A robot may not injure a human being or, through inaction, allow a human being to come to harm.
A robot must obey the orders given it by human beings except where such orders would conflict with the First Law.
A robot must protect its own existence if such protection does not conflict with the First or Second Law.
Isaac Asimov, a science fiction author and professor at Boston University postulated the “Three Laws of Robotics” in his 1942 popular short story “Run-around”. Though these laws appeared fictional at the time of writing, the advent of technology has made humans and Robots work together and these laws, form the crux of the operation in such workplaces. While countries like Germany, Italy, Sweden, France, S. Korea, China, Spain, the US, UK have taken to the use of Robots in a big way subsequently driving up productivity and scale, India has somewhat lagged in the adoption of Robots on the shop floor. As the Government pushes on the idea of “Make in India”, it becomes imperative for Indian manufacturers to adopt Robots at the workplace.
With increased adoption globally, standard robot models are now mass-produced, and this presents a perfect opportunity for small and medium-sized companies to deploy Robotic Automation in their manufacturing and drive the next wave of value unlocking. A holistic view of the costs involved shall allow them to make the decision to adopt Robotic Automation.
At Addverb, we recommend the “FOLDUP” approach to customers to calculate the ROI for
Robotic Automation:
Flexibility: Robotic Automation is future-ready automation, by just reprogramming the robot and changing the end tools, the entire production process can be tweaked. This is in stark contrast with the special purpose machines which generally have hard tools that cannot be tweaked. In the case of a manual process, the human workforce clubbed with archaic labor laws makes the production process very inflexible.
Overheads: Once the upfront investment has been made in Robotic Automation, the cost of running the entire system is very low as compared to a manual system. Robotic Automation ensures low or no maintenance and administrative costs, which are quite high while managing a manual workforce. These costs are often not included in the ROI calculation, also the administrative costs (Overheads) generally tend to increase as the number of years of operation increases. Taking this into account results in a very low cost of total ownership for Robotic Automation.
Labor: At present, the majority of the jobs that absorb most of the labor are repetitive in nature, these kinds of jobs do not add any skill to the people who are employed. This, in turn, results in stagnation of labor which creates a hostile industrial relations scenario. With Robotic Automation, the labor that is required to maintain the robots is highly skilled and as such this provides better employment opportunity, resulting in harmonious industrial relations. Quite a few jobs in manufacturing take place in an environment that is hostile to the human body, using robots for such processes is a great investment that also ensures harmonious Industrial Relations.
Dependability: The manual process often results in variability and quality defects. Robotic Automation is highly dependable, and robots often prove to be superior to humans in terms of quality of the work for most of the production processes. Robotic Automation can drastically reduce the number of defects and improve the quality of the inspection. As Robotic Automation displays zero deviation from the production process, the resulting quality of the finished products is quite good. This cost often gets overlooked as a manual process usually results in high-quality defects, affecting the overall brand of the company as well.
Usage: This is the most important criterion that must be factored in while implementing Robotic Automation. Robots allow three-shift operations, 7 days a week and 365 days a year without any interruption and stoppage. While comparing with a manual process, this must be compared to an equivalent workforce that shall be required to manage such operations at this scale. It ensures continuous production without any stoppages due to administrative issues.
Productivity: Apart from non-stop usage, one of the most neglected aspects of Robotic Automation is the increase in Productivity. Having a Robot is like having a highly skilled resource available, round the clock. Unlike Robots, the human body is susceptible to short-term fatigue, injury and disability. Many jobs in manufacturing typically either because of the hostile environment or being repetitive in nature result in low productivity after some time. This is not the case with Robotic Automation, which ensures constant productivity throughout.
Even with all this, the most important factor that determines the success of Robotic Automation in a factory is an “Integrator”- a company which completely understands the nuances of Robotic Automation and can design complete solution that will maximize the output by selecting the right robot, designing the layout, integrating the vision system, etc.
Robotic Automation offers a very reliable and efficient production process, robots typically can be refurbished and used again after a period of 10-12 years with ease. All these factors make the ROI on Robotic Automation attractive; a good rule of thumb is to target a minimum of three years for calculating the ROI. After these three years, typically Robotic Automation results in positive cash flow for the company with minimum variability and high efficiency. That’s the stage when actual value unlocking happens for the organization. It becomes imperative for small and medium enterprises, who aim to grow, to look beyond the near future to truly ascertain the gains obtained from Robotic Automation.
About Addverb:
Addverb provides smart end-to-end warehouse and industrial automation and intralogistics solutions. Addverb’s fleet of automated robots, material handling technologies, and software solutions comprising an extensive portfolio of fixed and flexible automation solutions help improve the performance and accuracy of warehouse and factory operations. Addverb’s mission is to discover a customer’s warehousing problem, design an appropriate customized automation solution to the identified problem, deliver the solution, and provide dedicated after-sales support. Addverb’s headquarters, manufacturing, and R&D facilities are in India, with global offices in Australia, Singapore, the Netherlands, the USA, Germany, and the UAE. Addverb’s current 100+ customers include Coca Cola, PepsiCo, DHL, Amazon, Colgate Palmolive, Reliance, Unilever, Flipkart, Johnson & Johnson, and PAR Pharmaceutical. For more information visit https://addverb.com/
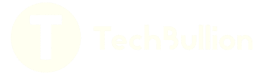