Introduction
The transformation journey of rotomolded products is no one short of amazing. The story of rotational molding that came from such humble beginnings to where it is now, a driving force in the global manufacturing trends that itself reflect the industry’s search for new ideas, efficiencies, and more sustainable production methods, is a true fairy tale.
The Genesis of Rotomolding
Rotational molding, or simply shrink molding was originally used to manufacture toys that could withstand impact despite being lightweight and hollow. This was done through potting of molten plastic in the mold under manual operation. The clear-cut and fast nature of the procedure simplified the crafting of strong and cheap plastic toys. This initial breakthrough in the rotomolding sector opened the door for it to expand in terms of different industries and demonstrate its capability in terms of adaptability and versatility.
Materials and Process Refinements
In the course of time, the development of different materials and process enhancements turned rotomolding from a special craft to an advanced production method design. Rotational molding which had polyethylene as the material, experienced the benefits of developing a stronger and UV-resistant product with improved performance. As a result of these technological progressions, this helped lengthen the limbs of rotomolded products into a much wider area of uses.
Automotive and Industrial Applications
Rotation molding technology has been extensively used by manufacturers in the automotive as well as industrial industries to realize their benefits. Rotational molded products became progressively popular in fuel tanks, right up to the level of complex components with precise designs where they developed a reputation for toughness, precision and material efficacy.
Technological Advancements Driving Evolution
The rotomolding evolutionary journey is all about the technological innovation which revolutionized the manufacturing procedure of this product’s making. These innovations not only increased the productivity but they also shaped the way we design our products and made the whole process more sustainable.
CNC introduced a new level of accuracy to the rotomolding process and continues to lead the rotomolding market. Now manufacturers can fabricate molds with the parts of highest preciseness and complexity as well which leads to manufacturing of complex products. High level of accuracy has made it possible for industries like aerospace, automotive, and others to come up with light-weight and high quality products.
Robotic Automation
Robotic automation is decreasing the production time and time required for inspection of molding machine and is leading to higher efficiency and lower margin of error. Machines have a variety of tasks. Besides the work on loading raw materials into molds, the machines can take care of the temperature controls within the furnace. Apart from facilitating faster production, this also guarantees uniform quality from batch to batch which is a big plus to consumers as they can rightfully trust and believe in the reliability of rotomolded products.
Advanced Material Formulations
The ability to deliver next-generation polymer formulations, which have contributed to the advancement of rotomoulded products, is a pivotal factor in the development of rotomoulding. These formulations become windless, weathering, and life prolonging features. Consequently, the field of rotomolding has become a choice of industries where reliability and efficient performance are the top priorities. It can be clearly observed that rotomolded products have a direct influence on manufacturing trends in the worldwide economy, in a variety of sectors. Such versatile technology has a great impact on the form and content of products, material utilization, and environmental protection standard.
Conclusion
The evolutionary path of rotomolded products from the toy industry to global dominant in various industries is a great lesson to manufacturing technologies in their capacity to vary and adjust to suits changing environments. Technological progress, meticulous engineering, as well as the focus on sustainability had been the driving factors which turned rotomolding into one of the cornerstones of global manufacturing industry that is evolving every second. As we journey further into the future, rotomolding will continue to reinvent the approach to design, heighten material characteristics and settle forming manufacturing thinking patterns.
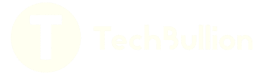