A stepper motor is a brushless, synchronous electric motor that takes digital pulses and turns them into mechanical rotation of the shaft. When it’s powered by a DC supply that’s switched on and off in sequence, the shaft moves in distinct angular steps that are pretty much the same size each time.
You can think of a stepper motor as a digital input-output device. It’s super handy for applications where the control signals come as digital pulses instead of smooth analog voltages. When you send one digital pulse to the motor’s drive or translator, it moves a specific angle. And as you keep sending those digital pulses faster, the motor starts to rotate continuously instead of just stepping.
You’ll find stepper motors being used in all sorts of industrial and scientific setups—like in robotics, machine tools, pick and place machines, automated wire cutting and bonding machines, and even in devices that control fluids with precision.
How does a stepper motor work?
A stepper motor divides each full revolution into a set number of steps—usually about 200. This means you need to send a separate pulse for each step. The motor can only move one step at a time, and each step is the same size.
Each pulse makes the motor turn a precise angle, typically 1.8°. Because of this, you can control the motor’s position without needing any feedback system. When you speed up the digital pulses, the motor shifts from stepping to continuous rotation, and the speed of that rotation directly matches the frequency of the pulses.
Stepper motors are really popular in both industrial and commercial settings. They’re low-cost, super reliable, provide high torque at low speeds, and are built tough enough to work in almost any environment.
A few key points about stepper motors:
The rotation angle of the motor directly corresponds to the input pulse.
The motor has full torque even when it’s standing still (as long as the windings are powered).
They offer precise positioning and repeatability. Good stepper motors have an accuracy of about 3 to 5% of a step, and this error doesn’t build up from step to step.
They respond really well to starting, stopping, and reversing.
They’re quite reliable since they don’t have any contact brushes. So, the lifespan of a stepper motor mainly depends on the bearings.
The way stepper motors respond to digital input pulses means you get open-loop control, making them easier and cheaper to manage.
You can achieve super slow synchronous rotation even with a load directly connected to the shaft.
Plus, a wide range of rotational speeds is possible since speed is proportional to the pulse frequency.
Choosing a Stepper Motor and the Controller
When picking a stepper motor, you need to think about the torque and speed needs of your application. Check out the motor’s torque-speed curve (you’ll find this in the specs for each drive) to find a motor that fits your requirements.
In the Omegamation line, every stepper motor controller shows the torque-speed curves for the recommended motors. If your torque and speed needs can be met by more than one motor, select a controller based on what your motion system requires—like step/direction, stand-alone programmable, analog inputs, or microstepping—then pick one of the recommended motors for that controller.
The recommended motor list comes from thorough testing by the manufacturer to make sure you get the best performance from the combination of the stepper motor and controller.
Choose the right stepper motor for your application
Step and Direction
These drives take in step pulses along with direction and enable signals from a stepper motor controller, like a PLC or PC. Each step pulse makes the motor rotate a specific angle, and the speed of rotation depends on the frequency of these pulses. The direction signal tells the motor which way to turn (clockwise or counterclockwise), and the enable signal is what turns the motor on or off.
Oscillator
Stepper motor drives that come with a built-in digital oscillator can accept an analog input or joystick for controlling speed. These are usually used in setups that need continuous motion instead of precise positioning, like in mixers, blenders, and dispensers.
Stand-Alone Programmable
All these stepper motor controllers can be set up for stand-alone use. You create the motion control program using an easy drag-and-drop software interface (which is included for free!), then you just download it and it runs when you power it up. Typically, the motion control program waits for something like a switch to close or a button to be pressed before it starts the programmed motion.
High Performance Stepper Motors
These digital stepper motor drives come with advanced features like self-test diagnostics, fault protection, auto-tuning, torque ripple smoothing, command signal smoothing, and anti-resonance algorithms. Some drives are programmable for stand-alone use, while others work with step/direction and analog inputs. If you want the best performance for your motion control system, go for the high-performance drives!
Related Articles
Pushbutton Switches:Description,Applications and Types
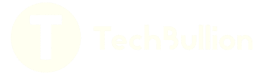