor and resources:
Dock scheduling aligns staffing and capacity with expected truck volumes. This allows efficient handling of all scheduled inbound and outbound shipments.
- Enhanced truck turnaround:
With scheduled appointments, trucks spend less time waiting idly. This enables quicker turnarounds, improves driver experience, and provides cost savings.
- Reduced shipping delays:
Dock scheduling provides clarity regarding the timing of incoming and outgoing deliveries. Shipments arrive and depart as planned, minimizing delays.
- Improved supply chain visibility:
Real-time tracking of dock schedules and truck locations provides visibility across the supply chain for all partners.
- Higher inventory accuracy:
Inbound shipment arrival times are known in advance. This allows quick unloading, verification, and addition of incoming inventory into the system.
Strategies for Effective Dock Scheduling
Here are some key strategies to improve dock scheduling:
Implement Dock Scheduling Software
Manual scheduling through whiteboards or spreadsheets is inefficient. Dock scheduling software provides real-time visibility and coordination. Key features include:
- Appointment booking and management
- Dock door scheduling and optimization
- ERP and TMS integration
- Analytics and reporting
Scheduling software improves turn times by 20-50% and increases dock productivity by 15-25%.
Collaborate with Supply Chain Partners
Communicate dock schedules with suppliers, 3PLs, and other partners across the supply chain. Collaboration allows partners to align their operations.
- Share dock appointment slots:
Provide schedule visibility to partners so they can book dock times.
- Integrate shipping data:
Exchange shipping notices, ASNs, and tracking data to coordinate arrivals.
- Optimize delivery routes:
Suppliers can optimize routes and capacity based on dock schedules.
Segment Dock Activities
Dedicate certain dock doors for receiving, others for shipping, and some for oversized loads. This separates flows and reduces congestion. Separate schedules can be created for each activity zone.
Level Out Inbound Deliveries
Work with suppliers to spread out inbound deliveries across the week instead of having huge volumes on some days. Level loading minimizes congestion and allows smooth operations. Suppliers may offer pricing incentives in return for off-peak deliveries.
Prioritize Time-Sensitive Shipments
Expedite handling of priority outbound shipments by assigning them scheduled dock times for loading and departure. This ensures urgent deliveries depart on time.
Data Source: Acumatica
The Balance Between Inbound and Outbound Shipment Flows
In addition to coordinating overall dock activities, it is crucial to balance inbound and outbound volumes to avoid congestion.
Companies should analyze past shipment data to identify typical daily, weekly, and monthly traffic flows. This helps plan capacities and resources needed for both inbound and outbound activities.
Other tips include:
- Review inbound shipment schedules to determine outbound shipment cut-off times. Avoid scheduling large outbound volumes during peak inbound times.
- Similarly, cut-off times for inbound trucks should account for large outbound activities. Schedule inbound arrivals before major outbound processes start.
- Consider spreading inbound and outbound volumes throughout the day. For example, focus on inbound activities in the morning, then switch to outbound operations in the afternoon.
- Keep some dock doors free for ad hoc inbound and outbound volumes during the day. This provides a buffer capacity to handle uncertainties.
- Use historical shipment data to create templates for balanced daily, weekly, and monthly dock schedules. Update schedules based on actual volumes.
- Collaborate with partners to align inbound and outbound traffic. For example, have major suppliers avoid deliveries during outbound peak times.
Achieving the right equilibrium between inbound and outbound dock activities is key for smooth operations, optimal utilization, and supply chain coordination.
Best Practices for Dock Management
Follow these best practices to further optimize dock operations:
- Extend dock hours:
Add additional shifts or extend hours to align with truck arrivals/departures. This provides more flexibility to handle additional volumes.
- Implement dock reservations:
Require trucks to have reserved dock times for loading/unloading. This spaces out arrivals and prevents congestion.
- Automate gate processes:
Use automated systems for driver check-in, load/unload instructions, and paperwork. This speeds up gate movements so trucks can enter and exit smoothly.
- Improve dock design:
Have sufficient dock doors, proper spacing between bays, clear signage and directions, efficient layout to avoid jams. This facilitates easy movements.
- Train dock workers:
Ensure staff is proficient in loading/unloading, material handling equipment, and safety protocols. Well-trained staff work efficiently.
- Monitor performance:
Track metrics like truck turn times, dock utilization, and labor efficiency to identify bottlenecks. Address pain points to optimize operations.
- Enforce security:
Require driver IDs, vehicle inspections, and CCTV monitoring to prevent unauthorized access and theft. Security protects assets.
- Implement auto-dispatch:
Use algorithms to automatically dispatch trucks to open dock doors based on priorities and workloads. Removes manual effort.
- Leverage data analytics:
Gather and analyze data on dock activities to gain insights. Continuously fine-tune processes.
- Communicate with drivers:
Provide check-in instructions, directions, and loading guidelines proactively via app notifications or signs. Reduces delays.
Following industry best practices creates efficient, safe, and productive dock operations. Continual process reviews and improvements drive even higher performance over time.
Key Takeaways
- Effective dock scheduling is vital for coordinated inbound and outbound movements.
- Dock scheduling software provides real-time visibility and automation.
- Collaboration with partners, dock segmentation, and shipment prioritization are key strategies.
- Best practices like reservations, automation, and performance monitoring optimize operations.
- Effective dock scheduling leads to reduced delays, faster turnarounds, and lower supply chain costs.
With growing demands on warehouses, investing in dock scheduling improves efficiency, productivity, and customer service.
FAQs
What difficulties do companies face in dock scheduling?
Common issues are poor visibility into dock activities, congestion during busy times, inefficient processes, unused dock doors, and lack of data sharing between supply chain partners.
How can software assist with dock scheduling?
It enables real-time tracking of dock operations, automated scheduling based on priorities, alerts for late arrivals, yard management, and analytics for insights.
What are FIFO and LIFO dock scheduling methods?
FIFO (first-in-first-out) prioritizes the trucks that arrive at the dock earliest. LIFO (last-in-first-out) prioritizes the trucks that arrived most recently. The software can support both methods.
How can off-peak deliveries be encouraged?
Companies can offer discounts, preferential bookings, or financial incentives to suppliers willing to deliver during less busy off-peak times.
How do manufacturing and distribution dock schedules differ?
Manufacturing docks focus more heavily on inbound raw materials and outbound finished products. Distribution docks have more varied inbound and outbound flows. Scheduling priorities also differ between the two.
Conclusion
Effective dock scheduling is critical to streamline warehouse operations. Proper coordination of inbound and outbound shipments reduces delays and costs. Implementing dock scheduling software provides visibility, automation, and analytics.
Strategies like collaboration, segmentation, and shipment prioritization optimize flows. Best practices in dock management improve productivity. Balancing between inbound and outbound volumes minimizes congestion. Companies must focus on dock scheduling to maximize efficiency.
The result is a faster turnaround, lower expenses, and better customer service. Supply chain agility and responsiveness improve. In today’s dynamic environment, effective dock scheduling delivers significant benefits. It is an essential component of warehouse success.
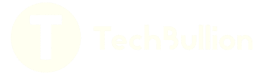