The rapid advancement of industrial technology has paved the way for groundbreaking innovations in predictive maintenance. This article, based on research by Karthikeyan Rajamani, explores how the integration of Internet of Things (IoT) sensors and acoustic analysis is transforming industrial equipment management. These innovations are reducing downtime, optimizing costs, and enhancing efficiency across various industries.
The Rise of IoT in Predictive Maintenance
Traditional maintenance strategies, such as reactive and preventive approaches, often result in unexpected breakdowns or excessive costs. IoT-enabled predictive maintenance has changed this landscape by introducing real-time monitoring. Sensors embedded in industrial equipment continuously collect data on temperature, pressure, vibration, and electrical currents, allowing industries to detect anomalies before they lead to failure. This transition towards a data-driven maintenance model minimizes disruptions and improves operational reliability.
Real-Time Data Collection for Proactive Maintenance
One of the primary advantages of IoT technology is its ability to facilitate real-time data collection and transmission. Sensors communicate through wireless protocols like Wi-Fi and Bluetooth, ensuring seamless data flow to centralized processing systems. With edge computing, data can be analyzed closer to its source, reducing latency and enabling faster decision-making. This capability allows maintenance teams to proactively address potential issues, preventing costly breakdowns and enhancing overall efficiency.
Advanced Analytics: A Game Changer in Industrial Monitoring
The power of predictive maintenance lies in advanced analytics, which applies machine learning algorithms to detect early signs of failure. These systems compare real-time data with baseline metrics, identifying irregular patterns that might indicate equipment malfunction. The ability to recognize subtle deviations in vibration levels or power consumption helps maintenance teams take action before significant damage occurs. This data-driven approach leads to substantial cost savings and extends equipment lifespan.
Acoustic Monitoring: A Non-Invasive Diagnostic Tool
An innovative addition to predictive maintenance strategies is the use of acoustic monitoring. By analyzing the sounds produced by machinery, this technique can detect irregularities such as bearing wear, motor misalignment, or loose components. Unlike traditional sensors that require direct contact with equipment, microphone-based monitoring systems offer a non-invasive solution, making them particularly useful for older machinery where physical modifications may not be feasible.
Combining IoT Sensors and Acoustic Analysis
The integration of acoustic monitoring with traditional IoT sensor data has created a more comprehensive predictive maintenance system. By cross-referencing acoustic patterns with temperature and vibration data, maintenance teams gain a deeper understanding of potential failures. This combination enhances fault detection accuracy and provides actionable insights for optimizing maintenance schedules. The synergy between these technologies ensures that industries can maximize equipment uptime and minimize unexpected failures.
Industrial Applications of Predictive Maintenance
Industries such as manufacturing, energy, and logistics have significantly benefited from predictive maintenance solutions. In manufacturing, IoT sensors help monitor production machinery, ensuring optimal performance while reducing unplanned downtime. The energy sector relies on predictive maintenance for monitoring turbines, generators, and transformers, preventing power outages and improving efficiency. In logistics, fleet management systems leverage IoT data to track vehicle health, reducing breakdowns and improving delivery timelines. Across these industries, predictive maintenance is proving to be a game-changer in operational efficiency.
Challenges in Implementing IoT and Acoustic Monitoring
Despite its numerous benefits, the adoption of predictive maintenance technologies comes with challenges. Integrating IoT systems with legacy equipment can be complex and expensive. Additionally, managing the vast amount of data generated by sensors requires robust analytics infrastructure. Cybersecurity risks also pose a concern, as interconnected systems become potential targets for cyber threats. Moreover, organizations need skilled professionals to interpret data insights effectively and drive maintenance strategies.
Future Prospects: AI and Digital Twins in Predictive Maintenance
The future of predictive maintenance is set to be even more transformative with the integration of artificial intelligence (AI) and digital twins. AI-powered analytics can improve the accuracy of failure predictions, while digital twins—virtual replicas of physical assets—enable real-time simulations to optimize maintenance strategies. The adoption of augmented reality (AR) tools for equipment repairs is also expected to enhance technician efficiency. As these technologies continue to evolve, predictive maintenance will become even more efficient, cost-effective, and accessible across industries.
In conclusion ,The fusion of IoT and acoustic analysis has redefined industrial maintenance, bringing unprecedented efficiency, reliability, and cost savings. As industries embrace predictive maintenance, they gain a competitive edge by reducing downtime and extending equipment longevity. While challenges remain, ongoing advancements in AI, machine learning, and digital twins promise an even more sophisticated future for industrial maintenance. Karthikeyan Rajamani underscores the critical role of these innovations in shaping the next generation of industrial operations, ensuring a smarter and more resilient manufacturing landscape.
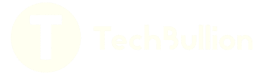