Polypropylene or PP is second most used plastic after polyethylene in the world because its available widely and in cheap rate.
PP’s material properties, processing versatility, recycling capabilities makes it one of the favorites in injection molding specifically, and in manufacturing sector in general.
The reason is, when the PP is 3d printed, it retains the sought after properties, not only that, it is also good for things that need to be water tight, durable, and light.
Although there are unique challenges, even then, the pp printing is getting popular in the traditional manufacturing sectors, we do provide solutions to those problems at boston industrial solutions.
Choosing the ink is one of the most important steps to get it done correctly.
Pad printing ink for PP
Creating consistent and top-notch pad print designs relies on finding reliable equipment and combining it with top-performing materials. It’s crucial to select the appropriate pad printing ink tailored to the specific surface, product shape, production, and usage needs.
We take pride in having the one of largest inventory of Pad Printing Inks in America.
Now, let’s explore how ink plays a role in the pad printing process and discuss the most effective methods for determining the perfect ink for each application.
The ideal polypropylene pad printing ink is one that effectively prints on the material and adheres permanently after proper curing. This ink should successfully pass essential tests like rub, tape, and scratch tests.
Although some inks in the market may assert flawless adhesion to polypropylene without any pre-treatment, this claim is misleading.
Pretreatment of PP
While the inks may pass the rub test, they often fail in the scratch or tape adhesion tests. To ensure strong ink adhesion on polypropylene plastics, it’s necessary to utilize a pre-treatment solution. Printing on polypropylene requires some preparation to ensure durable prints. Different pre-treatment methods are available, such as PP primer, flame, corona, plasma, and reactive gas technology.
COSMETIC PAD PRINTING / Packaging
The field of cosmetic pad printing comes with unique demands, particularly when it comes to printing on primary packaging.
Not only does it require resistance to chemicals, but it also necessitates the ability to adapt to fast-changing product cycles. Recognizing these challenges, we have developed several specialized series tailored to meet these specific demands.
As a result, we proudly serve as a key supplier to leading players in the cosmetics industry on a global scale.
Our expertise extends to printing on diverse materials such as glass, ceramics, metals, plastics, and natural products. Furthermore, our capabilities cover a wide array of shapes and different cosmetic products, providing a comprehensive solution for the intricate needs of cosmetic packaging.
In the cosmetic product printing, the ability to swiftly adapt to changing product cycles is crucial. Leveraging our advanced pad mounting system and efficient clamps, you can seamlessly achieve these changes in a minimal amount of time. This not only enhances the flexibility of the printing process but also ensures that cosmetic products can be presented in a dynamic and ever-evolving market.
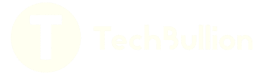