Noise assessment is not only an indispensable but highly necessary process to ensure safety within the workplace atmosphere, especially where working conditions exist that are vulnerable to excessive noise. Long-term exposure to high-level noise can create a serious health hazard where both NIHL, stress, and low productivity are witnessed. It requires a business to mitigate such risks and practice regular noise assessment in order to maintain compliance with prescribed workplace health and safety regulations. In this article, we describe the importance of noise assessments, the steps followed during noise assessments, and best practices a business should follow.
In workplaces where loud machinery, tools, or equipment are used, the noise levels can easily surpass safe limits. One of the most serious health risks involves long-term exposure to high noise levels, and NIHL is one of the most common occupational hazards within manufacturing, construction, mining, and aviation sectors. NIHL is permanent and irreversible; thus, prevention and early intervention through noise assessment have become critical.
Apart from causing hearing loss, excessive noise can lead to safety hazards by making communication among workers difficult as they may fail to hear any warnings or alarm signals. This may increase the chances of accidents, with a general deterioration in job performance due to the fatigue and stress experienced. The execution of routine noise assessments assists in the detection of hazardous levels of noise, thereby allowing businesses to take specific measures in reducing workers’ exposure, hence safeguarding their health and welfare.
Legal Requirements for Noise Assessment in Australia:
The clear requirements of managing noise in the workplace are outlined in Work Health and Safety (WHS) Regulations 2011 in Australia. In summary, these regulations say that a business is required to assess the level of noise exposure and is obliged to take necessary measures where the exposure level exceeds the national exposure standard.
Australia’s noise exposure standard is:
- 85 decibels (dB) averaged over an 8-hour work period, or
- 140 dB for a single burst of sound, such as an explosion.
Employers should make a noise assessment if it is likely that exposure to noise by workers will exceed these noise levels. If the exposure standard is exceeded, the business must take action to control the noise or reduce workers’ exposure to it.
The Noise Assessment Process:
Noise assessment involves measurement and evaluating the level of noise at the workplace. General steps usually included are:
1. Noise Hazard Identification
Identification of areas or procedures at work that may involve noise hazards. This includes the identification of specific machinery, tools, or workstations emitting loud noise, and processes or tasks likely to expose workers to harmful levels of noise.
2. Noise Level Measurement
Noise levels are measured in different locations of the workplace by special measuring equipment, such as sound level meters or noise dosimeters. There are two basic methods of measurement, namely:
- Area Noise Monitoring: Noise levels are measured in areas of the workplace, such as around machinery or near production lines. This is particularly useful for identifying “hot spots” where noise levels are particularly high.
The data can also be taken by a dosimeter that could be attached to the employee themselves to identify the personal noise exposure for the entire shift. This is typically very accurate in representing the exposure of an individual worker.
3. Analyze the Data
After noise measurement, data is analyzed to see if there is an area in the workplace which exceeds the standard 8 hours of exposure at 85 dB. Further action should be resorted to if hazardous areas are identified to reduce the noise exposure of workers.
4. Control Measures Implementation
In the case that the noise assessment points out hazardous levels to which the workers are exposed, some controls must be implemented. Examples of these controls include the following:
- Engineering controls: This refers to modifying equipment or processes at source to reduce the noise, for example, quieter machinery or the use of soundproof barriers.
- Administrative controls: This refers to policy formulation that limits exposure; for instance, rotating shifts or providing quiet areas for taking breaks.
- Personal Protective Equipment (PPE): One should provide earplugs or earmuffs for protecting the hearing of workers when other controls are insufficient.
5. Monitoring and Review
Noise levels should be measured on a regular basis to ensure control measures continue to be effective. There is a need for periodic reviews of noise assessments, mainly where changes in equipment, work processes, or the environment could have an impact on noise levels.
Best Practices for Noise Assessment
Noise assessments can only be said to be properly and acceptably carried out by regulations laid down by the Australian government when the following best practices are implemented by any business:
- Use Qualified Professionals
Noise assessments involve specialized knowledge and equipment. Businesses are advised to incorporate qualified professionals, such as occupational hygienists, who have received the correct training to measure and assess workplace noise levels with accuracy.
- Carry Out Assessments Regularly
Noise assessments should not be done only once; there should be repeated assessments, as controls and equipment may change and because of changes in either equipment or processes that may expose new noise hazards. The frequency of such assessments shall be determined by the prevailing conditions at the workplace, but annual reviews are generally recommended.
- Involve Workers
Workers usually know when the level of noise is too high. Employee involvement can ensure that potential hazards that may be overlooked otherwise will be discovered. Education on the risks of noise for workers, and the encouragement of reporting concerns, may help improve overall workplace safety.
- Maintain Detailed Records
Businesses must keep records of all noise assessments, including the methods adopted, areas assessed, and results of the assessment. Such records may assist in ongoing monitoring and review besides serving as proof of compliance with the WHS regulations.
- Provide Ongoing Training
Workers need training regarding their exposure to noise, correct utilization of their hearing protection, and the realization and identification of possibly hazardous noise levels. Refresher training given at regular intervals will help the employees remember and be conscious of the noise hazard and the protection from noise that are available to them.
Conclusion:
Noise assessment is one of the most important aspects related to ensuring workplace safety as well as health hazards arising from excessive noise that can be a constant threat within particular industries. The business enterprise will be able to identify hazardous noise levels by conducting regular noise assessments, implementing control measures, and thus protecting its workers from the long-term health effects caused due to noise exposure. Complying with the legal requirements as set forth by the Australian WHS regulations, along with best practices in their application for noise management, will lead to a safe, healthy, and productive work environment.
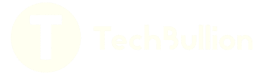