In today’s fast-evolving industrial landscape, where safety, reliability, and efficiency are non-negotiable, Musa Adewoyin is setting a new benchmark in mechanical system integrity. His groundbreaking work on Systematic Review of Non-Destructive Testing Methods for Predictive Failure Analysis in Mechanical Systems offers a bold and forward-thinking framework for enhancing system reliability through early fault detection, hybrid inspection strategies, and intelligent diagnostics.
Adewoyin’s research explores the power of advanced Non-Destructive Testing (NDT) methods such as ultrasonic, radiographic, thermographic, and eddy current testing. When combined with cutting-edge technologies like artificial intelligence, sensor fusion, and digital twins, these methods enable industries to detect wear and degradation before failures happen. This approach dramatically improves safety, reduces downtime, and extends asset lifespans.
Mechanical failure remains a serious global concern, particularly in high-stakes sectors like oil and gas, aviation, transportation, and manufacturing. In regions such as the UK and Europe, where infrastructure safety and regulatory compliance are critical, predictive maintenance has evolved from a best practice into a strategic necessity. Adewoyin’s research meets this demand head-on by advocating for the integration of diverse NDT methods to catch issues like fatigue, corrosion, and delamination early, before they trigger costly, unplanned shutdowns.
Unlike conventional inspection approaches that react to failure after it has occurred, Adewoyin’s framework prioritizes proactive and data-driven strategies. By combining complementary NDT techniques, such as ultrasonic with thermographic testing, he addresses the limitations of relying on a single method. The result is a more holistic and accurate picture of asset health. Additionally, integrating AI and machine learning enables real-time diagnostics and condition monitoring, creating a foundation for intelligent and adaptive maintenance systems. These innovations are especially valuable in environments like offshore oil rigs, energy grids, and aerospace structures, where even minor failures can have catastrophic consequences.
The oil and gas sector, in particular, stands to gain immensely. Equipment failures in this industry not only incur significant financial loss but also pose serious environmental and safety risks. Adewoyin’s hybrid NDT framework, supported by real-time data and predictive analytics, provides operators with a way to anticipate faults in critical assets, from pressure vessels to subsea pipelines, before they escalate. With AI-enabled simulations and digital twins, companies can better understand stress behavior, plan optimal maintenance schedules, and comply with stringent safety regulations, all while extending the life of expensive infrastructure.
What truly sets Adewoyin’s work apart is its foundation in real-world engineering. Between 2007 and 2020, he held senior technical roles in two of the world’s most demanding industrial environments: Coca-Cola HBC and ExxonMobil Nigeria. At ExxonMobil, he led major initiatives to restore high-voltage backup systems and conducted fault diagnostics on diesel generators powering operations that delivered up to 300,000 barrels of oil per day. His focus on condition-based monitoring significantly boosted uptime and system redundancy.
At Coca-Cola HBC, Adewoyin introduced autonomous maintenance practices and tackled recurring electrical and mechanical faults on filling lines, conveyors, and bottle sorters. His efforts streamlined production and enhanced overall efficiency. These hands-on experiences lend a level of credibility and practicality to his research that few academic frameworks can claim. They also demonstrate that his NDT model is not just theoretical, but effective in real-world scenarios.
For the UK, Adewoyin’s contributions are particularly timely. As the nation pursues goals such as decarbonizing its energy grid, expanding rail and transport networks, and embracing Industry 4.0, the need for intelligent and scalable maintenance solutions has never been greater. His hybrid NDT approach supports compliance with British and European safety standards while providing a cost-effective strategy for managing risk, optimizing resources, and enhancing long-term asset performance.
Beyond large corporations, Adewoyin’s work also extends a lifeline to small- and medium-sized enterprises (SMEs). His emphasis on affordable and portable NDT tools and AI-powered diagnostics makes advanced predictive maintenance accessible even to organizations that lack massive inspection budgets. By promoting mobile units and scalable AI solutions, he enables SMEs to enhance operational safety and efficiency without incurring unsustainable costs.
Importantly, Adewoyin’s framework aligns with growing global expectations for sustainability. In an era of heightened environmental awareness, his condition-aware asset management strategies, powered by IoT sensors, real-time data, and machine learning, offer a pathway to reduce carbon emissions, avoid wasteful overhauls, and optimize energy usage.
In conclusion, Musa Adewoyin’s work represents a transformative shift in how industries approach mechanical reliability. His predictive failure analysis framework not only tackles one of the most critical challenges facing modern infrastructure, but it also offers a blueprint for how companies, both large and small, can build safer, smarter, and more sustainable systems. With its unique blend of academic insight and real-world validation, Adewoyin’s research is poised to make a lasting impact across the UK, Europe, and the global industrial community.
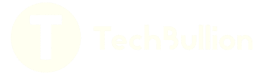