Rapid prototyping has essentially become synonymous with additive manufacturing and three-dimensional printing in recent years. The term “rapid prototyping” refers to a group of processes that are used to create a scale model of a real-world product by employing data from a three-dimensional computer-aided design (CAD) file. Because these processes provide a prototype that is close to the finished product with a small amount of time and money, the terms additive manufacturing and three-dimensional printing have basically become synonymous with rapid prototyping.
Traditional prototyping was prohibitively expensive when it was done well, and it was functionally useless when it was done with makeshift proof-of-concept models and basic tools. This is one reason why rapid prototyping has gained popularity in recent years. To put it simply, if you wanted to make a good prototype, you had to spend almost as much money on it as you did on the actual thing. On the other hand, if you wanted to make a cheaper prototype, it was not worth your time or money because it did not resemble the actual thing. The significance of rapid prototyping services for product designers and engineers in a wide variety of manufacturing sectors today is expected to continue to increase. The following is a list of the top ten suggestions for reducing the cost of rapid prototyping as well as the lead time involved.
1. Would your company benefit from utilizing rapid prototyping as a service?
Rapid prototyping is the right move for companies in the manufacturing and software industries that need to show proof of concept before a large rollout of their product. It can produce a scaled-up prototype of high quality and speed very quickly without breaking the bank.
2. Determine which types of technology and machinery will work best for your project.
Determine what aspects of your prototypes are the most essential, and then select the appropriate tools for the endeavor. If the overall prototype is more important than the specific details, you should concentrate on finding equipment that can produce the most accurate product in the shortest amount of time. If attention to detail is your top priority, you should look for the machinery that can produce the prototype of the highest possible quality.
3. Make your components hollow if they are able to perform their intended functions while in this state
If a prototype has hollow parts, it allows you to create a general idea of what the final product will look like and how it will function at a fraction of the cost of producing a solid model. You will be able to create a high-quality prototype using fewer raw materials if you are aware that the hollow parts will not be hollow when it comes time to produce them. This will lead to a reduction in the amount of money spent, the amount of work done by the machinery, and the amount of time required to finish the project.
4. Make improvements to the design
It is important to pay attention to the details, such as by adding air holes to hollow designs, getting rid of angled walls, using wall thickness that is greater than the minimum specifications, etc. You can avoid the headaches associated with creating a good prototype by first optimizing the design of the prototype.
5. When it is possible to do so, automate the post-processing steps involved in three-dimensional printing
You should consider using post-processing automation rather than doing everything by hand if it is possible to do so. Post-processing is an essential but time-consuming step, and it is critical to take advantage of any opportunity to cut down on the amount of work and effort required.
6. Instead of printing the entire product all at once, assemble larger parts by combining multiple smaller prints into a single larger one.
It is easier, in the long run, to print small jobs and then assemble them later than it is to print an entire product and then have a post-processing nightmare. Printing small jobs and then assembling them later. By assembling the work in stages, you can reduce the likelihood of making mistakes and maintain quality control more easily throughout the production process.
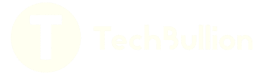