How Servo Motors Work
Servo motors have been around for ages and are used in all sorts of applications. They may be small, but they’re super powerful and really energy-efficient. If you’re into electronics and curious about what a servo motor is, it’s basically a specialized motor with a feedback system that lets you control things like position, speed, and acceleration with a lot of precision. You’ll find these motors in remote-controlled cars, robots, planes, and even in industrial setups, robotics, manufacturing lines, pharmaceuticals, and food services.
So, how does a servo motor actually work? Well, the magic happens in the motor unit, which has a positionable shaft, usually hooked up to a gear. The motor responds to an electric signal, which tells it how much to move the shaft.
Inside a Servo Motor
To really get what a servo motor does, you’ve got to take a peek inside. It’s actually pretty simple—a small DC motor, a potentiometer, and a control circuit. The motor is connected to a control wheel through some gears. As the motor turns, the resistance in the potentiometer changes, and the control circuit adjusts how much the motor moves and in which direction.
When the motor shaft reaches the position you want, the motor stops. If it’s not there yet, the motor keeps turning in the right direction. The motor’s speed depends on how close it is to the target position. If it’s almost there, it’ll slow down; if it’s far away, it’ll speed up. This is called proportional control, meaning the motor only works as hard as it needs to get the job done. Pretty neat, right? That’s basically how servo motors work and why they’re so efficient!
Servo Motor Control
Servos are controlled by sending electrical pulses of different widths through the control wire, which is called pulse width modulation (PWM). There’s a minimum pulse, a maximum pulse, and a steady repetition rate. Most servos can only turn 90° in each direction, giving a total of 180° movement. The motor’s neutral position is where it has the same amount of possible rotation both clockwise and counterclockwise.
To make it clearer, the PWM signal sent to the motor decides where the shaft will be positioned. Depending on how long the pulse is, the rotor will turn to the right spot. The servo motor expects a pulse every 20 milliseconds (ms), and how long that pulse lasts tells the motor how much to rotate. Still wondering how it works? Here’s an example: if the pulse is 1.5ms long, the motor will turn to the 90° position. If the pulse is shorter than 1.5ms, the motor will rotate counterclockwise toward 0°. If it’s longer than 1.5ms, the motor will turn clockwise toward 180°.
When you tell a servo to move, it’ll go to the position you’ve set and stay there. If something pushes against it while it’s holding that position, the servo will push back to resist moving out of place. The maximum force a servo can push with is called its torque rating. But keep in mind, servos don’t hold their position forever—they need a pulse sent repeatedly to keep holding that spot. Before picking the right servo for your project, it’s super important to understand how they work and the technical side of things.
Types of Servo Motors
Servo motors come in all sorts of types, shapes, and sizes. The term “servo” was first used by Joseph Farcot back in 1859 when he used steam to control a ship’s rudders. A servo has three parts: the motor, the feedback device, and control electronics. The motor is just one part of the whole system. For feedback, you can use things like a potentiometer, Hall-effect device, tachometer, resolver, encoder, or linear transducer—basically any sensor that fits your project. The control electronics compare the feedback and command signals to make sure the servo motor is working properly. This is the core idea of what a servo motor is all about.
Still wondering how a servo motor works? Well, there are two main types: AC and DC. AC servos can handle bigger power surges, which is why they’re usually used in industrial machines. DC servos, on the other hand, aren’t built for high-power surges and are better for smaller projects. DC servos are generally cheaper than AC ones. Some of them are designed for continuous rotation, making them great for getting robots moving. They even have two ball bearings on the output shaft to cut down on friction, making it easier to adjust the potentiometer that sets the rest point.
Servo Motor Applications
To really get what a servo motor is, you should also know where they’re used. In radio-controlled airplanes, servos position control surfaces like elevators and rudders. They’re also found in walking robots, robotic grippers, and more. These little motors are compact, have built-in control circuitry, and pack a punch for their size.
In food services and pharmaceuticals, servo motors are built tough to withstand harsh environments, like when equipment needs to be washed at high pressures and temperatures to meet hygiene standards. They’re also found in in-line manufacturing, where precision and repetition are key.
Now, you don’t need to know all the details of how a servo works to use one, but the more you understand, the more possibilities open up for your projects. Whether you’re a hobbyist building robots, an engineer working on industrial systems, or just someone who’s curious, servo motors can take your work to the next level. Want to dive deeper into electronics? Check out Jameco Electronics!
Related Articles
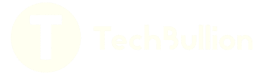