Launching a supplement brand comes with many responsibilities, and regulatory compliance should be high on the priority list. The UK supplement market is shaped by several regulations that ensure products are safe, accurately labelled, and suitable for consumers. Whether you’re a start-up or an established business, keeping up with these rules can be challenging, especially in a fast-moving sector with evolving standards.
Working with a liquid supplements manufacturer in the UK can help you stay on track, but it’s still essential to understand your obligations. From product formulation and testing to labelling and advertising, every stage must adhere to the regulations set by bodies such as the Food Standards Agency (FSA) and the Department of Health and Social Care. These authorities outline strict guidance that brands must follow to operate legally.
Ingredients and Formulation Controls
One of the first hurdles for any supplement business is selecting compliant ingredients. UK regulations specify which vitamins, minerals, and botanicals are permitted in food supplements. Certain substances may be prohibited or restricted due to safety concerns, requiring thorough checks before any formulation begins.
Beyond the permitted lists, brands need to consider ingredient purity and dosage levels. Even if a component is allowed, exceeding recommended quantities could result in enforcement action or product withdrawal. Working closely with qualified food technologists and regulatory consultants can help ensure your formulations meet legal requirements without compromising quality.
Labelling Requirements and Claims
Labelling is another crucial area where compliance must be precise. UK legislation mandates that labels clearly display information such as ingredient lists, recommended daily intake, and relevant warnings. Failing to include these details can lead to penalties or product recalls.
Health and nutrition claims are tightly controlled. Only approved claims listed in the GB NHC Register can be used in marketing materials and on packaging. Statements suggesting a product can prevent, treat, or cure diseases are not permitted. To avoid issues, brands should have all labelling and promotional content reviewed by compliance specialists before launch.
Quality Assurance and Manufacturing Standards
Good Manufacturing Practice (GMP) is central to maintaining compliance throughout production. All facilities involved in supplement manufacture must follow documented procedures to ensure products are safe and consistent. GMP encompasses hygiene controls, quality checks, and traceability processes that help protect consumers and maintain trust in your brand.
Batch testing is also a vital element of quality assurance. Regular analysis of finished products verifies that formulations match specifications and remain free from contaminants. Keeping detailed records of every production run is not only good practice but also a legal requirement that supports accountability.
Staying Informed and Responding to Change
UK supplement regulations can evolve as scientific evidence grows or international rules shift. Staying informed is essential for any brand that wants to avoid disruption. Subscribing to updates from official bodies and industry associations can help you monitor any regulatory changes that could affect your business.
When regulations are updated, it’s important to act promptly. This could involve revising formulations, updating labels, or training staff on new compliance protocols. Maintaining flexibility and a proactive approach makes it easier to adapt and continue supplying products that meet legal and consumer expectations.
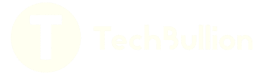