Intro to Quality Control
Quality control has long been at the core of manufacturing. It ensures products meet specific standards and meet customer expectations; but as industries advance so have their methods for maintaining quality. With advances such as automatic checking fixtures transforming modern production methods.
These innovative tools are revolutionizing how we view quality assurance. By streamlining processes, reducing human error and increasing efficiency to achieve product excellence in an increasingly precise world. Automatic checking fixtures represent a revolutionary leap forward that’s sure to reap great dividends for product excellence in years to come.
Manufacturing landscape is rapidly shifting in response to technological innovations and rising quality demands, necessitating companies to adopt automation to remain competitive without compromising standards of excellence. Let’s examine this fascinating development further and discover how automatic checking fixtures are revolutionizing quality control procedures.
The Evolution of Automatic Checking Fixtures in Manufacturing
As a professional manufacturer, Favamill dare say that automatic checking fixtures have come a long way since their debut. At first, these tools were simply mechanical devices used to verify parts met basic specifications; manual adjustments frequently led to inconsistent measurements.
As technology advanced, so did the design of these fixtures. Computer-aided design (CAD) allowed for more intricate measurements; manufacturers began including sensors and software into their systems for increased efficiency.
Today’s automatic checking fixtures come equipped with sophisticated automation technologies like robotics and artificial intelligence that enable real-time inspections at high speeds with significantly less human error.
With every advancement comes greater adaptability and flexibility in production lines. Modern solutions not only enhance accuracy but also contribute to faster turnaround times across diverse industries.
Benefits of Using Automatic Checking Fixtures
Automatic checking fixtures offer many benefits in manufacturing environments. They help ensure parts meet exact specifications every time and reduce human error – which could otherwise prove costly.
Speed is another crucial advantage offered by these fixtures; their efficient inspection process enables faster production cycles without sacrificing quality, so manufacturers can boost output while increasing reliability.
Consistency also plays a vital role. Automatic systems generate consistent outcomes regardless of who operates them, leading to more predictable results and making training for new staff simpler.
Reduce waste through early identification of defects in production lines. Addressing issues swiftly prevents defective goods from reaching consumers and saves both resources and reputation.
Integrating these fixtures can result in lower operational costs over time as your investment pays off through improved efficiency and reduced rework rates.
Case Studies:
Many companies have successfully integrated automatic checking fixtures into their production lines.
It was reported that BYD found dramatic enhancements in quality control by adopting these fixtures; as a result, inspection time was cut in half, speeding turnaround and decreasing downtime significantly.
Aerospace manufacturers employed automatic checking fixtures to ensure component assembly precision, leading to reduced defects and compliance with stringent safety regulations, which in turn led to greater customer satisfaction and trustworthiness.
Consumer electronics firm also took advantage of this technology and experienced increased throughput while upholding rigorous accuracy standards, leading them to experience cost savings over time. Their adoption not only streamlines operations but has also resulted in cost reduction.
These examples demonstrate how automatic checking fixtures have revolutionized various industries by going far beyond traditional quality control measures.
Challenges and Limits of Automatic Checking Fixtures
Automated checking fixtures offer many benefits; however, their setup cost can be prohibitively expensive for smaller manufacturers.
Integration can present its own set of difficulties. Many facilities possess outdated equipment which may prevent new fixtures from fitting effortlessly into their facility’s infrastructure – leading to additional downtime or interruption during implementation.
Furthermore, maintenance and calibration must take place regularly to keep automatic checking fixtures operating at their maximum performance. Expertise in technical maintenance must also be available if the systems need to function at peak levels.
Adaptability is also a concern; as product designs evolve, automatic fixtures must be updated or changed out regularly in order to remain accurate – which adds complexity to operations.
Technology dependence creates concerns over potential failures or malfunctions that could shut down production lines and create delays throughout the supply chain.
Future of Quality Control with Automated Checking Fixtures
Quality control’s future looks bright with the use of automated checking fixtures, becoming smarter through artificial intelligence and machine learning innovations.
Imagine a production line where every component is monitored real-time to detect and predict defects as soon as they appear, cutting downtime while increasing overall productivity. Automatic checking fixtures would not only detect flaws but also anticipate potential failures before they happen – creating an efficient production cycle while decreasing downtime and increasing overall efficiency.
As manufacturers embrace Industry 4.0 principles, their fixtures can easily connect with smart devices on the shop floor and use data collected during inspections to inform design processes for continuous improvement.
Customizability provides companies with greater ability to tailor automatic checking fixtures to specific products or fluctuating market needs, adapting these essential tools as technology changes so as to stay at the forefront of manufacturing innovation while upholding quality control as an essential aspect.
Conclusion
Quality control has long been considered essential to successful manufacturing. As industries change and adapt their tools and techniques for maintaining standards are met, so too do their tools and techniques – and automatic checking fixtures represent one major advancement on this long journey towards quality.
Precision, efficiency and cost effectiveness are revolutionizing how manufacturers approach quality assurance. Companies adopting such advanced solutions can streamline processes while decreasing errors and wastefulness.
Implementing automatic checking fixtures may present some initial costs and training requirements; however, their long-term advantages typically outweigh these hurdles. Real world examples demonstrate this point – businesses across various sectors have seen tangible benefits after adopting these systems into their production lines.
Looking towards the future, quality control’s future appears promising with automatic checking fixtures leading the charge. As technology develops further, more advanced solutions may become available that further improve precision and reliability within manufacturing processes.
Automation isn’t simply about keeping pace; it sets new benchmarks of quality control excellence, which could ultimately shape manufacturing success in future eras. By adopting automation solutions now, businesses may well see success emerge at once!
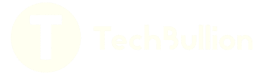