Introduction
Are you seeking to bring the innovation in design of your product designs to the next level? Multi-shot injection molding could be just what’s necessary! In this blog post, we’ll dive deep into multi-shot molding technologies and discover their power to revolutionize manufacturing processes – so come explore this tool together as we unleash innovation through design!
Advantages and Benefits of Multi-Shot Molding
Multi-shot injection molding offers numerous advantages that make it a desirable solution for manufacturers seeking to optimize their designs. It enables complex parts with multiple materials or colors produced simultaneously in one mold – eliminating secondary operations for faster cycle times and reduced production costs.
Multi-shot molding offers improved part quality by streamlining assembly processes and decreasing risks such as warping or misalignment. Furthermore, its combination of materials opens up exciting design options allowing products to display enhanced functionality as well as aesthetics.
Multi-shot molding provides additional cost and environmental savings by precisely controlling material distribution within the mold, helping reduce material wastage. These advantages make multi-shot molding an essential tool in producing efficient and high-quality production results.
Types of Multi-Shot Injection Molding Techniques
Multi-shot injection molding techniques offer many ways of creating complex designs using multi-shot injection. One such technique is overmolding, which adds another material onto an initial substrate for soft-touch finishes or enhanced grip characteristics on products like toothbrushes or tools.
Insert molding, where metal components or other materials are added directly into a mold before injecting plastic resin, has also become increasingly popular, often seen in connectors or electronic components. It results in seamless integration of different materials for seamless functionality – commonly seen with connectors and electronic components.
Co-injection molding entails injecting two materials at the same time through separate nozzles into one mold cavity – ideal for creating products with dual-colored aesthetics or combining hard and soft materials in one part of their make up.
Injection mold manufacturers who fully comprehend these various multi-shot molding techniques can maximize their benefits to create high-quality and visually appealing products efficiently and cost-effectively.
Examples of Products Manufactured through Multi-Shot Molding
Multi-shot injection molding opens a world of design options in product creation. From dual-color buttons on remote controls to intricate medical devices with soft touch grips, its applications range greatly. Imagine smartphone cases featuring different textures or automotive interior panels seamlessly blending hard and soft materials together – multi-shot injection molding makes these possibilities accessible and possible!
Multi-material seals used in food packaging require flexibility and durability; complex components like toothbrushes with ergonomic handles made of different materials also lend themselves perfectly to multi-shot molding technology, which enables precise material placement that creates products with enhanced functionality and aesthetics.
Imagine wearable devices featuring rigid frames and soft silicone bands produced through one seamless process; or everyday items, like razors, that benefit from multi-shot molding by adding rubberized grips for improved user experience. Multi-shot molding offers manufacturers unique opportunities to produce innovative products in today’s highly competitive market place.
Factors to Keep in Mind when Selecting Multi-Shot Molding Technique
Before selecting multi-shot molding techniques for your project, it’s essential to assess its complexity. Different designs may necessitate specific multi-shot processes in order to produce desired outcomes.
Material compatibility should also be kept in mind; make sure any materials used will bond effectively during multi-shot molding processes.
Consider production volume requirements when considering multi-shot molding techniques; some methods may be more cost-efficient for large production runs while other are ideal for lower quantities.
Consider design flexibility: multi-shot molding methods provide greater design freedom, permitting intricate shapes and features which traditional injection molding cannot.
Keep tooling costs and lead times within budget by choosing an approach that best meets the complexity of your mold design. Choose an approach that aligns with both budgetary constraints and timeline considerations to find an acceptable technique solution.
Applications and Industries that Utilize Multi-Shot Molding (MSM)
Multi-shot injection molding techniques have revolutionized many industries with complex products. Automotive industries often rely on this technique for creating intricate interior components with various textures and colors integrated seamlessly into a single component; cost-efficient production while meeting high quality standards is achieved using this approach.
Consumer electronics industries also benefit from multi-shot molding by producing devices with soft touch grips, dual color buttons or clear window displays in one manufacturing cycle. This streamlines production and minimizes assembly steps – ultimately saving time and resources in assembly process steps and assembly steps.
Medical device makers utilize multi-shot molding technology to design products combining different materials that deliver improved performance – for instance combining rigid plastics and elastomers for increased comfort and functionality. Meanwhile, aerospace designers employ this process to craft lightweight yet strong components to optimize aircraft performance.
Multi-shot molding has quickly become an indispensable resource in various sectors looking to stay at the cutting-edge in product innovation and efficiency.
Conclusion
Multi-shot injection molding techniques offer many benefits that can enhance design and production processes, from creating complex geometries to decreasing manufacturing steps, improving part reliability, and creating innovative designs that separate your products from those produced by competitors. By adding multi-shot molding into your next project, multi-shot molding allows you to realize these potential gains – greatly speeding up design iterations as well as production times.
With several types of multi-shot molding techniques to select from, it is vitally important that consideration be given to factors like part complexity, material compatibility, cost-effectiveness and production volume when choosing an optimal method for your project. Multi-shot molding provides the ideal way for automotive dealers looking to improve vehicle aesthetics or electronics manufacturers looking for ergonomic designs; multi-shot molding helps achieve these goals efficiently and cost effectively.
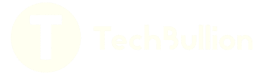