Historically, ergonomic risk assessments have been conducted by ergonomists or safety professionals who visit a workplace to observe employees performing tasks. They manually note posture, movements and environmental factors and use standardized checklists and tools to measure risk factors that may contribute to musculoskeletal disorders.
Some common evaluation methods include RULA, REBA and The Revised NIOSH (National Institute for Occupational Safety and Health) Lifting Equation. RULA (Rapid Upper Limb Assessment) is a survey method for evaluating the exposure of the upper limbs to ergonomic risks and focuses on posture, force and repetition. REBA (Rapid Entire Body Assessment) assesses whole-body postural risks associated with job tasks, accounting for static, dynamic and rapidly changing postures. Finally, the Revised NIOSH Lifting Equation is used to assess lifting task safety and, in an effort to reduce the risk of injury, identify the recommended weight limit.
Drawbacks of manual ergonomics assessments
While these manual methods may traditionally have had merit at one time, they also have significant drawbacks. First, they’re labor-intensive and time-consuming, making it difficult to efficiently assess multiple workstations or tasks. Further, scaling manual assessments across multiple sites or large organizations can be challenging.
Traditional assessments are informed by individual assessors’ expertise and judgment, potentially resulting in inconsistencies and subjectivity in evaluations. Additionally, because results and recommendations take time to compile, implementing important corrective actions may be delayed. Finally, relying on manual measurements and observations increases the likelihood of errors, particularly in complex settings such as the confined spaces airline ground crews operate in or the fast-paced, high-demand environments of electronics assembly lines.
How ergonomic risk assessments have improved with technology
By integrating computer vision and AI into ergonomics assessments, worker movements and postures can be automatically analyzed in real time to identify risky behaviors, eliminating the need for manual intervention. Large volumes of data can then be used to identify trends, and predictive analytics help organizations proactively address ergonomic risks before they result in injury.
Detailed risk assessments and recommendations generated automatically significantly reduce the time and effort needed for documentation. Finally, because assessment data can be stored, processed and analyzed in the cloud, it’s easily accessible and can be used collaboratively across multiple locations.
Benefits of utilizing technology for ergonomics assessments
Computer vision and AI reign supreme when it comes to preventing musculoskeletal injuries in the workplace: automation streamlines workflows, and AI-driven analysis yields more precise, reliable assessments.
Technology solutions also fast-track assessments, enabling safety professionals to focus on implementing solutions rather than spending time gathering data.
Further, because AI and computer vision are scalable, assessments across multiple sites and larger workforces become seamless without the need to increase resources.
Additional benefits include:
- Real-time feedback enables timely intervention and reduces the likelihood of injuries.
- Data-driven decisions can be made through the collection and analysis of large amounts of data and supports decisions based on predictive analytics and trends.
- Cost savings over time via injury prevention and efficiency enhancements.
- Enhanced employee wellness via proactive identification and mitigation of ergonomic risks boosts employee morale and reduces absenteeism.
What to look for
It’s important to note that all solutions are not created equally. The following criteria are paramount when choosing an AI-powered ergonomics assessment platform:
- Accuracy and reliability. Accurate ergonomic risk data, provided on a consistent basis, helps to minimize the chance of false positives or negatives.
- Ease of use. A friendly user interface enables experts and non-experts alike to operate the system.
- Real-time monitoring. Solutions should offer real-time data and alerts that allow for immediate corrective actions.
- Comprehensive reporting. Customized reports with crucial detail should be easy to understand and simple to act on.
- Data security. As with any sensitive workplace data, a system must offer security against data breaches and unauthorized access.
The bottom line
Technology has enabled advancements in countless industries; ergonomics is just one of them. The days of laborious manual assessments are growing fewer; today, ergonomics professionals rely on a mix of technology tools that have changed and improved the way they do their job.
These tools increase worker productivity and improve morale, save costs, and prevent worker injuries before they happen.
Zach Noland is co-founder of TuMeke, an AI-powered ergonomic assessment platform that streamlines how organizations identify and mitigate workplace injury risks.
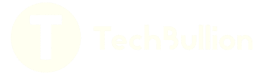