Driven by powder metallurgy industry, MIM technology has become more mature and stable. MIM technology includes the following aspects: feed preparation, injection molding, injection molding process simulation, degreasing, sintering, MIM application, MIM product design and specification.
Metal injection molding can be traced back to 1920s, started by ceramic spark plug powder injection molding. In subsequent decades, powder injection molding was mainly used in ceramic injection molding. Until 1979, Parmatech’s metal injection molding products, formed by Wiech and his team, got two awards. At that time, Wiech and Rivers patented, powder injection molding began to shift to metal injection molding-oriented.
The development of metal powder injection molding in China is relatively late start, so the technical aspects of MIM technology compared with foreign countries has not enough skill. In order to promote the research and development of MIM in China under the background of rapid development of MIM technology in the world, the monographs on the related theories of MIM technology, especially the application of MIM, are becoming more and more popular. More important.
Metal Injection Moulding Make Traditional Technology Suffered a Lot
Metal injection molding technology, in China’s manufacturing industry, is developing very rapidly, from the initial powder metallurgy to the current injection molding process. In other words, in the domestic manufacturing industry, MIM technology began to flourish in recent years.
More and more new markets began to use MIM processes to make parts such as aerospace, automotive, medical, military and all walks of life. China is a big manufacturing country, so powder metallurgy will face a greater market. The traditional processing technology, will suffer the most serious test.
It is understood that MIM process are widely used in the manufacture of aircraft structural and auto parts. With the arrival of domestic manufacturing era, we believe MIM technology will have more opportunities to show their talents.
There Is Always Something Suitable For You-ARBURG
On October 19-26, 2016, ARBURG presented the ALLROUNDER injection molding machine, automatic control, one-stop turnkey equipment, freeformer for industrial material manufacturing, service solutions and related examples of industrial 4.0 theme. Innovative applications, processes and machines will show you how you can more efficiently produce plastic products in the future.
Highlights 1: The world’s first: make you surprise!
GOLDEN ELECTRIC is the first new product in 2016.
Precise, Powerful, Energy-Efficient: “Gold Edition” motors are perfect for economical production of high quality parts. They will not compromise to provide with the top price standards to match the reliable high-quality technology.
Highlights 2: a variety of injection molding technology
Lightweight construction using physical pre-foaming technology:
Lightweight construction that made by physical pre-foaming technology and dynamic mold temperature control system, be used for high gloss automotive interior parts.
Innovative rotary die process for two-component cap production:
The world’s first innovative rotary die technology used in the manufacture of packaging industry, the case of two-component caps
A watch be molded two liquid silicone rubber (LSR)
Fast-moving medical technology applications:
Fast-moving clean-room version, ALLROUNDER, manufactures medical industry through subsequent assembly and stacking dishes
Highlight 3: Automation
As a technology and system partner, we offer a wide range of automation solutions from clamps to turnkey equipment in addition to ALLROUNDER injection molding machines. In the 2016 K exhibition, most of the exhibits are equipped with robot system. From a simple robot with a six-axis robot system with SELOGICA user interface to a complete one-stop turnkey facility, all here.
Highlights 4: freeformer
We will show freeformer and ARBURG (APG) freeform molding technology (APF) for the manufacture of plastic parts. An important advantage is the ability to process qualified plastic pellets. These plastic particles include PA, ABS, PC and TPU as well as blends with special properties.
The open system allows you to build inserts, prototypes, and small batches from 3D CAD data, and we continually develop it in close proximity to real-world applications. At the K16 exhibition in 2016, you can experience new applications, materials and components from 3 exhibits.
Harber Industrial Ltd was incorporated in Hong Kong in the year of 2014. Harber is a global high-tech MIM(Metal Injection Molding) service provider Located in Hongkong. As a leading global supplier of Metal Injection Molding products,Harber is a fully integrated MIM parts producer with capabilities and proficiency in design, tooling, materials and a full range of process,surface coating and assembly operations.
https://www.harber-mim.com/Company-Overview/
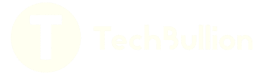