Extruder gearboxes are essential components in many industrial processes. They facilitate the transmission of power and torque from a motor to an output device such as a conveyor or pump. However, these gearboxes can generate a lot of noise during operation, adversely affecting workplace safety and productivity. This article will explore techniques for reducing noise levels in extruder gearboxes.
Causes of Noise in Extruder Gearboxes
The noise generated by extruder gearboxes is caused by various mechanisms, which include gear meshing, bearing vibration, and gear resonances. Gear meshing occurs when the teeth of two gears engage and disengage, producing a “clicking” or “whirring” sound. Bearing vibration occurs when the bearings that support the gears and shafts vibrate at their natural frequency, creating a “humming” sound. Gear resonances occur when the natural frequency of the gears and gearbox housing matches the operating frequency of the gearbox, resulting in a “ringing” sound.
Several factors contribute to the noise levels in extruder gearboxes, including the design of the gears and gearbox housing, the type of lubricant used, and the operating conditions of the gearbox. For instance, well-designed gears may generate more noise than well-designed gears. Using a lubricant with high viscosity may increase noise levels by generating more friction between the gears and bearings. It is also worth noting that operating conditions, such as the speed and torque of the gearbox can affect noise levels. Therefore, it is crucial to consider these factors when designing and operating extruder gearboxes to minimize noise levels.
Techniques for Noise Reduction in Extruder Gearboxes
There are various techniques available for reducing noise levels in extruder gearboxes. These techniques include using sound dampening materials, designing quieter gears, and proper lubrication and maintenance practices.
- Sound dampening materials effectively reduce noise levels by absorbing or reflecting sound waves, preventing them from transmitting from the gearbox to the surrounding environment. Common sound dampening materials used include rubber, foam, and fiberglass. These materials can be applied to the gearbox housing, gear teeth, and bearings to reduce noise levels.
- Designing quieter gears is another effective technique for reducing noise levels in extruder gearboxes. Gears can be designed to minimize noise by modifying their tooth profile, tooth spacing, and gear material. For instance, helical gears are quieter than spur gears because they engage more gradually, reducing the “clicking” sound produced by gear meshing.
- Proper lubrication and maintenance practices are also crucial for reducing noise levels in extruder gearboxes. Lubricants with low viscosity and high film strength can reduce friction between gears and bearings, lowering noise levels. Regular maintenance, including cleaning and inspection of gears and bearings, can help
- identify and address potential noise sources before they become more significant problems. It is important to note that following proper lubrication and maintenance practices can also help extend the gearbox’s life, thereby reducing the need for costly repairs or replacements.
Case Studies of Successful Noise Reduction
Numerous industrial applications have adopted noise reduction techniques in their extruder gearboxes to enhance their operations. A food processing company, for instance, reduced noise levels by utilizing sound-absorbing foam on the gearbox housing. This foam effectively absorbed and reflected sound waves, which minimized the amount of noise transmitted from the gearbox to the surrounding environment. Consequently, this improved workplace safety and productivity, as employees were not exposed to excessive noise.
Another successful technique a company implemented was using a lubricant with lower viscosity. Lubrication reduces noise levels in extruder gearboxes by minimizing friction between the gears and bearings. By choosing a lubricant with a lower density, the friction between the gears and bearings was reduced, resulting in reduced noise levels.
In addition, a mining company adopted quieter gear designs to reduce noise levels in their extruder gearboxes. They modified their gears’ tooth profile and spacing and replaced their steel gears with plastic ones. The new plastic gears were much quieter due to their low resonant frequency and better dampening properties, significantly reducing noise levels during operation.
These case studies show that combining different noise reduction techniques can lead to successful outcomes in reducing noise levels in extruder gearboxes. It is essential to assess the needs and requirements of individual applications and adopt techniques accordingly to achieve optimum results.
Conclusion
Reducing noise levels in extruder gearboxes is essential for maintaining workplace safety and productivity. Techniques for reducing noise levels include using sound dampening materials, designing quieter gears, and proper lubrication and maintenance practices. These techniques have been successfully implemented in industrial applications and can help to reduce noise levels and prolong the lifespan of extruder gearboxes. By implementing these techniques, industrial processes can ensure that their extruder gearboxes operate at optimal performance levels and achieve maximum lifespan while minimizing the negative impact of noise on the workplace.
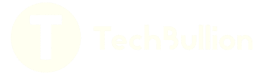