Perfluoroalkoxy Fluoropolymer (What Is Pfa Plastic) stands out due to its unique chemical composition and is known for its unparalleled combination of chemical resistance, thermal stability, and mechanical strength. Determining the usefulness of PFA plastic, it is evident that PFA plays a critically important role in manufacturing aids in electronics, pharmaceuticals, chemical processing, and more. PFA is distinctly different from other fluoropolymers in many aspects. This blog delivers an eloquent analysis of the many facts about PFA plastic and its manufacturing steps, which are specially designed for specialists and professionals in the field. The description provided in this guide is crucial for multifaceted engineers, designers, and developers as PFA takes the forefront of modern technology. If you are looking for key details and performance analysis of PFA, this guide provides the cutting-edge understanding professionals need.
What is PFA Plastic, and How Does it Differ from Other PFAS?
Perfluoroalkoxy alkane (PFA), a specific type of fluoropolymer, is recognized for its superb chemical resistance, critical non-stick features, high thermal stability, and remarkable resilience. It is a fully fluorinated thermoplastic polymer classified under per- and poly-fluoroalkyl substances (PFAS). PFA is also a fluoropolymer, like polytetrafluoroethylene (PTFE) and fluorinated ethylene propylene (FEP). Still, its prominence comes from its superior workability, which renders PFA easier to mold and extrude than other fluoropolymers. In addition, while PTFE is non-melt-processable, PFA can be subjected to high temperatures during processing, producing complex shapes while retaining excellent physical and chemical properties. These features make PFA particularly useful in extreme conditions encountered during semiconductor fabrication, chemical processing systems, or high-performance wire coatings.
Comparing PFA to other fluoropolymers like PTFE and FEP
Like most fluoropolymers, PFA has comparisons with PTFE and FEP, and each has its key distinctive characteristics suited for different purposes. Its relationship with PTFE is similar in that PFA shares excellent chemical resistance, high performance in elevated temperatures, and relatively weak bonding as characteristics, too. Its dissociation with PTFE comes in terms of shape. PFA, unlike PTFE, is melt-processable, making it easy to fabricate far more complex shapes without losing the ability to withstand extreme temperatures (260°C). FEP, which is also melt-processable, tends to have a lower continuous service temperature (between 205 and 230°C) and less mechanical strength than PFA, resulting in easier processing.
Though PTFE loses in non-stick applications, it performs well with everything else. PFA allows for a precision between PTFE and FEP’s flexibility by being incredibly easy to process and strong under harsh conditions. This will enable PFA in semiconductor manufacturing and harsh chemical environments.
What Are the Main Applications and Uses of PFA Plastic?
PFA plastic is widely used by industries that value high chemical resistance, thermal stability, and purity. Its main applications are in the semiconductor industries, where it is utilized in wafer processing equipment and chemical delivery systems because of its inert, non-contaminating properties. In chemical processing, PFA is also widely applied for linings, tubing, and fittings that come in contact with corrosive acids and solvents. Moreover, its excellent non-stick, low-friction properties make PFA suitable for specialty coatings in food processing and pharmaceutical equipment.
PFA in High-Purity Tubing and Lining Applications
PFA, short for Perfluoroalkoxy alkane, is the choice for critical tubing and lining applications because of its strong chemical resistance and chemical purity retention under severe conditions. It is non-leaching, meaning it can not contaminate the samples when used in ultrapure systems. Moreover, the non-stick and smooth surface of PFA minimizes the chances of contamination, which is very important in the semiconductor, biotechnology, and pharmaceutical industries. PFA tubing is also reliable in extreme thermal conditions due to its strong resistance to high and low temperatures. Furthermore, its resiliency and chemical inertness make it a top choice for processes with strict cleanliness and chemical stability requirements.
Uses in pharmaceutical and semi-conductor industries
Pharmaceutical Industry
PFA tubing is widely used in the pharmaceutical industry primarily due to its remarkable chemical resistance and non-reactive and biocompatible characteristics. It is also used for fluid transfer applications that necessitate ultrapure conditions, such as transferring high-purity solvents, reagents, and even active pharmaceutical ingredients (APIs). PFA is also non-leaching, ensuring chemical integrity with no contamination. The tubing is also reliable in high-temperature sterilization processes (steam cleaning/ autoclaving) fundamental to sterile production environments, as it functions at -200 degrees Celsius to 260 degrees Celsius.
Semiconductor Industry
In the semiconductor industry, the PFA tubing is self-evident, with aggressive chemicals used in wafer fabrication etching and cleaning phases. The inertness of the product also plays a vital role with ultra-pure chemicals like hydrofluoric acid or sulfuric acid that need to be used. PFA tubing will also endure high temperatures and pressures in a chemically aggressive environment of up to 200 psi, depending on its size and thickness, along with the additional temperature and pressure factors. The clarity of the tubing also enables the monitoring of fluid flow for improved precision and process control.
This is why PFA tubing is highly regarded in industries that focus on having pure, durable, high-quality, and extreme-condition warehouses.
How Does PFA Plastic Perform in Extreme Chemical Environments?
Due to the unmatched chemical inertness and corrosion resistance that PFA plastic provides, it can withstand even the harshest chemical environments. PFA can be exposed to strong acids, organic solvents, and bases and remain structurally intact. Its non-porous characteristic means that the polymer doesn’t absorb or diffuse chemicals, ensuring absolute containment. Moreover, PFA is stable at temperatures above 500°F (260°C). At this temperature, it continues to retain its mechanical and chemical characteristics. For such reasons, PFA Polymer is one of the most desirable materials when dealing with situations that require chemical stability while simultaneously preventing contamination.
PFA’s outstanding chemical resistance properties
PFA’s outstanding chemical resistance can be attributed to its unique molecular structure, which features strong carbon-fluorine bonds, ensuring high chemical inertness. The material effectively resists corrosion and degradation when exposed tothe most aggressive chemicals, including:
- Strong acids: Resistance to hydrochloric acid, sulfuric acid, and nitric acid across all concentrations.
- Strong alkalis: Compatibility with sodium hydroxide and potassium hydroxide without any observable etching or swelling.
- Organic solvents: Stable when exposed to polar and non-polar solvents, such as acetone, chloroform, and toluene.
These properties position PFA as a leading choice for use in industries requiring stringent chemical handling, such as semiconductor manufacturing, chemical processing, and medical device production.
What Are the Manufacturing Processes for PFA Plastic Products?
PFA plastic products are typically made from injection molding, extrusion, and blow molding. Precisely detailed complex components are manufactured using injection molding, the most popular method that forces molten PFA into a mold cavity. Specific shapes, such as films, tubes, and rods, are continuously created using extrusion, pushing molten PFA through a die. Hollow items, such as bottles, are made using blow molding when molten PFA is inflated into a mold. These processes benefit from PFA’s remarkable flow and thermal properties that guarantee high performance and consistency in the final products.
Injection Molding Techniques for PFA Parts
One of the most important things to consider when discussing injection molding techniques of PFA plastic parts is the characteristics of the material. Since PFA has a high melting point, it must be processed over 600F (315C). The injection mold must have even heat and venting to achieve high flow and high fill. In addition, screw and barrel assemblies made out of Hastelloy or nickel alloy are suggested. These materials avoid PFA destruction during machining because they are resistant to corrosion. The injection rate is another parameter that needs to be controlled precisely. Too fast of a fill can cause stress, and too slow of a fill can cause issues with the quality of the part. The combination of exact temperature control and appropriate tool design allows the production of strong and high-quality parts with very few imperfections.
Extrusion methods for PFA tubing and profiles
Given a particular material’s defined thermal and rheological specs, tight parameters must be set when processing PFA tubing and profiles. The barrel screw designs have a compression zone that is very gradual to lower the likelihood of shear stress and material degradation. The barrel typically needs to maintain a temperature between 590°F and 680°F (310°C to 360°C), along with closely maintaining the die temperature to ensure the melt flow is even.
During the extrusion process, pressure must remain steady between 2500 and 4500 psi to ensure the material moves through the die correctly. Moreover, after the extrusion process, an air or water cooling system is essential to cool the tubing or profiles to ensure they are dimensional and stable. Furthermore, corrosion-resistant tools and components such as Hastelloy or other Nickel alloys can withstand PFA’s chemicals, making them ideal.
Following these calibrated parameters of the extrusion line and calibration of the die will guarantee the quick and consistent creation of PFA tubing and profiles with excellent thermal resistance, flexibility, and mechanical strength for use in industrial applications.
Frequently Asked Questions (FAQ)
Q: What are the main applications of PFA plastic?
A: PFA is commonly used in the pharmaceutical and semi-conductor industries due to its high purity and chemical inertness. It’s also used for flexible and reusable medical equipment, chemical processing equipment, wire and cable insulation, and parts where high-temperature resistance and flexibility are required.
Q: How do PFAs impact the environment?
A: Many PFAs (Per- and polyfluoroalkyl substances), including those used in producing PFA plastic, have raised environmental concerns due to their persistence in the environment. These substances can accumulate in water, soil, and living organisms over time. However, PFA plastic itself, when properly used and disposed of, does not readily break down into these environmental contaminants.
Q: What makes PFA suitable for semiconductor applications?
A: PFA’s high purity, excellent chemical resistance, and ability to withstand high temperatures make it ideal for semiconductor manufacturing. Its low particle generation and resistance to aggressive chemicals used in etching and cleaning processes are crucial in maintaining the cleanliness required in semiconductor fabrication.
Q: How does PFA’s chemical inertness benefit various industries?
A: PFA’s chemical inertness means it doesn’t react with most solvents, acids, or bases. This property makes it excellent for containing or transporting aggressive chemicals in industries like chemical processing, pharmaceuticals, and electronics manufacturing. It also ensures that PFA parts don’t contaminate the materials they come into contact with, which is crucial for maintaining high purity in sensitive processes.
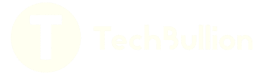