The CNC milling is a dynamic manufacturing approach, constantly evolving with technological advancements. As a pivotal component of modern manufacturing, CNC milling has transcended traditional boundaries, introducing new levels of precision and efficiency. The shift towards more advanced CNC milling techniques has been significant in recent years.
Understanding these changes is crucial for anyone involved in the manufacturing sector. Staying informed about the latest trends in CNC milling means staying ahead in a competitive market.
Let’s discuss the four-latest CNC Milling advancements that will keep you informed about the industry.
Integration of Artificial Intelligence in CNC Milling
As every industry integrates AI, manufacturing is no exception. It is ahead among all after Information Technology. The integration of AI) in CNC milling is transforming the manufacturing landscape. AI’s ability to analyze data and learn from processes has significantly changed machining efficiency and accuracy. This technology interprets complex data sets from CNC operations, optimizing machining parameters and tool paths. As a result, CNC milling becomes more smart, reducing errors and increasing output quality.
Next, AI’s role in predictive maintenance within CNC milling cannot be understated. It minimizes downtime and extends the lifespan of equipment by monitoring machine performance and predicting potential failures. AI integration for predictive analytics in CNC milling not only streamlines the manufacturing process but also elevates the overall efficiency of the production line. For example, research has shown that ” IIoT sensors and advanced edge computing enables maintenance teams to unlock machine performance and condition data to inform when maintenance activity should occur.” Source.
Moreover, AI’s contribution extends to quality control in CNC milling. With advanced algorithms, AI systems can detect even the slightest deviations or flaws in milled components, ensuring each part meets stringent quality standards. This level of precision is crucial in industries where accuracy is paramount, such as aerospace and medical device manufacturing.
Advancements in 5-Axis CNC Milling Machines
The evolution of 5-axis CNC milling machines has marked a significant milestone in the manufacturing industry. These machines offer unparalleled precision and efficiency, even for complex parts.
This advancement has increased capabilities and the automation and flexibility it brings to the production line. Manufacturers can now undertake complex tasks more efficiently and accurately, reducing the need for multiple setups and manual intervention.
Table: Advancements in CNC milling machine
Advancement | Description | Impact |
Enhanced Precision | The latest 5-axis CNC machines have improved accuracy due to advanced calibration and control mechanisms. | This produces highly accurate and intricate parts, minimizing errors and waste. |
Increased Speed | Modern 5-axis machines have faster processing capabilities and rapid tool change systems. | Quicker production times and higher throughput are achieved, enhancing overall productivity. |
Complex Geometries | These machines can produce parts with complex geometries that are challenging or impossible with traditional machining. | It expands the range of possible designs and applications in industries like aerospace and automotive. |
Improved Automation | Integration with advanced software allows for more automated and efficient machining processes. | Reduction in manual labor and human error, leading to consistent quality and lower production costs. |
Enhanced Flexibility | The ability to pivot and rotate on multiple axes provides unparalleled flexibility in machining. | This allows for single-setup machining of complex parts, reducing setup time and costs. |
Compact Design | Newer models are more compact and space-efficient without compromising on capability. | Smaller footprint machines are ideal for smaller workshops, expanding access to advanced machining. |
Energy Efficiency | Advances in technology have led to more energy-efficient designs. | This results in lower operational costs and a smaller environmental footprint. |
User-Friendly Interfaces | Modern 5-axis CNC machines feature more intuitive and user-friendly interfaces. | Easier operation and reduced training time for operators, enhancing workplace efficiency. |
Advanced Material Compatibility | Enhanced capability to work with diverse materials, including exotic and hard-to-machine alloys. | Broadens the scope of applications, catering to various industries with specific material requirements. |
Remote Monitoring and Control | Incorporation of IoT and remote monitoring capabilities. | Enables predictive maintenance and real-time monitoring, reducing downtime and enhancing productivity. |
Development in CNC Software and Simulation
Advancements in software and simulation technologies are dramatically reshaping the landscape of CNC manufacturing. These innovations enhance the efficiency and precision of CNC machines, changing how products are designed and manufactured.
Software developments in CNC have enabled more intuitive user interfaces, better integration with design software, and sophisticated simulation capabilities. These improvements are vital in reducing errors, optimizing production processes, and enabling more complex designs.
Critical developments in CNC software and simulation include:
- Intuitive User Interfaces: Modern CNC software features more user-friendly interfaces, making it easier for operators to navigate and execute tasks, reducing the learning curve, and enhancing efficiency.
- Advanced Simulation Tools: High-fidelity simulation tools allow for virtual testing of CNC processes, identifying potential errors and inefficiencies before actual production, saving time and resources.
- Integrated CAD/CAM Systems: Integrating CAD and CAM (Computer-Aided Manufacturing) systems streamline the transition from design to production, enhancing the overall workflow.
- Real-Time Data Analysis: Enhanced software now offers real-time data analysis and feedback, allowing for immediate adjustments and optimization of the machining process.
- AI and Machine Learning: Incorporation of AI and machine learning algorithms enables predictive maintenance, process optimization, and even adaptive machining strategies based on real-time data.
- Cloud-Based Solutions: Cloud technology facilitates remote access, collaboration, and data storage, making CNC programming and management more flexible and accessible.
Advancements in CNC Materials
CNC (Computer Numerical Control) technology has dramatically evolved, expanding its material repertoire beyond traditional metals. This diversification into composites and plastics has revolutionized manufacturing, offering enhanced properties and new possibilities in various industries, from aerospace to medical devices.
1. Metals
Innovations in metal treatments have improved performance, particularly in demanding sectors such as aerospace and automotive. Lightweight, strong alloys facilitate the creation of more efficient, durable components, maintaining metals’ relevance in advanced manufacturing.
2. Composites
Composites in CNC machining mark a significant advancement, offering high strength-to-weight ratios crucial in the aerospace and automotive industries. The machining of complex materials like carbon fiber reinforced polymers (CFRPs) and fiberglass has become more feasible with improved CNC technology. These materials pose unique challenges but promise lightweight and robust components, opening new avenues in design and functionality.
3. Plastics
Plastics have also seen significant use and advancements in CNC machining. Acrylics, polycarbonates, and polypropylene are commonly used, but one notable mention is PTFE (Polytetrafluoroethylene).
Renowned for its high melting point, chemical resistance, and non-stick properties, PTFE is challenging to machine due to its softness and tendency to deform. However, with the right tools and parameters, PTFE CNC Machining service can produce high-precision, chemically resistant parts ideal for various applications, such as chemical and food processing industries.
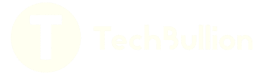