What is an Industrial Generator and How Does It Work?
Understanding the Basics of Industrial Generators
Industrial generators are critical machines designed to supply electricity during power outages or in locations where grid power is unavailable or unreliable. They are essential for industries that require continuous power to sustain operations, including healthcare, manufacturing, construction, and data centers. These generators function by converting mechanical energy into electrical energy using electromagnetic induction. When paired with an appropriate power distribution system, industrial generators ensure uninterrupted energy supply to essential equipment and systems.
If you are looking for more information about Industrial Generator – LIANJIE, go here right away.
Key Components of an Industrial Generator
An industrial generator incorporates a number of parts that helps optimize its performance:
View Industrial Generator for sale – LIANJIE for More Details
Engine – Usually fueled with Diesel, Natural gas, or propane, an engine works as the primary mover for the generator.
Alternator – With the aid of electromagnetic induction, alternators change the mechanical energy which comes from the engine to electrical energy.
Fuel System – An adequate fuel system ensures that the engine receives and stores fuel consistently within its set parameters.
Control Panel – It helps to the interface with the operator for control, monitoring, and management of the operations of the generator.
Cooling System – Helps mitigate overheating through the cooling of alternators and engines which allows for the dissipation of heat generated during a prolonged use.
Exhaust System – It helps in curbing violations of standards which relate to the environmental protection by removing emissions produced during the fuel combustion process.
Lubrication System – These systems aid in providing the engine parts with improved efficiency while reducing friction and strain damage.
Efficient and positive results from a generator depend on the proper co – ordination of these parts and positive management.
The Advantages of Diesel Generators over Other Types of Generators
Because of the robustness, reliability, and efficiency of diesel generators, they are extensively used in the industry. Diesel generators have an upper hand over gasoline generators since they have a lower cost of operation and greater fuel efficiency because of the energy density of diesel fuel. Diesel engines also require low maintenance and suffer from reduced wear, compared to gasoline engines. This is due to a diesel engine’s simplified ignition system, which does not rely on spark plugs.
For remote or high-demand applications, diesel generators are preferred over propane or natural gas generators, as they are easier to store and transport in large quantities. However, for places with existing gas pipelines, natural gas generators may be preferred due to lower emissions and reduced environmental impact. The power requirements and operational limitations of the project determine which type of generator is most suitable for the given application.
Why Choose a Diesel Generator for Your Power Supply?
The Benefits of Using Diesel Generators
Determined and powerful, a diesel generator is a type of power device with many advantages. One advantage is that diesel engines are easy to maintain when used with other systems; usage does not require much effort to keep them sustained or maintained. These devices are also useful in providing backup power, especially for critical hospitals or data centers where power cuts are not to be tolerated. Compared to other types of fuel systems, these generators utilize additional power when transferring diesel fuel, which makes them superior. The backup systems are very easy to repair and are not very hard to maintain, making them cost-effective.
Generators powered by diesel have long been recognized for their remarkable fuel efficiency. While diesel generators’ fuel consumption is lower in comparison to gasoline generators, they yield the same amount of power, ultimately resulting in long-term savings. The more effective combustion of fuel in diesel engines, because of its higher compression ratio, accounts for this efficiency. Increased diesel system fuel economy due to turbocharging and modern electronic fuel injection systems further boosts diesel generators’ utility as an economical option during operations that sustain high or continuous power demand over extensive periods.
Typical Uses of Diesel Industrial Generators
The reliability and power output capabilities of diesel industrial generators make them indispensable in different sectors. They are frequently used as the main source of power in construction sites, mining operations, oil fields, and other remote locations that are not accessible to the power grid. These generators also serve as critical backup systems in facilities like hospitals, manufacturing plants, and data centers, ensuring operations that are highly sensitive to interruptions during power outages run seamlessly. In agriculture, diesel generators play a vital role in powering irrigation systems and other farming machinery. Their robust performance makes these generators useful in providing both temporary and permanent power solutions.
How to Select the Right Size for Your Industrial Generator
Calculating Your Power Requirements
Choosing the correct industrial generator for your business hinges upon determining your power requirements first. First off, determine the cumulative electrical load for your business which requires operational power during functional hours. This entails adding the wattage of all equipment, machinery, and systems which need to be continuously operational. Consider running and starting wattages separately for systems such as motors and compressors which require higher power levels during operation compared to when they are running on standby.
Generator and Facility Requirements
There are several prerequisites that will influence the size of generator required for your facility. These cover the kind of equipment and their number, load type (inductive or resistive) and power demand (steady or fluctuating). Predefined physical conditions such as altitude and temperature may additionally influence generator efficacy and output. These preconditions may need capacity specifications to be altered.
Correct Output Assessment
Proper differentiation of peak power demand from average operating power can be critical while assessing your generator’s power output needs. Make sure the generator specifications are rated to provide sufficient capacity and handle load during surge periods, often seen during start-up or infrequent usage patterns. Meeting these requirements when choosing a generator avoids underperformance, providing power delivery reliability and consistency across all applications.
Frequently Asked Questions About Industrial Generators
What Types of Generators Are Available?
Industrial generators are of different types based on their applications and operational requirements. A popular example is diesel generators, known for their effectiveness in heavy-duty applications. Another example is natural gas generators, which are cleaner and more cost-effective but less efficient since they have lower efficiency. Besides those, portable power generators are used as temporary and backup power sources. Standby generators restore power automatically through backup systems in case of an outage. There are also hybrid generators, which combine conventional fuels with renewable energy, including solar, making them efficient and eco-friendly. Regardless, the initial selection always considers power requirements, fuel sources availability, and condition of the place of use.
Maintaining Your Industrial Generator
Routine maintenance includes inspecting and replacing air filters, checking oil levels, coolant levels, cross-contamination within the fuel system, and ensuring all components adhere to standard requirements. Not only does this decrease overall downtime and increase efficiency during peak hours, but it also ensures industrial generator maintenance prolongs its lifespan. Comprehensive testing is suggested during peak power demand to ensure uninterrupted power flow. Additionally, servicing by certified professionals who specialize in core machine components such as alternators, batteries, and control panels while following the manufacturer’s servicing schedule also aids compact reliability in the long run. Ensuring precise logs are kept along with the servicing records boosts overall performance optimization.
What Are the Emission Standards for Diesel Generators?
Diesel generators are no different from other machines when it comes to having to comply with emission standards. All their emissions are regulated by the Environmental Protection Agency (EPA) of the USA. The diesel generator set is also equipped with various emission control devices to capture and restrict the release of NOx and CO and lower exhaust SO2 levels. In the case of diesel generators, it consists of particulate matter, nitrogen oxides, carbon monoxide, and hydrocarbons. Based on the power output and the year of manufacture, generators are placed in different tiers. Newer generators are mostly compliant with the stringent Tier 4 regulations. Not every model of diesel generator set is compliant with EPA objectives; only with advanced exhaust SCR systems and diesel particulate filters are they fully compliant. Emission regulations are there to help builders avoid legal constraints and operate emissions freely while preserving the environment.
Comparing Portable and Stationary Generators
When to Use Portable Generators
In the case of portable generators, these power sources are a great choice for short term, outdoor, or mobile power needs due to their compact design. These generators are often used for outdoor activities, construction jobs, and even emergency backup. In scenarios where the primary source of energy is inaccessible, these generators can be lifesavers. Also, due to their small size and the ease with which they can be transported, portable generators offer operational flexibility.
Benefits of Stationary Generators in Industrial Settings
In contrast to portable generators, stationary generators are specifically designed to serve industrial and commercial sectors as a reliable, high capacity power supply. These generators are installed as permanent fixtures and unlike portable ones, they can automatically turn on during grid outages which helps in maintaining consistent power supply without requiring manual switching. Since stationary generators are designed to seamlessly integrate with existing electrical infrastructure, they are more efficient. In addition, they can include advanced telemetry monitoring systems that allow for enhanced oversight and maintenance, which makes them even more helpful.
Cost Considerations for Portable Versus Stationary Generators
Analyzing costs for portable and stationary generators involves evaluating upfront costs, operational expenses, and intended usage. Lower investment costs are associated with portable generators, however, these might have higher operating costs due to reduced fuel efficiency and a lower operating threshold. On the other hand, upfront investment costs for stationary generators are higher due to the installation and setup expenses; however, they may be more reliable long-term and more fuel-efficient during over varying use periods, resulting in lower overall operational costs. Evaluating the power output requirements, duration of use, maintenance costs, and other relevant factors are key in determining the most cost-effective solution for a wide range of applications.
How to Ensure Reliable Backup Power with a Transfer Switch
What is a Transfer Switch and How Does it Work?
The transfer switch assists in the shifting of electricity supply from the primary grid to a standby generator in the event of grid failure. It guarantees that electricity is delivered sufficiently to certain circuits without backfeeding power to the grid to ensure the safety of utility workers and to avoid any damage to the equipment. As per design, transfer switches can be divided into two categories: Manually operated Transfer switches (MTS) and Automatic Transfer switches (ATS). An MTS requires physical interactions to enable switching, whereas an ATS monitors the power supply and responds to cuts automatically.
Choosing The Best Transfer Switches For Your Requirements
The brands and models of transfer switch you wish to install depend on multiple crucial considerations such as the generator type, power needs for auxiliary devices, balance between efficiency and automation, among others The generator size determines how many circuits are powered. Smaller generators can power a few circuits and may use a manual transfer switch. For larger applications, facilities that wish to maintain availability require automatic transfer switches. Make sure the voltage and ampere ratings of your generator match those of load shedding features that provide prioritization of power to essential circuits when the generator is in operation.
Installation Guidelines for Your Transfer Switch
The correct installation of a transfer switch impacts how safely and effectively backup power will function. It is best to work with a licensed electrician who observes local electrical codes and safety regulations. The transfer switch must be located adjacent to the main circuit panel to decrease wiring difficulties. Furthermore, regular system assessments are vital to confirm functional capability and preparedness for automatic responses during outages. The electrician must explain manual operational workflows, if necessary, for simplified user interaction in conjunction with thorough circuit labeling.
Understanding the Role of Industrial Generators in Emergency Situations
How Generators Provide Backup Power During Outages
Generators are paramount in ensuring uninterrupted electrical power systems function within a facility during outages. They convert mechanical energy into electrical energy through an internal combustion engine running on diesel, natural gas, or propane. Generators initiate fuel supply as soon as there is fuel outage, automatically powering the necessary circuits through the automated transfer switch AVR. Depending on the facility’s specifications, different essential systems such as lighting, HVAC, or critical machines can be seamlessly integrated. The reliability and responsiveness provided by industrial generators during emergencies make them invaluable.
Critical Features for Emergency Generators
Like other types of generators, emergency generators have defined characteristics to enhance their dependability and effectiveness at crucial times. Emergency generators receive information from various sensors and monitor their temperature and voltage, which helps the generator to ensure fuel-efficient operations. The generator along with other equipment is protected from electrical harm using an overload protection mechanism. In addition, equipment specially designed to reduce noise can be integrated to improve generator performance in noise-sensitive areas. Most emergency generators tow integrated high-capacity fuel tanks to enable continuous operation while positioned at remote locations enabling easy monitoring and servicing, even when stationed far away from the operator.
Optimizing Facility Functionality During Power Outages
When it comes to power outages, proper preparation greatly improves the efficiency of backup generators. Completing a thorough power audit assists the facility in determining the critical systems that need to be backed up. Creating an emergency power policy and routinely scheduled testing and maintenance boosts the mechanical readiness of generators and mitigates the risks of failure. Following fuel maintenance schedules and ensuring the necessary reserves are set aids in sustaining operation over extended periods. Along with active issuing refueling policies, training personnel on issuing operational commands and interfacing the systems into the master electrical grid of the facility allows for backup power automatic engagement during seamless shifts. Following all the listed above significantly boosts resilience during systemic emergency power outages.
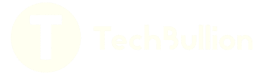