Introduction
We live in a modern world where manufacturing factories, power plants, mineral processing activities, and many other industrial processes are all around us and necessary to keep civilization functioning. Even though the results of these processes are readily apparent, one important element—the simple filter bag—tends to go overlooked.
These simple yet efficient devices are essential to the operation of many industrial processes because they filter dust and other particulate matter from air streams. Many industrial and processing operations could not function safely or in accordance with environmental requirements without filter bags.
Dust and polyester filter bag is the state-of-the-art in filter bag technology. These high-performance filters combine robustness, effectiveness, and adaptability to satisfy the exacting requirements of global industries. Let’s examine more closely what makes these filters so remarkable.
Polyester, the Material of Miracles
To understand polyester filter bags, we must first look at polyester fiber. Ethylene glycol and terephthalic acid react to form polymers, producing polyester, a synthetic textile.
Despite its seemingly common appearance, polyester fiber has a special set of qualities that make it very useful for filtering applications:
Power
Because of the superior tensile strength of polyester fibers, filter bags can resist the demanding conditions of industrial usage without breaking or deforming. These filter bags can withstand large air volumes and differential pressures due to the sturdy nature of polyester.
Resistance to Heat
Polyester can readily survive the high temperatures involved in operations like waste incineration, metallurgy, and cement manufacture since it has a melting point of around 500°F (260°C). Because of their heat resilience, filter bags don’t deteriorate too soon.
Resistance to Chemicals
Polyester has strong chemical resistance to a variety of substances, such as solvents, acids, and alkalis, often encountered in industrial environments. This chemical inertness protects the filter bags from deterioration.
Resistance to Hydrolysis
Polyester has many advantages over materials like cellulose, including its superior resistance to hydrolysis, which is the process by which water breaks down chemical molecules. Because of their resistance to hydrolysis, polyester filter bags don’t deteriorate in humid environments.
Stability in Dimensions
In warmer weather, polyester fibers don’t shrink, stretch, or distort too much. Because of their dimensional stability, polyester filter bags are able to continuously retain both their form and filtering efficiency.
Essentially, polyester combines the chemical resistance to prevent deterioration from exposure to corrosive gases, liquids, and particles with the durability required to survive demanding industrial settings. Specifically designed for filtering, it is a robust and adaptable substance.
How Polyester Filter Bags Are Made
In order to provide dependable, effective performance, the physical design and manufacturing techniques used for polyester filter bags are just as crucial as the polyester fiber itself. Here are a few critical elements of the production of polyester filter bags:
Textile Weaves
The filter bag’s woven or felt fabric greatly influences its filtering properties. Plain, twill, sateen, and felt/membrane laminates are common weaves. Each weave imparts different pore sizes, air permeabilities, and surface qualities to meet specific filtering requirements.
Tight twill weaves, for instance, provide very effective filtration that’s perfect for small dust particles. Higher permeability means reduced air resistance in plain weaves. In addition, felt laminates combine periodic pulse-jet cleaning with effective surface filtering.
Completing Therapy
Polyester filter bag textiles may undergo a variety of finishing processes to improve their functionality for certain uses.
- oleophobic fluorinated coatings to repel oils and liquid aerosols;
- hydrophobic coatings to maintain airflow in humid conditions;
- antistatic treatments to prevent static charge buildup;
- Singe-resistant coatings for high temperatures up to 550°F;
- PTFE membrane laminates for ultra-fine sub-micron particle filtration
Shapes and sizes of bags
We make polyester filter bags to order in a variety of sizes and forms to suit various housing designs.
- oval bags, round or circular bags, top load bags, polyester filter socks, pleat-shaped bags, pleat lock bags, and more bespoke combinations Bags may have hundreds of square feet of surface area and lengths ranging from inches to over ten feet. Venturis, cuffs, clips, and cable restraints are examples of construction attachments that stabilize bags and improve airflow.
Needlefelt Technology
High-performance polyester filter bags commonly use needlefelt as a core fabric structure. Polyester strands are mechanically looped and compacted into a thick, non-woven mat to form needlefelt.
The outcome is a sheet that is porous and very resilient, making it perfect for pulse-jet cleaning. Due to its distinctive design, needlefelt operates with less air resistance and a high dust-holding capacity while using less energy. Specifically designed for high-volume industrial filtration, it’s a specialty cloth.
All things considered, polyester filter bags combine the benefits of polyester fiber with creative fabric design, finishing techniques, and bag geometry. They can satisfy the whole range of industrial air filtering requirements because of their adaptability.
Bags for dust filtering in dry particulate matter
Polyester filter bags are excellent in a variety of industrial processes for collecting dry particle matter. Due to their resilience to heat, moisture, and chemicals, as well as their excellent particle-holding capacity, they are perfect for demanding dust collection applications such as the following:
- Pharmaceutical and plastics manufacturing;
- Sand and gravel processing;
- Metalworking and Smelting Operations;
- Furnace and Kiln Exhaust Filtration;
- Agricultural and Food Processing;
- Woodworking and Sawmills; and many more
In these situations, polyester dust filter bags protect personnel and equipment from exposure to dangerous chemicals such as silica, carbon dust, metal vapors, and other fine particulate matter. They meet ever-tougher pollution regulations while enabling processes to run safely.
Dust filter bags with high temperatures
Polyester has a unique benefit in that it may be used as a high-temperature dust filter bag material. Polyester filter bags can withstand hot exhaust streams from sources such as the following thanks to their 500°F melting point:
The industries that include aluminum smelting and remelting, glass and fiberglass manufacturing, ceramic, brick, and refractory processing, ferrous and non-ferrous foundries, waste incineration, cement kilns, and fly ash filtration in power plants
Standard textiles like cotton or polyolefin would soon degrade and lose their integrity in these high-heat settings. However, polyester dust filter bags are capable of withstanding the intense heat without sacrificing filtering efficiency.
Finishing techniques like single-resistant coatings may also be used to manage difficult dust streams that include condensables. Additionally, for continual removal of caked dust, specialist needlefelt polyester fabric laminates are perfect for pulse-jet cleaning cycles.
Overall, polyester is a great high-temperature dust filter bag for demanding applications due to its capacity to withstand high heat as well as its resistance to corrosives and abrasion.
Polyester Filter Bags for Liquid Filtration
Polyester filter bags are mostly used for the capture of dry particles, but they may also be used for liquid mists, aerosols, and light liquid flows. These filters work well even in greasy or damp environments because of the inherent oleophobicity of polyester fiber and repellent fabric treatments.
Typical uses for liquids are as follows:
- Gathering oil mist;
- Recovering hydrocarbons and solvents
• Production of food and beverages; - Petrochemical processing;
- Industrial scrubber systems;
- Water and condensate removal;
- Pharmaceutical manufacturing
In these situations, the hydrolysis resistance of a polyester filter bag keeps it from degrading from exposure to moisture. The bags’ unique oleophobic treatments enable them to continuously reject oils and other similar pollutants while preserving airflow.
Membrane laminates provide a strong barrier surface for difficult condensable particle and liquid aerosol applications. To put it simply, the polyester fabric blocks liquids from passing through or blinds the filter material by functioning as a shell with an integrated internal membrane.
Polyester filter bags can withstand mists, aerosols, and sporadic light liquid flows without sacrificing performance, even though they are not intended for large-scale liquid filtering. They are workhorses in all sectors that need the removal of light liquid and dry particles in a single bag because of their oleophobicity and fluid resistance.
Efficiency, durability, and safety
In comparison to conventional filter media like cotton or polypropylene, polyester and polyester/membrane filter bags provide significant real-world benefits in terms of safety, lifespan, and operational efficiency. These advantages extend beyond their remarkable technological capabilities.
Regulatory and Environmental Aspects
In addition to being essential for operational effectiveness, the use of polyester and dust filter bag is also necessary for adhering to environmental requirements and advancing sustainability. Several nations and areas have imposed strict emission restrictions and air quality regulations, with harsh consequences for noncompliance.
These filter bags are critical for helping industrial operations meet regulatory standards while also reducing their environmental impact because they capture and trap particulate matter efficiently. Furthermore, the deployment of these filtration systems shows a proactive attitude toward environmental stewardship and a dedication to corporate social responsibility.
Progress and Upcoming Events
Growing environmental consciousness and technical developments are driving ongoing change in the air filtration industry. These advancements will help dust and polyester filter bags, improving their effectiveness and performance even more.
Better Materials: Constant research and development is being done to create new materials and fabric blends that are more durable and economical but also have better filtering qualities.
Applications of Nanotechnology: There is great potential for using nanotechnology in the design of filter bags. Coatings made of nanofibers or nanoparticles may improve filtration effectiveness, collect a greater variety of particulates, and even have self-cleaning or regenerative properties.
Intelligent Monitoring Systems: By using sensors and data analytics, intelligent monitoring systems may provide up-to-date information on the functionality and state of filter bags. This knowledge may aid in predictive maintenance, optimize replacement schedules, and reduce downtime.
Sustainable Manufacturing: As environmental concerns continue to influence business practices, filter bag production is becoming more and more focused on sustainable methods. This covers the use of biodegradable or recycled materials in addition to energy-saving manufacturing techniques.
Conclusion
Although dust and polyester filter bags may seem like little parts of larger industrial processes, they have a significant influence on environmental preservation and air quality. These unsung heroes protect the wellbeing of employees, communities, and ecosystems by going about their business quietly and effectively.
Effective air filtering technologies will only become more crucial as companies develop further and environmental rules tighten. With their remarkable resilience, filtering effectiveness, and adaptability, polyester and dust filter bags are well-suited to tackle these difficulties.
Businesses may show their dedication to ethical business practices and help create a cleaner, healthier future for everybody by adopting this filtering technology and keeping up with industry developments.
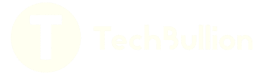