There were around 2.2 million minor and major workplace injuries in the United States in 2021, and 5200 of those were fatal. While it may sound like a lot, it is not half as bad as it used to be only a few decades ago. Back in 1972, there were around 10.9 incidents per every 100 workers, compared to 2.7 in 2021.
That’s because Occupational health and safety training has managed to pull those numbers down over the years. But how does that happen? What’s the role of safety training in the reduction of workplace accidents? Let’s find out.
What Is Occupational Health And Safety Training?
Occupational health and safety training educates workers and supervisors about workplace accidents, risk management, and injury prevention to promote a safety culture. The process includes a variety of training programs that teach the basics of workplace safety.
In the United States, this program is provided by the Occupational Safety and Health Administration (OSHA) under the wing of the U.S. Department of Labor. The purpose of this agency is to provide safety solutions to workplaces, including:
- Worker and supervisor training through online and in-person classes;
- Accreditation and certification for qualified personnel;
- Ensure a safe working environment through a series of inspections.
The safety training programs provided by the organizations teach workers to comply with workplace safety regulations—allowing companies to ensure a safer and hazard-free work culture.
5 Ways Occupational Health and Safety Training Prevents Workplace Accidents
Understanding the basics of occupational health and safety training is just the beginning. In this section, we’re going to explore five ways that safety training impacts workplace safety and prevents incidents. So, let’s dig in.
-
Assessment And Hazard Recognition
Assessing any workplace environment for hazards and the possibility of workplace accidents is a common process for many companies. However, without proper training, neither the workers nor the supervisors can tend to this sort of hazard recognition.
The job site safety rules require a company to tend to any potential hazards to ensure OSHA compliance. Therefore, this shall allow them to:
- Conduct better risk management;
- Thorough emergency preparedness;
- 100% job site safety for workers and supervisors;
- Safety gear and record keeping for safety awareness.
That’s why safety training programs are necessary to ensure not only the well-being of an employee but also the workplace itself. When the entire workforce does this as a single mind, things become easier for both sides, which is why
-
Employee Skill & Knowledge For Safety
Employees work for their pay and dedicate their days to work. That’s why providing them with training and the ability to ensure job site safety is important. However, all workplaces should teach this sort of knowledge or skill at a certification level.
OSHA regulates these rules for all general industry companies so that they can conduct thorough hazard communication with their workers/supervisors and ensure safety awareness throughout the organization. Therefore, the three essential things that safety training helps you with include:
- Training workers and supervisors to prevent workplace accidents;
- Ensure usage of personal protective equipment (PPE);
- Frequent and extensive workplace inspections for injury prevention.
This is a necessary factor regulated by safety committees worldwide—not just in the United States. Therefore, the first step to a truly safe workplace is promoting skills and knowledge among employees.
-
Inclination For Safety Gear & Equipment
As mentioned before, safety gear and equipment are necessary for any general industry company. Using personal protective equipment (PPE) is one of the primary workplace safety regulations that every company must abide by.
But, it’s not just a trend; it’s a necessary aspect of general industry. Thus, safety awareness around it can only be promoted by proper training. Here’s how occupational health and safety training helps with that:
- It teaches the importance of personal safety gear;
- It ensures the usage of proper equipment on-site and on the work floor;
- Usage of equipment for fall protection and electrical safety;
- Hazard communication among workers and their leaders/supervisors/managers.
It’s important to understand that using the proper gear can prevent injuries. In 2022, only around 1% of employees suffered any injuries who were wearing face/head protection. Therefore, the conduct of safety is taught by occupational health and safety, promoting safety gear and equipment and saving lives in the process.
-
Promoting Job Site Safety & Awareness
General safety awareness isn’t just about the type of protective gear that you’re wearing. Or the type of workplace safety that is ensured by your employers. Instead, job site safety is more about employee/supervisor awareness of their surroundings.
This means clearing the area of any potential people who are in the way or could potentially walk by a hazardous area. Or ensuring there’s no one around when they are operating loud machinery—at least not without ear protection (Switch Protection Earplugs).
Besides that, it’s also about being aware of the ergonomics of the machinery, workers, and other on-site equipment that might be a potential hazard. Thus, the basics of occupational health and safety training ensure that employees are aware of their surroundings.
-
Accident Investigation And Hazard Communication
Accidents can happen even in the safest environment. One lapse of judgment or a simple mistake can lead to a catastrophic end. While employers and employees can do all, they need to ensure ether’s always a small percentage of accidents happening, even in the safest work environments.
However, failures like that are opportunities to learn, and that’s when accident investigation and hazard communication is important. Here’s why:
- To prevent any future injuries and accidents;
- To ensure OSHA compliance;
- To avoid potential hazards and mistakes in the future.
Thus, proper training is important in any general industry work, and training your workers can improve the safety culture within your company premises.
Conclusion
These are some of the key factors of occupational health and safety training and how it impacts preventing workplace accidents. This includes preparing employees and supervisors to deal with workplace hazards to ensure a safe environment. It also ensures a workplace that promotes safety gear and PPE, proper training, and prevention of many unfortunate events in any workplace today.
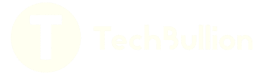