Introduction:
Rubber stoppers serve as indispensable components in pharmaceutical packaging, ensuring the integrity and safety of medications. However, ensuring compatibility between rubber stoppers and diverse pharmaceutical formulations poses significant challenges for manufacturers. This article delves into the complexities of achieving compatibility and explores innovative solutions to overcome these challenges.
Understanding Compatibility Challenges:
Rubber stoppers are commonly used in pharmaceutical vials and containers to create a hermetic seal and prevent contamination or degradation of medications. However, the interaction between rubber stoppers and pharmaceutical formulations can lead to issues such as leaching, adsorption, or chemical incompatibility. Factors influencing compatibility include the type of rubber used, the composition of the formulation, and storage conditions.
Challenges in Achieving Compatibility:
- Leaching and Extractables: Rubber stoppers may release compounds or additives into the pharmaceutical solution over time, potentially affecting drug stability or safety. Leachable substances such as antioxidants, plasticizers, or vulcanizing agents pose risks to product quality and patient safety.
- Adsorption: Some pharmaceutical formulations may adhere to the surface of rubber stoppers, leading to drug loss or reduced efficacy. Adsorption can occur due to the hydrophobic nature of rubber surfaces or interactions with formulation components.
- Chemical Incompatibility: Certain pharmaceutical ingredients may react with rubber stoppers, leading to degradation or alteration of drug properties. Chemical incompatibility can result in changes in pH, precipitation of insoluble particles, or formation of reactive by-products.
Solutions to Compatibility Challenges:
- Material Selection: Rubber stopper manufacturer can optimize material selection based on the specific requirements of pharmaceutical formulations. Choosing rubber compounds with low extractable profiles, minimal leachables, and inert properties can mitigate compatibility risks.
- Surface Treatment: Surface modification techniques such as plasma treatment or coating deposition can improve the surface properties of rubber stoppers, reducing adsorption tendencies and enhancing compatibility with pharmaceutical formulations.
- Barrier Coatings: Applying barrier coatings or liners to the interior surface of rubber stoppers can prevent leaching and minimize interactions between rubber and pharmaceuticals. Barrier coatings act as a protective layer, reducing the risk of chemical migration or contamination.
- Compatibility Testing: Rigorous compatibility testing protocols can help identify potential interactions between rubber stoppers and pharmaceutical formulations early in the development process. Accelerated aging studies, extractables and leachables testing, and compatibility assessments under simulated storage conditions are essential for ensuring product safety and stability.
Conclusion:
Achieving compatibility between rubber stopper and pharmaceutical formulations is essential to ensure product quality, safety, and efficacy. Rubber stopper manufacturers play a critical role in addressing compatibility challenges through material selection, surface treatment, and innovative solutions. By implementing robust testing protocols and collaborating closely with pharmaceutical manufacturers, rubber stopper manufacturers can contribute to the development of reliable packaging solutions that meet the stringent requirements of the pharmaceutical industry.
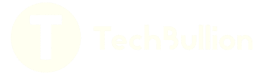