Oil and chemical spills have been the cause of more accidents and tragedies than we can count, but they still happen. Not all spillage issues make the news of course, but even seemingly minor spills can have dire consequences down the line.
Now, it’s an undeniable fact that preventive measures cannot always be 100% effective in averting unexpected circumstances and the ensuing accidents. Nevertheless, a well-planned and implemented spillage prevention and control plan can significantly lower the chances of such incidents. Even in bad situations, they often keep the spill from being much worse in terms of intensity.
Customization is Essential for Creating Reliable Spillage Prevention and Control Plans
There are numerous different fluid categories and industrial settings where a spill may lead to financial loss at the very least. Since a plan to prevent spillage at a construction site will not be of much use inside a chemical plant, prevention and control plans must be custom prepared to best fit the situation.
For example, the drip tray is a simple yet essential tool for mitigating both major and minor risks associated with chemical spills, oil spills, spills at construction and renovation sites, sewage spills, and more. In many cases, additional protective measures, such as oil stop valves, help prevent contaminants from spreading into drainage systems. However, there is a vast difference in design, construction, material choice, size, and other standard regulations that separate the various drip tray systems, based on their respective specialities.
Assessment is the Universal First Step
Assessment of the concerned location and the potential risk factors is an all-important, universal first step for mitigating spills. We now have access to a library of knowledge from past incidents and mistakes. We also have the technology to prevent, control and sometimes even predict future spills. All of which must be used in cohesion to constantly assess and mitigate spillage risks considerably.
Confinement Procedures and Plans Must be in Place
From drip trays and blotters to chemical absorbents, we do have access to a much wider range of tools nowadays to confine, if not prevent dangerous spills. The issue is often related to preparedness and reaction time. Thanks to all the advances made in spillage prevention, they do not occur anywhere near as frequently as before.
Unfortunately, that is also what will often lead to slow reaction times from the responsible party. When a spill does happen, the unexpected nature of the accident and a lack of properly trained personnel damages the efficacy of any confinement measures that are taken later. Whether it’s oil, chemical, or even sewage, trained professionals must be present to take all measures necessary to contain the spill and prevent it from spreading.
Budget can be a huge constraint for sure, especially for smaller businesses with limited resources. Nonetheless, that cannot be used as an excuse anymore when there are lives at stake. For example, smaller freight companies must be prevented from taking on more outsourced loads from large oil companies than they are prepared to handle safely. Making that mistake has been the primary cause behind some of the largest oil spills in recent history.
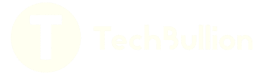