When it comes to electronics design, prototyping and production are two critical phases, each serving distinct purposes. Navigating these stages effectively can make a significant difference in terms of efficiency, quality, and cost-effectiveness. Below, we’ll break down the unique goals, processes, and considerations of prototyping and production, offering insights for companies aiming to transition seamlessly from one phase to the other.
What is Electronics Design Prototyping?
Prototyping is an initial, iterative stage in electronics design that allows engineers and designers to test the functionality, usability, and feasibility of a concept. The prototype serves as a preliminary model, representing a working version of the intended design but not yet optimized for large-scale production. Prototyping enables companies to explore multiple design possibilities, identify potential issues, and refine the product before committing significant resources.
Key Characteristics of Prototyping
- Flexibility: Prototyping allows for rapid changes and adjustments based on real-time feedback and testing.
- Cost-Effective Iteration: Components in prototypes may not be final, and certain shortcuts may be used to save time and costs.
- Focus on Testing: Prototyping emphasizes testing for design flaws, usability, and potential functionality issues.
- Quick Production Time: Prototypes are generally produced quickly, allowing design teams to analyze and iterate on designs in a timely manner.
Types of Prototypes
- Proof of Concept (PoC): A basic model to test the core functionality of the design.
- Form and Fit Prototype: Evaluates how well the product fits into its intended space or environment.
- Functional Prototype: A fully operational version that closely fight resembles the final product, though often built with different materials.
Moving from Prototyping to Production
After a prototype proves successful and meets all specified requirements, it’s time to shift focus from exploration to execution. The production phase transforms a well-tested prototype into a scalable, market-ready product. This transition requires careful planning, considering aspects such as cost efficiency, durability, reliability, and the logistics of manufacturing at scale.
Key Differences Between Prototyping and Production
Aspect | Prototyping | Production |
Goal | Testing and refining design | Consistent, scalable manufacturing |
Materials | Temporary, less expensive substitutes | High-quality, durable materials |
Production Scale | Small, limited quantities | Large-scale, optimized for mass production |
Time and Flexibility | Quick adjustments and iterations | Established, repeatable processes |
Cost Management | Focus on speed over cost | Cost efficiency through volume production |
Key Considerations When Moving to Production
- Component Selection: Production-grade components are chosen for durability, efficiency, and cost-effectiveness. This is a crucial step, as materials must be of a standard suitable for long-term use.
- Supply Chain Optimization: Establishing a reliable supply chain for sourcing production components is essential. The right suppliers can deliver components on time, in the right quantities, and at reasonable costs.
- Quality Assurance and Testing: Production necessitates rigorous quality control procedures. Each unit must meet the design’s specifications without the variances tolerated during prototyping.
- Regulatory Compliance: Unlike prototypes, production models often need to comply with industry standards, regulatory requirements, and certifications, depending on the market and product type.
- Scalability and Cost Efficiency: Manufacturers strive for methods that minimize waste, streamline processes, and ensure scalability, balancing quality and cost.
Prototyping to Production: Common Pitfalls to Avoid
The transition from prototyping to production isn’t always seamless, and it’s essential to be aware of potential pitfalls that can disrupt the process:
- Overlooking Design Adjustments: Prototypes may have design elements that don’t translate well to large-scale production. For example, materials used in prototyping may not meet durability requirements at a mass-production level.
- Neglecting Testing Adjustments: Prototypes are tested for functionality, but production units need consistent performance across every batch. This often requires reevaluation of testing methods.
- Underestimating Costs: Production costs involve expenses that were negligible in the prototyping stage. Planning for additional manufacturing costs, such as tooling, labor, and logistics, is essential.
- Ignoring Time Constraints: Production timelines are often longer due to the need for sourcing, manufacturing, and assembly at scale. Rushing to production can lead to quality issues, so factoring in realistic timelines is critical.
Tips for a Successful Transition
- Plan for Scale from the Start: Design prototypes with scalability in mind, considering materials and components that can transition smoothly to production.
- Maintain Clear Communication: Cross-functional teams, including design, engineering, and manufacturing, should collaborate from prototyping through to production.
- Leverage Simulation and Modeling: Using simulations can reveal design flaws and test functionality without the need for physical prototypes, saving time and resources.
- Document Changes Meticulously: Document all changes made during prototyping to ensure they are accurately reflected in the production process.
Conclusion
Both prototyping and production are essential phases in electronics design, each with its unique goals and methods. Prototyping focuses on experimentation, functionality, and rapid iteration, while production emphasizes consistency, quality, and scalability. By understanding the core differences and planning thoughtfully for the transition, companies can ensure a smooth journey from initial concept to final product.
For anyone in electronics design, managing the shift from prototyping to production is about balancing innovation with reliability, creating products that not only meet market demands but also achieve commercial success.
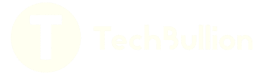