Printed electronics is a rapidly growing field that combines the best of both traditional print and digital technology. It involves the use of printing techniques to create electronic devices, such as sensors, batteries, and displays, on various substrates including paper, plastic, and fabric. This innovative technology has the potential to revolutionize different industries by providing cost-effective and customizable solutions for various applications.
The concept of printed electronics dates back to the 1960s when researchers began exploring ways to print electronic circuits directly onto flexible materials. However, it was only in the past decade that this technology gained significant traction due to advancements in materials science, printing techniques, and manufacturing processes.
How Does Printed Electronics Work?
At its core, printed electronics relies on a combination of conductive ink or paste with traditional printing methods such as screen printing or inkjet printing. These inks are made up of conductive particles such as silver or copper mixed with a polymer binder. The ink is then deposited onto a substrate using specialized equipment that can handle fine lines and detail required for electronic circuits.
After the ink has been deposited onto the substrate, it undergoes curing or drying process where it solidifies into a conductive layer. Additional layers may be added depending on the complexity of the device being created. Once all layers have been printed and cured/dried, any excess material can be removed through etching or laser cutting processes leaving behind functional electronic components.
Definition and Explanation of Printed Electronics
Printed electronics, also known as organic or plastic electronics, is a rapidly growing field that combines the principles of traditional printing techniques with modern electronic technology. It involves using conductive inks or materials to create electronic devices on various substrates such as paper, plastic, fabric, and even glass.
The concept of printed electronics has been around for several decades but has gained significant attention in recent years due to its potential to revolutionize the way we manufacture and use electronic devices. This innovative technology offers a range of benefits such as low-cost production, flexibility in design and manufacturing processes, lightweight and portable devices, and environmentally friendly production methods.
Unlike traditional electronics that are created using complex fabrication processes on rigid materials like silicon wafers, printed electronics utilize simpler techniques that involve depositing thin layers of conductive ink onto flexible substrates. These materials can be easily printed using conventional printing methods like screen printing, inkjet printing, or even roll-to-roll printing.
One of the key components of printed electronics is the use of conductive ink. These inks are formulated with tiny particles of conducting materials like silver or carbon which allow them to carry electrical current. The choice of conductive ink depends on the specific application requirements such as conductivity level, adhesion properties, substrate compatibility, etc
History and development of the technology
The history and development of printed electronics is a relatively recent phenomenon, with its roots dating back to the late 1980s. The technology has evolved greatly over the years, bridging the gap between traditional print and digital technology.
In the early days, printed electronics was primarily focused on producing simple electronic components such as resistors and capacitors using conventional printing techniques like offset lithography and screen-printing. However, with advancements in materials science and nanotechnology, researchers were able to integrate conductive inks made from nanoparticles into these printing processes. This enabled them to create more complex electronic devices such as transistors and sensors.
One major breakthrough in the development of printed electronics came in 1992 when researchers at Xerox PARC developed a new type of inkjet printer that could print conductive patterns onto flexible substrates. This allowed for the creation of bendable circuits, paving the way for applications in flexible displays, RFID tags, and solar cells.
The turn of the century saw a significant increase in research efforts towards developing printable organic semiconductors – materials that can conduct electricity but are also soluble in common printing solvents. This opened up new possibilities for creating fully functional electronic devices using only printing techniques.
Another important milestone was reached in 2003 when researchers at HP Labs demonstrated a process called self-aligned imprint lithography (SAIL) which enabled high-resolution patterning on plastic substrates. This further expanded the potential applications of printed electronics by allowing for finer details to be incorporated
Traditional Printing and Printed Electronics
Printed electronics is a rapidly growing field that combines the capabilities of traditional printing techniques with advanced digital technologies. This has led to the development of new and innovative products that were previously thought to be impossible.
- Printing Process: Both traditional printing and printed electronics involve a similar process of transferring ink onto a substrate. The difference lies in the type of ink used and the level of precision required.
- Flexibility: Traditional printing allows for flexibility in terms of choosing different substrates such as paper, fabric, or plastic. Similarly, printed electronics can also be applied on various flexible substrates like plastic films, papers, fabrics, etc.
- Mass Production: Both techniques are capable of producing large quantities of products at high speeds, making them suitable for mass production.
- Low Cost: Traditional printing methods are known for their cost-effectiveness due to their high-speed production capabilities. Printed electronics also have lower production costs compared to conventional electronic manufacturing processes.
Applications of Printed Electronics
The field of printed electronics has been rapidly growing in recent years, thanks to its potential for revolutionizing the way we interact with technology. By combining traditional printing techniques with modern digital technologies, printed electronics offer a wide range of applications that have the potential to transform various industries. In this section, we will explore some of its most exciting and promising applications.
- Flexible Displays:
Printed electronics have made it possible to create flexible and bendable displays that can be integrated into a variety of products such as clothing, packaging, and even medical devices. These displays are lightweight and can be easily manipulated to fit different shapes and sizes, making them ideal for portable electronic devices.
- Wearable Technology:
With the rise in popularity of wearable technology, printed electronics have become a game-changer in this industry. The flexibility and thinness of these components make them perfect for embedding into clothing or accessories like smartwatches and fitness trackers. This not only makes them more comfortable to wear but also allows for a seamless integration with our daily lives.
- Smart Packaging:
Imagine buying a product from the store that comes with an interactive package – one that provides information about the product or offers personalized promotions? This is where printed electronics come into play by enabling smart packaging solutions that can communicate with consumers through their smartphones or other devices.
- Internet-of-Things (IoT):
The concept of IoT involves connecting everyday objects to the internet so they can communicate with each other, creating a network of smart devices.
Examples of how printed electronics are being used in various industries
Printed electronics, also known as organic or plastic electronics, is a rapidly growing field that combines traditional printing techniques with digital technology to create functional devices. This innovative technology has gained popularity in various industries due to its low production costs, flexibility, and versatility. In this section, we will explore some examples of how printed electronics are being used in different industries.
- Healthcare Industry
One of the most promising applications of printed electronics in the healthcare sector is biosensors. These sensors can be easily integrated into bandages or patches to monitor vital signs such as heart rate, blood pressure, and body temperature. They can also be used for continuous glucose monitoring for diabetic patients. Printed electronics have also been used to develop skin patches that deliver medication through the skin without the need for injections.
- Consumer Electronics
The consumer electronics industry has been quick to adopt printed electronics due to its potential for creating lightweight and flexible devices at a lower cost than traditional methods. For example, flexible OLED displays are made using printed organic light-emitting diodes (OLEDs) on thin plastic sheets instead of glass substrates, making them bendable and shatterproof.
- Automotive Industry
The automotive industry is another sector where printed electronics are gaining traction. The use of touch-sensitive control panels and curved display screens is becoming more prevalent in modern cars, all thanks to printed electronics technology. Additionally, manufacturers are exploring ways to incorporate smart surfaces into car interiors using conductive ink prints.
Potential future uses for the technology
In recent years, there has been a significant increase in the development and adoption of printed electronics. This innovative technology combines traditional print techniques with digital capabilities. It allows for the creation of electronic components and devices on various surfaces such as paper, plastic, and fabric. Currently used mostly in consumer products such as smart packaging and wearables. The potential applications for printed electronics are vast and could revolutionize many industries.
One of the most exciting potential future uses for printed electronics is in the medical field. These sensors could continuously monitor vital signs or deliver medication without the need for invasive procedures. Additionally, printed electronics could also be used to create smart bandages that can detect infections or monitor wound healing.
The automotive industry is another sector that could greatly benefit from printed electronics. The lightweight and flexible nature make them ideal for use in vehicles considering weight reduction for fuel efficiency. Printed sensors can be used to monitor engine performance or airbag deployment systems. Also, touch-sensitive surfaces can enhance driver interaction with vehicle controls. Furthermore, printed batteries may reduce reliance on traditional lithium-ion batteries and reduce overall weight.
Another promising application of printed electronics lies in sustainable energy solutions. Solar cells made with printable materials have already been successfully developed and tested.
Conclusion
Printed electronics is a ground breaking field that bridges the gap between traditional printing and digital technology. Its versatility, cost-effectiveness, and flexibility in design make it applicable across various industries. With ongoing advancements in materials science and manufacturing processes, the potential applications for printed electronics are vast. It offers solutions to complex challenges and open up exciting possibilities for the future. As the technology continues to evolve, we can expect to see even more innovative and transformative uses emerge. Printed electronics is indeed a field to watch as it reshapes the way we interact with technology and the world.
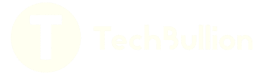