In the contemporary industrial sector, the efficient use of resources is essential, with a particular emphasis on the role of solvent recycling.
These machines are pivotal in various manufacturing processes, where the recovery and reuse of solvents are vital for both environmental sustainability and economic viability.
For industries that rely heavily on solvents, NexGen Enviro Systems’ technologies represent a step toward more sustainable practices, aligning with global trends toward environmental responsibility and resource conservation.
The Efficiency Challenge
The challenge in maximizing the efficiency of solvent recyclers involves selecting the right technology and maintaining these systems properly.
Industries must carefully choose between batch, continuous feed, and fractionating solvent recyclers, depending on their specific needs.
Regular maintenance and optimization of operating procedures are crucial in this regard.
The Basics Of Solvent Recovery
Solvent recovery, involving solvent recycler machines, plays a crucial role in industrial environments. This process entails the extraction and reuse of solvents from mixtures or waste streams, thereby minimizing waste and reducing costs.
In the automotive industry, automotive solvent recyclers are essential for recovering solvents used in painting and other processes.
Key Technologies In Solvent Recovery
Technological advancements have greatly enhanced the capabilities of solvent recycler machines.
Fractionating solvent recyclers are known for their ability to separate solvents precisely based on their boiling points, making them ideal for recovering high-purity solvents.
Continuous feed solvent recyclers are designed for high-volume industrial settings, providing a constant solvent recovery process.
In contrast, batch solvent recyclers are suitable for smaller-scale operations or where specific types of solvent recovery are required.
Sustainable Manufacturing: The Role Of Solvent Recycling
Manufacturers play a critical role in the economy, producing goods from raw materials through various processes, including machining, assembly, and more.
In the context of solvent recycling, manufacturers are not just producers of recyclers but also significant users.
Industries that require solvents for parts cleaning, painting, and other processes need efficient ways to manage and recycle these chemicals to reduce costs and environmental impact.
Enhancing OEM Solutions With Solvent Recycling Technologies
Original Equipment Manufacturers (OEMs) design and produce parts or equipment that may be marketed by another manufacturer.
In the solvent recycling industry, OEMs might integrate recycling systems into their larger equipment solutions or offer them as value-added products to their clients.
For example, an OEM specializing in automotive manufacturing equipment might include solvent recyclers as part of their comprehensive offering to automakers.
This integration helps OEMs provide more environmentally friendly and cost-effective solutions to their customers.
The Military’s Path To Eco-Friendly Solvent Management
The military, with its vast array of vehicles, machinery, and maintenance facilities, is a significant consumer of solvents for cleaning, maintenance, and repair operations.
In this sector, efficient and environmentally responsible solvent management solutions are critical to minimizing hazardous waste and ensuring compliance with stringent environmental regulations.
Aerospace Innovation Through Advanced Solvent Recycling
The aerospace industry, encompassing both commercial and military aviation, requires high standards of precision and cleanliness, making solvent use in manufacturing, maintenance, and repair operations a necessity.
The complexity and sensitivity of aerospace components mean that solvent recycling systems used in this sector must be highly efficient and capable of returning solvents to a near-original state.
These specialized systems could be particularly beneficial in this context.
They would provide aerospace manufacturers and maintenance facilities with the technology to ensure the purity of recycled solvents, thus maintaining the integrity and performance of aerospace components.
Environmental And Economic Benefits
The environmental and economic benefits of efficient solvent recycling are substantial. Industries utilizing systems like fractionating, batch, and continuous feed solvent recyclers can significantly reduce their environmental impact and operational costs.
Future Trends And Developments
The solvent recovery landscape is poised for significant changes, driven by advancements in technology and evolving industry demands.
These future trends and developments are particularly relevant to engineers, plant managers, and EHS professionals, as they will influence how solvent recovery processes are designed, implemented, and managed.
Understanding these trends is crucial for staying ahead in an increasingly competitive and environmentally-conscious industrial world.
Automation And Advanced Control Systems
Automation is set to play a pivotal role in the future of solvent recovery. We are likely to see more sophisticated, automated control systems that can optimize the recovery process with minimal human intervention.
For production engineers and plant managers, this means an increased focus on integrating these systems into existing workflows.
Automated systems will not only increase efficiency but also reduce the likelihood of human error, ensuring a more consistent and reliable process.
Internet of Things (IoT) And Connectivity
The integration of IoT in solvent recovery systems is a development that holds significant promise.
IoT-enabled devices can provide real-time data monitoring and analysis, allowing for immediate adjustments to optimize performance.
This connectivity will enable maintenance departments to transition from reactive to predictive maintenance strategies, reducing downtime and extending the lifespan of equipment.
Plant managers and EHS professionals can leverage this data to ensure compliance with environmental standards and improve overall plant safety.
Green Solvent Technologies
As environmental regulations become stricter, there is a growing trend towards the development and use of green solvents.
These are solvents that are less harmful to the environment and are often derived from renewable resources. Process engineers will need to stay abreast of these developments, as they may require adjustments to existing recovery systems.
The shift to green solvents is not just a compliance issue but also a corporate responsibility one, likely to be championed by EHS departments.
Energy-Efficient Systems
Energy efficiency is another area where significant advancements are expected. Future solvent recovery systems are likely to be designed with a greater emphasis on reducing energy consumption.
This will not only help in lowering operational costs but also align with global efforts to reduce carbon footprints.
For plant and production managers, this means balancing the initial investment in energy-efficient technologies with long-term savings and environmental benefits.
AI And Machine Learning
Artificial intelligence (AI) and machine learning are expected to revolutionize solvent recovery systems. These technologies can analyze vast amounts of data to identify patterns and predict outcomes, leading to more informed decision-making.
For engineers, this means designing systems that can accommodate AI algorithms.
Manufacturing staff will need to adapt to working alongside these intelligent systems, which will likely become an integral part of the production process.
Enhanced Safety Features
Safety in the workplace, especially in industrial environments dealing with solvents, is a paramount concern.
Future developments in solvent recovery systems are expected to include enhanced safety features, reducing the risk of accidents and exposure to harmful substances.
EHS departments will be key in implementing these features, ensuring that the systems not only meet regulatory requirements but also provide the best possible protection for workers.
The future of solvent recovery is one of innovation and adaptation. As technology advances, so too must the approaches and strategies of those involved in solvent recovery processes.
Engineers, plant managers, EHS professionals, and manufacturing staff will all play crucial roles in embracing these changes, ensuring that their facilities remain efficient, compliant, and competitive.
The focus will be on sustainability, efficiency, and safety, with technology serving as a key enabler in this evolution.
Optimizing the efficiency of solvent recycling, including automotive solvent recyclers and other types, is crucial for modern industrial operations.
It presents significant economic and environmental benefits, underscoring the need for industries to continually adapt and improve their solvent recovery practices.
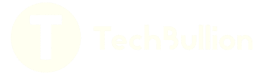