Roller bearings play a crucial role in various mechanical applications, providing support and reducing friction between moving parts. Whether you’re an engineer, a machinery enthusiast, or just curious about how things work, understanding roller bearings is essential. In this article, we will delve into the world of roller bearings, exploring their types, working principles, advantages, applications, maintenance, and more. So, let’s get started and know more about roller bearings.
Introduction
Roller bearings are mechanical components designed to enable rotational or linear movement while minimizing friction and supporting heavy loads. They consist of an inner and outer ring with a series of cylindrical, tapered, or spherical rollers placed between them. These rolling elements distribute the load evenly, allowing smooth and efficient movement.
What Are Roller Bearings?
Roller bearings are a type of anti-friction bearing widely used in various industries, including automotive, aerospace, industrial machinery, and more. They offer superior load-carrying capacity compared to other bearing types, making them suitable for applications with heavy radial or thrust loads.
Types of Roller Bearings
There are several types of roller bearings, each with its unique design and characteristics. The most common types include:
- Cylindrical Roller Bearings: These bearings have cylindrical rollers and provide high radial load capacity.
- Tapered Roller Bearings: With tapered rollers, these bearings can handle both radial and axial loads, often used in automotive applications.
- Spherical Roller Bearings: These bearings can accommodate misalignment and heavy loads due to their spherical outer ring.
- Needle Roller Bearings: Needle roller bearings have long, thin rollers and are suitable for applications with limited space and high radial loads.
How Do Roller Bearings Work?
Roller bearings work based on the principle of rolling motion. When a load is applied, the rolling elements distribute the force evenly, reducing friction between the inner and outer rings. This enables smooth rotation or linear movement, allowing machines to operate efficiently.
Advantages of Roller Bearings
Roller bearings offer several advantages, making them a preferred choice in many applications:
- High Load-Carrying Capacity: Roller bearings can handle heavy loads due to their design and distribution of rolling elements.
- Reduced Friction: By minimizing contact between the rolling elements and the rings, roller bearings significantly reduce friction, enhancing efficiency.
- Radial and Axial Load Support: Different types of roller bearings can support both radial and axial loads, offering versatility.
- Durability: Roller bearings are known for their durability, withstanding harsh operating conditions and providing long service life.
Common Applications of Roller Bearings
Roller bearings find extensive use in various industries and applications, including:
- Automotive: Roller bearings are widely used in wheel hubs, transmissions, engines, and other automotive components.
- Industrial Machinery: They are crucial in machinery such as conveyors, pumps, compressors, and gearboxes.
- Aerospace: Roller bearings are utilized in aircraft engines, landing gear systems, and flight control mechanisms.
- Construction and Mining: Heavy-duty equipment, such as excavators and bulldozers, rely on roller bearings for reliable performance.
Factors to Consider When Choosing Roller Bearings
Selecting the right roller bearings for a specific application requires considering several factors:
- Load Requirements: Determine the magnitude and type of load the bearing needs to support, whether radial, axial, or combined.
- Speed: Consider the rotational or linear speed at which the bearing will operate to ensure it can handle the required RPM.
- Operating Conditions: Evaluate environmental factors such as temperature, humidity, and exposure to dust or chemicals that may affect the bearing’s performance.
- Space and Design Constraints: Consider the available space and the bearing’s size, design, and mounting requirements.
Maintenance and Lubrication of Roller Bearings
Proper maintenance and lubrication are vital for ensuring the longevity and optimal performance of roller bearings. Here are some key maintenance practices:
- Regular Inspections: Periodically inspect the bearings for signs of wear, damage, or contamination.
- Lubrication: Apply the appropriate lubricant according to the manufacturer’s recommendations to minimize friction and prevent premature failure.
- Environmental Protection: Shield the bearings from dust, moisture, and other contaminants that can compromise their performance.
Signs of Roller Bearing Failure
It’s essential to be aware of the signs indicating roller bearing failure, such as:
- Unusual Noise: Grinding, rattling, or squeaking sounds may suggest bearing damage or wear.
- Increased Friction: If a machine becomes harder to operate or experiences decreased efficiency, it could be due to bearing issues.
- Excessive Heat: Overheating may indicate insufficient lubrication or bearing damage.
- Vibration: Excessive vibration can be a sign of misalignment or bearing wear.
Troubleshooting Roller Bearing Issues
When encountering roller bearing problems, some troubleshooting steps can help identify and resolve the issues:
- Inspection: Thoroughly examine the bearing and surrounding components for damage or misalignment.
- Lubrication: Ensure proper lubrication by following the manufacturer’s guidelines and using the recommended lubricant.
- Replacement: If severe damage or wear is detected, replacing the bearing may be necessary.
- Professional Assistance: In complex situations or if you lack experience, consult a qualified professional for guidance.
Conclusion
Roller bearings are essential components that enable smooth and efficient movement in various mechanical applications. With their ability to handle heavy loads and minimize friction, roller bearings have become indispensable in industries worldwide. By understanding the types, working principles, advantages, applications, and maintenance considerations of roller bearings, you can make informed decisions when selecting and maintaining them for your specific needs.
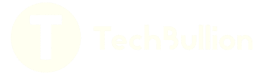