The automotive industry is undergoing an unprecedented transformation driven by digital technologies and Industry 4.0 principles. Kumar Rajiv Nayan, an expert in smart manufacturing, explores these advancements and their profound impact on the industry. His analysis sheds light on the technologies reshaping production efficiency, quality control, and supply chain agility.
The Rise of Smart Manufacturing
The integration of smart manufacturing technologies is redefining automotive production. Implementing automation, artificial intelligence (AI), and the Internet of Things (IoT) has streamlined operations, resulting in faster production cycles, improved quality assurance, and cost reduction. By leveraging interconnected systems, manufacturers can respond dynamically to market demands, reducing product development time and maintenance costs. This evolution ensures that companies remain competitive in a digitalized global market.
Digital Twin Technology: A Game Changer
Digital twin technology is a pivotal innovation in the automotive industry. These virtual models replicate physical assets, allowing real-time monitoring and process optimization. Manufacturers using digital twins have experienced reduced development cycles and a boost in efficiency. This technology enhances predictive maintenance, with AI-driven models achieving high accuracy in predicting equipment failures and minimizing costly downtime. Digital twins are also leveraged to refine vehicle design and test manufacturing methodologies before real-world implementation.
Advanced Manufacturing Systems Integration
Modern automotive plants are integrating Manufacturing Execution Systems (MES) to enhance efficiency. These systems synchronize thousands of sensors and actuators, increasing productivity and declining defect rates. Edge computing accelerates data processing, reducing decision-making latency. Cloud-based platforms optimize scheduling and resource allocation, improving energy efficiency. Integrating AI-driven analytics into these systems has improved production planning, reducing bottlenecks and enabling real-time decision-making.
Addressing Legacy System Challenges
While digital transformation brings numerous benefits, integrating legacy systems remains a challenge. Many manufacturers operate with systems over two decades old, leading to delays and budget overruns. Efforts to standardize data formats through AutomationML and OPC UA have successfully reduced communication latencies and enhanced system reliability. As industries transition to smart factories, bridging the gap between outdated and modern systems remains crucial.
Strengthening Cybersecurity in Manufacturing
With increased connectivity comes heightened cybersecurity risks. The automotive sector has seen a surge in cyber threats over recent years. Implementing network segmentation, multi-factor authentication, and encrypted communication has significantly reduced unauthorized access attempts and data breaches. Continuous security monitoring has improved threat detection times, reducing response durations. Cybersecurity strategies also focus on proactive threat intelligence, utilizing AI to predict and prevent breaches.
Bridging the Workforce Skills Gap
The shift toward digital manufacturing necessitates workforce upskilling. Many manufacturers struggle to find skilled professionals in data analytics and automation programming. Companies investing in training programs report a rise in productivity and a reduction in integration-related issues. Employees trained in digital manufacturing technologies contribute to a higher success rate in innovation implementation. Upskilling initiatives enhance operational efficiency and boost employee retention and job satisfaction.
The Future of Automotive Manufacturing
Emerging technologies such as additive manufacturing, AI-driven defect detection, and software-defined vehicle production are shaping the future of automotive manufacturing. The adoption of 3D printing drives efficiency, cutting prototype development time and reducing material consumption. Predictive maintenance systems utilizing machine learning minimize unplanned downtime, saving manufacturers millions annually. Future advancements in quantum computing and blockchain could revolutionize supply chain management, ensuring transparency and security.
The Shift to Software-Defined Vehicles
Modern automotive production embraces software-driven methodologies, enabling flexible assembly lines that simultaneously accommodate multiple vehicle models. This shift has led to improved throughput and quality control. Over-the-air (OTA) updates have further transformed the industry, ensuring continuous software optimization. Software-defined architectures pave the way for autonomous driving capabilities, enhancing vehicle performance and safety.
In conclusion, the automotive industry’s digital transformation redefines manufacturing practices, enhances efficiency, and drives innovation. While challenges such as legacy system integration and cybersecurity threats persist, the industry’s continued evolution relies on adopting advanced technologies and workforce training. As Kumar Rajiv Nayan highlights, staying ahead in this dynamic landscape requires adaptability and a commitment to digital excellence. Companies embracing these changes will lead the future of automotive manufacturing, setting new standards for sustainability, efficiency, and customer-centric solutions.
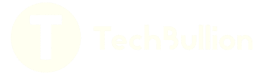