In a world where demanding industries seek materials capable of withstanding extreme conditions, discover MP35N, an alloy that stands out as one of the most high-performing options. Used in sectors such as aerospace, medicine, oil, and gas, as well as in other fields requiring cutting-edge materials, this high-performance alloy is renowned for its exceptional corrosion resistance, mechanical strength, and flexibility. Let’s explore why MP35N has become a key choice for these advanced industries, known for pushing the boundaries of technological innovation and material science.
Composition and Exceptional Properties
MP35N is an alloy composed of nickel (35%), cobalt (35%), chromium (20%), and molybdenum (10%), a combination of metals that together create exceptional synergy. This unique composition provides the alloy with unmatched physical and mechanical properties, particularly its extreme tensile strength and outstanding resistance to corrosion. These characteristics are especially sought after in environments where materials are subjected to intense mechanical and chemical stress.
One of the alloy’s key strengths is its ability to withstand high pressures, extreme temperatures, and a wide variety of corrosive agents, such as acids, chlorides, and seawater. Additionally, MP35N possesses remarkable ductility, meaning it can be formed and worked without compromising its strength or structural integrity, making it highly adaptable in various manufacturing processes.
Applications in Cutting-Edge Sectors
Thanks to its exceptional characteristics, MP35N has become indispensable in sectors at the forefront of technological innovation. Here are some major applications of this alloy:
- Aerospace Industry: MP35N is used in the manufacture of critical components such as bolts, nuts, springs, and fasteners for airplanes and spacecraft. The alloy’s ability to withstand extreme temperatures, high forces, and vibration makes it an ideal choice for applications where safety and performance are paramount.
- Medical Sector: In the medical field, MP35N is used in surgical implants and medical devices such as pacemakers and stents. Its corrosion resistance and biocompatibility are key factors that allow this alloy to last within the human body without causing adverse reactions, enhancing patient safety and product longevity.
- Oil and Gas Industry: Highly corrosive underwater environments require extremely robust materials. MP35N is used to manufacture components such as valves, seals, and drilling equipment, where reliability is crucial to minimize the risk of failure and ensure operational efficiency.
Corrosion Resistance and Economic Advantages
MP35N’s ability to resist corrosion in extreme environments helps reduce the costs associated with the maintenance and replacement of materials in industrial applications. By minimizing the risk of premature failure, companies can extend the lifespan of their equipment while reducing costly downtimes. This makes MP35N a valuable long-term investment for industries focused on operational sustainability.
Moreover, due to the exceptional strength of this alloy, less material is required to manufacture components, which can reduce production costs while offering superior performance, providing both economic and engineering benefits.
MP35N is undoubtedly one of the most high-performing alloys available on the market today. Its unique combination of mechanical strength, corrosion resistance, and flexibility makes it essential for the most demanding industries. As technology continues to advance, MP35N will remain a key element in future innovations, ensuring durability, reliability, and safety in extreme environments.
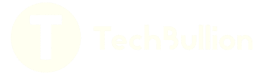