Water-cooled laser welding is revolutionizing the way precision is achieved in various projects. Imagine consistently crafting flawless seams, regardless of the material or thickness involved. With advanced cooling systems, your laser weld processes become more efficient and gain an impressive level of reliability.
Understanding how water-cooled technology enhances welding accuracy and control is essential for any welder. This discussion will highlight the key benefits, effective techniques, and practical tips to refine your welding practices. Prepare to master precision control and elevate your laser welding skills.
Introduction to Water‑Cooled Laser Welding
Water-cooled laser welding uses a cooling system to manage heat during welding. This method keeps laser welders at optimal temperatures, enhancing precision and reducing thermal distortion. Benefits include:
- Consistent Performance: Stable temperatures prevent overheating.
- Versatility: Suitable for various materials and thicknesses.
- Efficiency: Enables faster welding speeds with fewer interruptions.
Advanced cooling systems support flawless seams, improving the quality and reliability of your projects. How can integrating water-cooled laser welders elevate your welding precision?
Fundamentals of Water‑Cooling Technology
Water‑cooling plays a crucial role in laser welders by managing heat efficiently. Proper cooling maintains optimal laser performance and extends equipment lifespan.
Heat Generation & Dissipation
Laser welders produce significant heat from diodes and laser crystals. Water-cooling systems circulate coolant to absorb this heat. Efficient dissipation keeps the laser at a stable temperature, enhancing performance and longevity.
Core System Components
A water‑cooled laser welding machine includes a pump, a heat exchanger, and cooling lines. The pump circulates coolant, the heat exchanger disperses heat, and the lines transport the coolant. These components work together to maintain effective temperature control.
Performance Advantages
Water-cooled laser welders provide enhanced control and reliability. Superior temperature management supports high-precision welding and consistent performance.
Continuous Duty & Power Stability
Water-cooling allows continuous operation without performance drops. Lasers maintain power stability over extended periods, ensuring reliable welding processes.
Weld Quality & Productivity
Precision control improves weld quality. Low laser power, reduced welding speed, and minimal gap size enhance bead surface quality. Stable thermal environments increase productivity and lower rework rates.
Design & Integration Considerations
Water-cooled laser welders provide high cooling efficiency and precise temperature control, ensuring stable laser output for accurate welding.
Portability & Footprint
Water-cooled laser welders require more space for cooling units and plumbing, which limits portability compared to air-cooled systems. However, newer models offer more compact designs, although they remain larger than their air-cooled counterparts.
Maintenance & Reliability
Regular maintenance keeps cooling circuits free from contaminants and scale. Clean the system periodically to maintain efficiency and prevent overheating. Reliable performance extends the laser welder’s lifespan by reducing the risks of damage from inconsistent cooling.
Environmental & Energy Factors
Water-cooled systems use more energy for pumps but provide better cooling efficiency. They rely on water, minimizing the use of refrigerants and reducing environmental impact. Proper disposal and recycling of cooling water are essential to maintain eco-friendly operations.
Application Examples
Water-cooled laser welders excel in various applications by providing precise control and consistent performance.
Industrial Sectors
- Automotive Industry: Welds engine parts and body panels with high accuracy.
- Aerospace Industry: Joins titanium and aluminum alloys securely.
- Medical Device Manufacturing: Assembles surgical instruments and implants.
- Electronics Manufacturing: Fuses small, intricate components efficiently.
Material Range
Material Type | Examples | Benefits |
---|---|---|
Metals | Magnesium alloys, aluminum, titanium, and steel | High strength and durability |
Alloys | Complex mixtures requiring consistent temperature | Prevents thermal damage |
Thin Materials | Sheets, foils | Precise welding without overheating |
Water-cooled laser welders handle diverse materials, ensuring quality welds across different industries.
DenaliWeld Water‑Cooled Product Highlights
DenaliWeld’s 1500W Laser Welder delivers high power with efficient water cooling.
Features:
- Power Output: 1500 Watts ensures strong welds
- Cooling System: Superior water cooling dissipates heat effectively
- Stability: Maintains consistent laser performance during continuous operation
- Temperature Control: Precise management reduces thermal damage
Specifications:
Specification | Details |
---|---|
Power | 1500 W |
Cooling Type | Water-cooled |
Materials | Metals, Alloys |
DenaliWeld laser welders support high-precision projects, enhancing weld quality and reliability.
Best Practices for Maximizing Efficiency
Enhance your water-cooled laser welders’ performance with these best practices.
Coolant Management
Maintain coolant between 5°C and 35°C to avoid power drops and equipment damage.
Filter water and monitor pressure for stable operations.
Use quality chiller materials and perform routine maintenance for consistent temperature control.
Preventive Maintenance
Use 100% U.S.-made control chips in your laser welders for reliability.
Incorporate advanced safety features to protect users.
Regularly check chiller status and coolant temperature.
Schedule maintenance to prevent damage and ensure optimal performance.
Comparative Snapshot: Water‑Cooled vs. Air‑Cooled Laser Welders
Choosing the right laser welder depends on your specific needs. Here’s a quick comparison to help you decide which cooling system suits your projects best.
Water-Cooled
Water-cooled laser welders offer precise temperature control, enhancing weld quality. They maintain optimal performance during continuous operation and are ideal for high-power, intricate tasks. Advanced cooling systems prevent thermal distortion, ensuring strong and consistent welds.
Air-Cooled
Air-cooled laser welders are simpler and cost-effective. They require less maintenance and are suitable for lower-power applications. But, they may struggle with temperature stability during extended use, making them less ideal for high-precision or demanding industrial projects.
Comparison Table
Feature | Water-Cooled Laser Welders | Air-Cooled Laser Welders |
---|---|---|
Temperature Control | Precise and stable | Less precise |
Maintenance | Higher requires coolant management | Lower, simpler upkeep |
Cooling Efficiency | Superior for high-power operations | Adequate for lower-power tasks |
Cost | Higher initial investment | More affordable upfront |
Best For | High-precision, industrial welding | Small-scale, lower-power applications |
Conclusion
Laser welders powered by water-cooling systems deliver exceptional precision. Advanced control software manages laser output with custom curves, producing smooth, strong welds. Intuitive interfaces simplify navigation, allowing quick adjustments and setup. U.S.-made control chips guarantee reliable performance during continuous use. Water cooling maintains optimal temperatures, preventing thermal distortion and ensuring consistent laser power. Features like flexible laser positioning and one-click welding enhance efficiency and accuracy. These components work together to boost your welding projects’ reliability, safety, and efficiency.
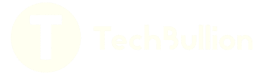