Nanotechnology is transforming material science like never before. Manufacturers across the USA are increasingly turning to nanotech solutions to drive innovation, improve product performance, and remain competitive in the global market. This transformative technology, rooted in manipulating matter at the atomic and molecular levels, is opening new frontiers in manufacturing. As a result, material science services built around nanotechnology are now more tailored, precise, and impactful than ever before.
The Fusion of Nanotechnology and Material Science: A Game Changer for the Manufacturing Sector
Nanotechnology, by definition, involves the manipulation of materials with dimensions smaller than 100 nanometers. When combined with material science, it allows the creation of entirely new materials with enhanced mechanical, thermal, electrical, and chemical properties. This fusion is not just theoretical—it’s already reshaping various sectors of manufacturing in the USA, from aerospace to biomedical devices, automotive, electronics, textiles, and beyond.
Moreover, the development of nanomaterials is enabling innovations that were once considered impossible. For instance, materials can now be made lighter yet stronger, more heat-resistant yet flexible, and more conductive while maintaining insulation where needed. These capabilities translate directly into better products and more efficient manufacturing processes.
Customization of Material Science Services for U.S. Manufacturers
The U.S. manufacturing sector is diverse, encompassing small startups, mid-sized enterprises, and multinational corporations. Consequently, one-size-fits-all solutions rarely suffice. Recognizing this need, material science service providers are increasingly offering customized nanotechnology services tailored to the specific requirements of individual manufacturers.
These services range from R&D partnerships to prototyping, scalability testing, quality assurance, and even regulatory compliance consulting. By collaborating closely with manufacturers, nanotech specialists can develop bespoke materials with exact properties, optimized for the intended use-case, production process, and market demands.
Key Areas Where Tailored Nanotech Material Services Are Making an Impact
Lightweight and High-Strength Materials:
The automotive and aerospace industries benefit significantly from nanocomposites that reduce vehicle weight while maintaining or enhancing strength and durability. This not only improves fuel efficiency but also extends the lifespan of components.
Corrosion-Resistant Coatings:
Nanotechnology enables the development of ultra-thin coatings that protect materials from corrosion, particularly in harsh environments. This innovation is especially crucial for manufacturers operating in marine, construction, and infrastructure sectors.
Thermal Management Solutions:
Nanomaterials like graphene and carbon nanotubes are excellent conductors of heat. Their use in electronics manufacturing enhances thermal management, which is critical for preventing overheating and ensuring optimal performance.
Wear-Resistant and Self-Healing Materials:
Manufacturing equipment and tools benefit from surfaces embedded with nanoparticles that resist abrasion and can even self-repair minor scratches. This significantly reduces maintenance costs and downtime.
Energy Storage and Conversion Devices:
Nanotechnology is at the forefront of improving battery performance, energy density, and recharge cycles. For manufacturers focused on sustainable products and green technologies, this innovation is invaluable.
The Role of Research Institutions and Startups in the USA
Innovation in nanotechnology is largely driven by academic research institutions and agile startups that focus on applied sciences. In the USA, institutions such as MIT, Stanford, and the University of California have state-of-the-art nanotech laboratories working in collaboration with industry players.
Startups, on the other hand, are filling gaps in commercialization. With agile teams and a focus on solving niche problems, these small companies often produce breakthrough technologies that quickly make their way into mainstream manufacturing. Many of these startups offer consulting, licensing, or direct partnerships with manufacturers seeking to integrate nanotech into their operations.
Government Support and National Initiatives
To further accelerate the adoption of nanotechnology in manufacturing, the U.S. government has implemented several initiatives. The National Nanotechnology Initiative (NNI), for example, coordinates efforts among federal agencies to support research, infrastructure development, and commercialization strategies.
Grants, subsidies, and public-private partnerships have allowed even smaller manufacturers to gain access to nanotechnology services. This democratization of innovation helps create a level playing field and encourages wider adoption across industries.
Additionally, regulatory bodies such as the FDA and EPA are actively working on guidelines to ensure the safe use of nanomaterials in products ranging from medical devices to consumer goods. This proactive approach builds trust and provides clarity to manufacturers.
Benefits of Adopting Nanotech Material Services for U.S. Manufacturers
Integrating nanotechnology into material science services offers numerous advantages:
Enhanced Product Quality:
Materials engineered at the nanoscale exhibit superior strength, flexibility, and resistance to environmental stressors.
Improved Efficiency:
Manufacturing processes become more efficient with reduced material waste, faster production cycles, and fewer defects.
Cost Savings Over Time:
Although the initial investment in nanotechnology services may seem high, the long-term savings in maintenance, energy, and material costs make it worthwhile.
Increased Market Competitiveness:
Innovative materials provide manufacturers with a competitive edge, especially in industries where performance and sustainability are key differentiators.
Sustainability:
Many nanomaterials contribute to environmental goals by enabling recyclable products, reducing emissions, or requiring less energy for production.
Challenges to Consider When Integrating Nanotechnology
Despite its promise, integrating nanotechnology into material science services comes with certain challenges. These include:
- High Initial Costs: Advanced nanomaterials and the equipment needed to produce them can be expensive, especially for small manufacturers.
- Knowledge Gaps: There is often a lack of in-house expertise, which necessitates external consulting or training.
- Regulatory Compliance: Ensuring materials meet health, safety, and environmental standards is a complex and evolving challenge.
- Scalability Issues: Some nanomaterials perform well in lab settings but require adjustments before being produced on an industrial scale.
Nevertheless, these challenges are being addressed progressively through collaborative efforts between research institutions, private companies, and government bodies.
The Future of Nanotech-Driven Material Science in U.S. Manufacturing
Looking ahead, nanotechnology will likely become even more deeply integrated into material science services. With advances in AI and machine learning, the discovery and optimization of new nanomaterials will become faster and more cost-effective. Furthermore, additive manufacturing (3D printing) using nanomaterials is on the rise, offering new possibilities in product design and customization.
As sustainability continues to influence manufacturing priorities, the demand for eco-friendly nanomaterials will grow. This includes biodegradable polymers, nanostructured catalysts for cleaner chemical processes, and more efficient photovoltaic materials for renewable energy systems.
In the near future, it’s also anticipated that modular nanotech service platforms will emerge. These will allow manufacturers to select, test, and implement nanomaterials much like selecting software packages today—flexibly and affordably.
Conclusion
Nanotechnology is no longer the future; it is the present force driving material innovation. For manufacturers in the USA, embracing tailored nanotechnology material science services is not just an option but a strategic imperative. These services enable companies to meet growing consumer demands for smarter, more sustainable, and higher-performing products.
From reducing operational costs to unlocking entirely new product categories, the potential is vast. By investing in nanotechnology and collaborating with experienced material science professionals, U.S. manufacturers can not only remain competitive but also lead the next wave of industrial innovation.
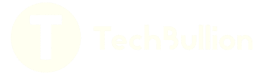