In the fast-paced world of manufacturing, the advent of collaborative robots (cobots) specifically designed for welding tasks represents a significant technological leap. These innovative machines work alongside humans to enhance productivity, safety, and precision. This guide explores the transformative potential of a welding cobot in modern manufacturing settings, offering insights for manufacturers, engineers, and tech enthusiasts looking to understand and leverage this cutting-edge technology.
Introduction to Welding Cobots
At the heart of the latest industrial revolution are cobots, a breakthrough in robotic technology designed to collaborate with human operators. Unlike traditional robots, which require significant safety measures and operate in isolation from human workers, cobots are built to work alongside them, enhancing human efforts without replacing them. This synergy is particularly impactful in welding, where precision, consistency, and safety are paramount.
The Evolution of Welding Technology
The history of welding technology is a testament to human ingenuity, evolving from ancient forge-welding processes to sophisticated automated systems. The emergence of welding cobots marks the latest chapter in this evolution. They represent the culmination of advancements in robotics, artificial intelligence, and machine learning, offering a level of flexibility, efficiency, and safety that traditional welding methods and automation technologies couldn’t achieve.
Understanding the Benefits of Welding Cobots
Welding cobots bring a host of benefits to the manufacturing table, three of which stand out most prominently: efficiency, safety, and precision.
- Efficiency: Cobots can operate continuously, reducing downtime and increasing production rates. Their ability to quickly adapt to different tasks also cuts down on the time and costs associated with retooling and reprogramming.
- Safety: Designed to work near humans, cobots are equipped with advanced sensors and safety features to prevent accidents. This reduces the risk of injuries associated with manual welding tasks.
- Precision: With superior control and steadiness, cobots achieve a level of precision in welding that is challenging for even the most skilled human welders, ensuring high-quality welds consistently.
Implementing Welding Cobots
Introducing welding cobots into a manufacturing environment entails several practical steps:
- Assessment: Evaluate the specific welding tasks to determine the suitability of cobots. This includes considering the types of materials, the complexity of welds, and the production volume.
- Selection: Choose the right cobot model based on payload, reach, and capabilities. Partnering with a reputable vendor can provide valuable guidance.
- Integration: Seamlessly integrate cobots into the existing workflow, which may involve training staff and fine-tuning cobot programming to suit specific tasks.
- Compliance: Ensure compliance with industry standards and safety regulations to maximize the benefits of cobot implementation.
Industry Applications
Welding cobots have found applications across a variety of sectors, from automotive to aerospace and beyond. In the automotive industry, for example, cobots are used to weld car parts with unparalleled speed and precision, streamlining production lines while maintaining high-quality standards. Similarly, in aerospace, cobots contribute to the manufacturing of aircraft components, where precision and reliability are crucial.
The Future of Manufacturing with Cobots
The future of manufacturing with cobots looks promising, with ongoing advancements in AI and robotics poised to enhance their capabilities even further. Predictions for the field include increased versatility, allowing cobots to handle more complex welding tasks, and improved user interfaces, making them accessible to a broader range of operators. The integration of cobots into digital manufacturing networks is also expected, enabling smarter, more connected factories.
Conclusion
Welding cobots represent a revolutionary step forward in manufacturing technology, offering improvements in efficiency, safety, and precision that far exceed traditional methods. As the industry continues to evolve, the adoption of cobots is set to become a defining feature of modern manufacturing facilities, signaling a new era of human-robot collaboration. For manufacturers, engineers, and tech enthusiasts, the time to explore the capabilities and potential of welding cobots is now, paving the way for a more innovative, productive, and safe manufacturing environment.
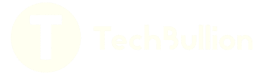