Employee safety must be a top priority in any workplace where hazardous chemicals are present. One critical component of workplace safety, especially in environments dealing with corrosive substances or particulates, is the presence of emergency eye wash stations. The Occupational Safety and Health Administration (OSHA) mandates specific standards to ensure these stations are effective in mitigating injury. This article provides an in-depth guide to OSHA eye wash station requirements, helping you understand when they’re needed, what standards apply, and how to stay compliant.
Why Eye Wash Stations Are Critical
Whether due to chemical splashes, dust, or flying debris, these injuries can lead to long-term vision problems or permanent blindness if not addressed immediately. Eye wash stations offer immediate decontamination, flushing harmful substances out of the eyes to reduce the risk of serious damage.
Rapid response is crucial—OSHA’s regulations are designed to ensure that workers can quickly reach and effectively use these stations during an emergency.
When Are Eye Wash Stations Required?
OSHA doesn’t specify exact details in its general regulations, but it refers employers to the ANSI/ISEA Z358.1-2014 standard, which is widely recognized as the best practice guideline for emergency eyewash and shower equipment. OSHA enforcement officers commonly use this ANSI standard during inspections.
According to OSHA (29 CFR 1910.151(c)):
“Where the eyes or body of any person may be exposed to injurious corrosive materials, suitable facilities for quick drenching or flushing of the eyes and body shall be provided within the work area for immediate emergency use.”
This applies to industries including:
- Manufacturing
- Laboratories
- Auto repair and painting
- Agricultural chemical handling
- Construction sites involving concrete and lime
If your workers are at risk of exposure to corrosive chemicals, you are likely required to install eye wash stations in your facility.
Key OSHA Eye Wash Station Requirements
- Location and Accessibility
An eye wash station must be accessible within 10 seconds (roughly 55 feet) of the hazard. There should be no obstructions, such as doors (unless they are always open) or equipment that could delay access. The path must be clear and well lit.
Also, the station must be on the same level as the hazard. Requiring workers to climb stairs or maneuver around machinery can render the station non-compliant.
- Water Flow and Duration
According to the ANSI/ISEA Z358.1 standard, the eye wash station must deliver a controlled flow of clean, tepid water (between 60°F and 100°F) to both eyes simultaneously. The flushing fluid should be provided at a flow rate of 0.4 gallons per minute for a full 15 minutes.
This is vital for removing chemicals effectively and minimizing damage.
- Hands-Free Operation
The station should allow hands-free operation after activation. Once turned on, it must remain on without requiring the user to continuously hold a lever or button.
This is crucial, as individuals may need both hands free to hold their eyelids open or remove contact lenses.
- Proper Signage and Lighting
Eyewash stations must be clearly marked with a visible sign and located in a well-lit area. Quick recognition is essential in an emergency.
Many facilities use green and white signage or symbols that conform to ISO standards.
- Maintenance and Inspection
Regular maintenance is the cornerstone of compliance with OSHA eye wash station requirements. The ANSI standard recommends:
- Weekly activation to ensure proper operation and clear lines of any sediment or bacteria.
- Annual inspection to verify compliance with all performance standards.
Records of maintenance and inspection should be retained to demonstrate due diligence during OSHA audits or inspections.
Types of Eye Wash Stations
Plumbed Eye Wash Stations
These are connected directly to the facility’s plumbing system and provide a continuous flow of water. They are ideal for permanent, high-risk areas and offer the most reliable water supply for prolonged flushing.
Pros:
- Unlimited water supply
- Reliable temperature control
Cons:
- Higher installation cost
- Less flexibility in relocation
Portable Eye Wash Stations
These units contain a self-contained tank of flushing fluid and are suited for temporary or remote job sites.
Pros:
- Mobility and flexibility
- Useful in areas without access to plumbing
Cons:
- Limited water supply
- Requires frequent refilling and maintenance
Personal Eye Wash Units
These are small bottles of sterile saline solution used as an initial response measure. They do not replace OSHA-required stations but can be placed at workstations for immediate flushing before reaching the primary unit.
Common Compliance Mistakes
Despite best intentions, employers often make preventable errors that can lead to OSHA violations:
- Obstructed access: Storing equipment and supplies in front of the stations.
- Improper water temperature: Using water that’s too hot or too cold, leading to user discomfort and underuse.
- Inadequate flushing duration: Using stations that provide less than 15 minutes of continuous flushing.
- Outdated equipment: Relying on old or malfunctioning units.
- No training: Failing to educate employees on how and when to use eye wash stations.
Avoiding these missteps is critical to worker safety and regulatory compliance.
Employee Training and Emergency Drills
Even with properly installed and maintained equipment, its effectiveness is compromised if employees don’t know how to use it. OSHA emphasizes the importance of employee training in emergency response procedures.
Best practices include:
- Annual training sessions with hands-on demonstrations.
- Posting simple instructions at every eye wash station.
- Emergency drills to test response time and familiarity with locations.
Employees should also be informed of the hazards that necessitate the eye wash station, so they can react quickly when needed.
Consequences of Non-Compliance
Failure to comply with OSHA eye wash station requirements can have serious repercussions:
- Injury lawsuits: If an injured employee cannot access proper flushing equipment, it could lead to costly legal action.
- OSHA citations: Inspectors may issue violations with financial penalties for non-compliance.
- Higher insurance premiums: Safety violations can impact a company’s risk profile and drive up costs.
- Loss of reputation: Clients and partners may view non-compliance as a sign of poor safety culture.
How to Ensure Compliance
To ensure that your workplace complies with OSHA eye wash station requirements:
- Conduct a hazard assessment to identify all areas needing eye wash stations.
- Install appropriate stations—either plumbed or portable—based on proximity to hazards.
- Train employees regularly on their use.
- Perform regular maintenance to keep equipment fully operational.
- Document inspections and training to stay prepared for OSHA audits.
Conclusion
Understanding and complying with OSHA eye wash station requirements is essential to protecting employees and maintaining a safe, legally compliant work environment. From proper placement and water temperature to maintenance and employee training, every aspect plays a role in ensuring these life-saving devices are effective when they’re needed most.
A proactive approach to eye safety not only safeguards your workforce but also builds a culture of responsibility and care in your organization. Regular reviews and updates of your safety protocols can go a long way in preventing accidents and improving outcomes when emergencies occur.
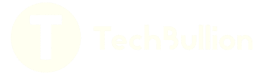