If you are an owner of an SME you’ll know the importance of a smooth-running procurement process all too well. One failure in the process can have a domino effect on the rest of the steps, bringing workflow to a halt, which is something that nobody wants or needs.
Let’s explore some simple ways to prevent poor procurement processes that could be a risk to your business – after all, prevention is better than cure.
Make sure you research suppliers properly
Quality materials can make or break your reputation, and in business, reputation is something that can make the difference between success and failure. This means you need to properly research and test out your suppliers to ensure you are getting the best product and service available. You need to be positive that what you are receiving is exactly what you require, as well as at the best value (for example, check out these semiconductors for electronics parts). In some cases, it could be an option to trial different suppliers before committing to them long-term, especially when it comes to regular bulk orders. It’s also a good idea to read reviews online from independent websites and get different quotes to see which is the most suitable option for your business.
Always double check
When it comes to ordering items, diligence is key. Accidentally ordering duplicate or excessive items that aren’t necessary can become stressful, costly mistakes. The same goes for not ordering an adequate amount of a particular part. Always make sure the figures are double-checked by more than one person, and that the delivery is arranged to come to the correct address at the right time. It sounds like common sense but when in a rush, these minor mistakes that can have catastrophic consequences can be made all too easily make.
Ensure you have set employee protocols in place
If your protocols are always updating and your team members haven’t been trained sufficiently to fully understand how they should be executing their tasks, then problems are likely to arise. You need to ensure that your workers are always in the loop, checking in with them regularly and providing training programs. Not only will this help you to organize your business, but it will also help your team to feel valued and informed. It should also improve efficiency throughout the system.
Make sure data is always updated correctly
Without the correct data in place when you’re dealing with procurement on a large scale, how do you know what you need more of and when? The short answer is, you don’t. This is why it is absolutely imperative that all the facts and figures are kept current, otherwise, errors will be much more likely. Your bill of materials always needs to be up to date in real-time, so that everybody that needs information from it has access to it. Without a modern digitized system, this can be more difficult to achieve. Communication is also key here – if anything changes or an issue is spotted, it needs to be brought to the attention of anyone else it may impact along the line.
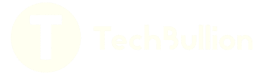