Manufacturing is an intricate dance of machinery, workforce, and methods. At the core of this dance is the automation system, and more often than not, the maestro is a Programmable Logic Controller (PLC). These digital computers have been the backbone of automation for decades. However, with the advancements in PLC programming, their role is evolving. No longer just the silent operators, PLCs are now reshaping on-site troubleshooting and maintenance protocols in the manufacturing world, bringing about a revolution in efficiency and precision.
Traditional Troubleshooting: Reactive and Time-consuming
Historically, troubleshooting in manufacturing setups was a reactive process. Machinery would run until a fault occurred, necessitating stoppage, manual diagnosis, and subsequent repairs. This method was time-consuming and costly, with unexpected downtimes affecting production schedules and bottom lines.
Maintenance was often scheduled, with machinery being checked at regular intervals. But this approach had its pitfalls. Equipment that was in perfect working order would undergo unnecessary checks, while others might fail just after a routine inspection.
Enter Advanced PLC Programming
With the evolution of PLC programming, this paradigm is shifting. PLCs, equipped with advanced programming, can now:
- Predictive Troubleshooting: Instead of waiting for a fault to occur, PLCs can now predict potential issues before they become critical. By constantly monitoring machine operations and parameters, PLCs can detect anomalies and bring them to operators’ attention. This proactive approach allows for minor interventions that prevent major breakdowns.
- Real-time Diagnostics: Advanced PLCs provide real-time feedback on machinery operations. In the event of a fault, they can pinpoint the exact cause, whether it’s a mechanical failure, a software glitch, or an external interference. This precision eliminates the guesswork from troubleshooting, drastically reducing downtime.
- Remote Monitoring: Modern PLCs can be accessed remotely with integrated communication protocols. This means that experts from anywhere in the world can log in, diagnose, and even rectify certain issues without being physically present on-site. It’s a game-changer, especially for remote facilities or those operating round the clock.
- Data-driven Maintenance: Instead of routine checks, maintenance can now be data-driven. PLCs, with their continuous monitoring, can provide insights into wear and tear, component life cycles, and operational efficiencies. This data can be analyzed to schedule maintenance only when required, optimizing resource utilization and minimizing disruptions.
The Bigger Picture: Cost Savings and Efficiency
The implications of these advancements go beyond just machinery uptime. For manufacturers, the costs associated with unexpected downtimes can be significant. There’s the direct impact of halted production, but there are also ripple effects: delayed deliveries, compromised quality, and increased labor costs. By minimizing these unplanned stoppages, PLCs provide tangible cost savings.
Moreover, the efficiency gains are paramount. With predictive troubleshooting and data-driven maintenance, machinery operates at peak efficiency for longer durations. This not only increases production capacities but also ensures consistent product quality.
The manufacturing world is in flux, with technologies like IoT, AI, and advanced robotics making inroads. But at the heart of this transformation, PLCs continue to hold their ground. With enhanced programming capabilities, they’re not just adapting to the changing landscape; they’re shaping it.
By revolutionizing troubleshooting and maintenance protocols, PLCs and their programmers are ensuring that the manufacturing dance continues unhindered, with every move precise, every step optimized, and every beat resonating with efficiency. For manufacturers, embracing these advancements is not just a choice; it’s a necessity in the quest for excellence in the modern age.
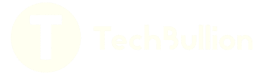