1. Proportion of Molds in Automotive Development Costs
Overall Proportion Range
The average mold costs typically represent 15%-30% of the total vehicle development costs, with the exact percentage depending on the model positioning and production processes.
∙ Economy Vehicles: Account for about 15%-20%. In these vehicles, design and production processes are usually simpler, and costs are reduced by shared molds and simpler designs. For example, some economy sedans make use of shared platforms and molds, which eliminates the need to develop new molds for each model, and thus, saves a lot of development costs.
∙ Mid-to-High-End Vehicles: Account for 20%-25%. The higher mold costs are due to these vehicles having more complex designs and more customized components. As an example, luxury vehicles have body and interior parts that need high-precision durable molds that may need several rounds of fine-tuning and adjustment.
∙ New Energy Vehicles (NEVs): Account for 25%-30%. Due to the increasing demand for the specialized components such as battery housings and motor housings, the mold cost proportion of NEVs is normally higher than the traditional internal combustion engine vehicles. For example, electric vehicle battery packs need high-strength molds to guarantee safety, and motor casting molds demand an extremely high precision.
Cost Breakdown by Process
Mold costs occur usually in these production processes:
∙ Stamping Molds (50%-60%): The material mostly serves to create body parts like doors, hoods, and side panels. Stamping molds need exceptional precision and strength in mass production so their production costs stay high. BMW and Mercedes-Benz need expensive and difficult-to-produce high-precision stamping molds to make their body parts.
∙ Injection Molds (20%-25%): The material serves to create elements inside the vehicle like dashboard parts and seats while lighting equipment. When car interiors grow more intelligent and luxurious manufacturers need more advanced injection molds because they make high-end parts that contain such functions as hidden air vents and multifunctional displays.
∙ Casting Molds (10%-15%): These materials form the basis of engine blocks and transmission units plus other metal details. The production of casting molds demands both heat tolerance and exactness which leads to expensive mold expenses. The exact dimensional control and structural stability of molds matter most for high-performance engine and transmission parts.
∙ Other Molds (5%-10%): Use rubber sealing elements and carbon fiber parts in your production. The automotive industry now needs carbon fiber composite materials to meet environmental goals which makes mold production more challenging and expensive.
2. Core Factors Affecting Mold Costs
Model Complexity
∙ Body Design Complexity: The more complex the body’s curves, the higher the stamping mold cost. Molds needed for sports sedans and similar models with complex curves increase mold expenses significantly. Companies need to make more mold parts for smooth body designs which increases production expenses.
∙ Interior Design Complexity: Interior design development and luxury features make interior parts more challenging to produce. The injection molds for these advanced components need better precision because they appear in luxury vehicle interiors.
Materials and Processes
∙ High-Strength Steel and Aluminum Alloys: The automotive sector now needs more high-strength steel and aluminum alloys which drives up both mold production expenses and production methods. The precise battery pack and electric drive system molds for NEVs demand better materials which raises mold production expenses across the board.
∙ Integrated Die-Casting Technology: Many car manufacturers use integrated die-casting to cut component count and improve production methods. Tesla produces the Model Y rear body part using one large 6000-ton die-casting machine that combines multiple components into a single part. By combining multiple components into a single mold the production expenses increase substantially.
Production Scale
∙ Advantages of Mass Production: Companies that produce more units each year pay for their molds across many items and lower their production expenses for each item. When manufacturers produce more units they use their molds better and pay less per product. Volkswagen shares its mold designs across different models through its modular platform system to cut development and manufacturing expenses.
∙ Challenges of Low-Volume Models: The small number of units produced from low-volume models makes it hard to spread mold expenses across many items thus increasing mold costs as a percentage of total production costs. Mold expenses take up a large percentage of production costs when making customized low-volume and limited-edition products.
Supply Chain Strategy
∙ Domestic vs. Imported Mold Procurement : International molds cost 30% to 50% more than home-made molds particularly for exacting and intricate mold designs. Top brand companies and NEV makers choose imported molds because they deliver exact and high-quality results. Mercedes-Benz and BMW depend on German and Japanese mold manufacturers because these companies need precise and durable mold components.
∙ Modular Design and Mold Sharing: Automakers use common parts to lower their mold expenses. When car companies exchange mold and component plans they use their equipment better which cuts development expenses. Toyota uses its TNGA platform to cut expenses because it lets the company repeat mold and component designs in multiple vehicle models.
3. Cost Reduction Strategies for Automakers
1. Design Optimization
Automakers achieve reduced mold costs by simplifying their mold designs and requiring fewer units. Automakers reduce their mold requirements by designing products that simplify production while requiring fewer components. Modern vehicle door handles use electric and hidden designs which improve vehicle aesthetics without requiring mold production. Manufacturers achieve mold cost reduction by combining multiple parts into single modules which simplifies their production methods. The application of parametric modeling enables startup testing of various product variations through mathematical designs which accelerates the development of molds and subsequent product creation.
2. Process Innovation
Process innovation serves as automakers’ primarymethod to minimize their operational costs. Companies that implement3D printing technology for mold fabrication reduce development tasks while saving money during mold prototyping stages. Automakers employ rapid prototyping techniques to inspect their mold designs quickly thus reducing costs associated with redoing physical molds. Through virtual mold testing technology companies can predict mold formation processes digitally before major expenses are spent through digital simulations. Virtual testing methods enable businesses to reduce their prototyping expenses by 30% thus decreasing product development costs.
3. Supply Chain Collaboration
Better cost management occurs when automakers collaborate closely with mold manufacturers. The collaboration between NIO and LK Technology produced die-casting molds through knowledge exchange and resource sharing thus reducing development costs. Automakers control their steel and alloy material expenses better by handling all purchasing orders from a single location. Our collaborative supply chain partnership helps us lower material expenses and speed up mold production which makes our entire production process more affordable.
4. Future Trends
1. Software-Defined Molds
The frequent use of software-defined molds in mold manufacturing results from continuous advancements in technology.AI systems evaluate real mold usage patterns to predict exact failure times for molds. The system we use reduces maintenance costs while preventing production failures to achieve operational excellence. The deployment of AI systems by these companies allows them to predict mold life duration thus enabling them to conduct preventive maintenance operations that prevent delays and maintain product delivery schedules.
2. Green Molds
As people care about environmental problems more and seek sustainable development methods green molds now get more research interest. Manufacturers in the automotive sector now prefer making molds from recyclable materials as a main industry trend. Bio-based plastics now replace regular plastics for mold production because of their growing popularity. They reduce environmental harm while needing fewer resources during recycling which brings down production expenses. Several car manufacturers now use bio-plastic molds instead of metal molds in their production processes. Although manufacturers spend more at first they earn more from lower waste handling expenses throughout the lifetime of their products because these materials support environmentally friendly practices.
3. Regionalized Supply
The modern global market leads many car manufacturers to design new ways to organize their mold supply chains. Companies now produce molds near their facilities to prevent trade restrictions and import taxes. The US-China trade war has made North American automakers switch to Mexican mold suppliers for their manufacturing needs. Organizing production in local areas lets companies manage expenses effectively and makes their supply network more flexible and resistant to shipping problems. Automakers can deliver products to customers faster when they produce supplies close to their target markets.
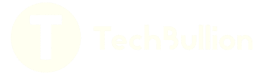