Overview
A piston compressor is a type of mechanical device used for compressing gases. It is a common type of compressor used in various industries, including automotive, HVAC, and manufacturing. In this answer.
Piston Compressors in Detail
We will explain the piston compressor in detail in 10 steps.
1: Introduction to Piston Compressor
A piston compressor, or a reciprocating compressor, uses a piston and cylinder to compress the gas. The piston moves up and down inside the cylinder, creating pressure and compressing the gas.
2: Types of Piston Compressor
There are two types of piston compressors in Oman: single-stage and two-stage. A single-stage piston compressor compresses the gas in one stroke of the piston, while a two-stage piston compressor compresses the gas in two stages.
3: Single-Stage Piston Compressor
In a single-stage piston compressor, the gas is sucked in through the inlet valve and compressed in one piston stroke. The compressed gas is then discharged through the outlet valve.
4: Two-Stage Piston Compressor
In a two-stage piston compressor, the gas is first compressed in the low-pressure stage and then passed on to the high-pressure stage for further compression. The compressed gas is then discharged through the outlet valve.
5: Components of Piston Compressor
The main components of a piston compressor include the cylinder, piston, inlet valve, outlet valve, connecting rod, crankshaft, and motor.
6: Cylinder
The cylinder is part of the compressor that houses the piston. It is typically made of cast iron or aluminum and has a smooth inner surface to reduce friction.
7: Piston
The piston is a cylindrical part that moves up and down inside the cylinder. It is typically made of cast iron or aluminum and has rings on the outer surface to seal the gas and prevent leakage.
8: Inlet Valve
The inlet valve is located on the side of the cylinder and allows gas to enter the cylinder during the intake stroke of the piston.
9: Outlet Valve
The outlet valve is located on the top of the cylinder and allows compressed gas to exit the cylinder during the compression stroke of the piston.
10: Working of Piston Compressor
During the intake stroke, the piston moves downward, creating a vacuum in the cylinder. This allows gas to enter the cylinder through the inlet valve. During the compression stroke, the piston moves upward, compressing the gas inside the cylinder. The compressed gas is then discharged through the outlet valve.
Advantages of Piston Compressor
Here are the benefits of piston compressors:
- Versatility: Piston compressors are highly versatile and can be used for various applications, including powering pneumatic tools, operating machinery, and supplying air for spray painting.
- High-Pressure Output: Piston compressors can produce high-pressure output, making them ideal for applications that require high-pressure air.
- Low Cost: Piston compressors are relatively inexpensive compared to other types of compressors, making them an affordable option for small businesses or individuals.
- Low Maintenance: Piston compressors are generally easy to maintain and require little maintenance. They are also highly durable, making them a long-lasting investment.
- Energy Efficient: Piston compressors are designed to be energy efficient, reducing energy consumption and operating costs.
Disadvantages of Piston Compressor
Here are the disadvantages of piston compressors:
- Noisy Operation: Piston compressors can be pretty loud, primarily when operating at high speeds. This can be a concern for workplaces that require low noise levels.
- Limited Capacity: Piston compressors have limited capacity, making them unsuitable for large-scale industrial applications.
- Pulsating Flow: Piston compressors produce a pulsating flow of compressed air, which can cause issues with downstream equipment or tools.
- Maintenance Requirements: While piston compressors are generally low maintenance, they require periodic maintenance, including oil changes and filter replacements. Failure to properly maintain a piston compressor can result in reduced efficiency and costly repairs.
- Heat Buildup: Piston compressors generate a significant amount of heat during operation, which can lead to issues with overheating if not adequately managed.
Overall, Piston compressors offer several advantages, including versatility, high-pressure output, low cost, low maintenance, and energy efficiency. However, they also have several disadvantages, such as noisy operation, limited capacity, pulsating flow, maintenance requirements, and heat buildup. It is essential to carefully consider these factors when selecting a compressor for a particular application.
Conclusion
A piston compressor is a type of mechanical device used for compressing gases. It uses a piston and cylinder to compress gas and is available in single-stage and two-stage. The main components of a piston compressor include the cylinder, piston, inlet valve, outlet valve, connecting rod, crankshaft, and motor.
The working of a piston compressor involves the intake stroke and compression stroke, where the piston moves up and down to suck in gas and compress it.
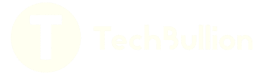