The secret to success in the complex world of semiconductor manufacturing, where creativity and accuracy collide, is strategic planning. This industry is characterized by meticulous processes and decisions, especially when managing the costs associated with converting raw wafer output into finished products. Approximately 80% of the Bill of Materials (BOM) cost for semiconductor products such as NAND, Memory, CPUs, and GPUs is attributed to the wafer. This statistic underscores the importance of strategically planning for the conversion process from fab output to the final product. The cost breakdown typically includes expenses from wafer-to-prepackaging, repackaging to the final SKU, and inventory positioning, making efficient management of these costs crucial.
Managing the conversion cost efficiently is paramount, given that fab output is a depreciating asset. The goal is to minimize expenses while ensuring swift delivery to meet market demands accurately. To achieve this, maximizing yield from the wafer is crucial. Employing engineering methods to this end is essential, with one effective strategy being the implementation of the “shift left” approach. This approach involves identifying and rectifying defective products at earlier stages of production, thereby minimizing costly failures downstream.
A prominent expert in this area, Anurag Reddy, has developed a comprehensive model that is intended to plan wafer supply and backend capacity for a duration of eighteen months. This model involves generating forecasts for various products, such as SSDs, phone memory, and retail flash devices, and then creating a wafer plan to align with these forecasts in the fabrication facilities. What sets this model apart from typical industry practices are two main aspects: it operates as an unconstrained model, and its objectives facilitate decision-making from demand to supply, contrary to the conventional supply-to-demand approach in semiconductor companies.
Accurately predicting demand is another critical aspect, especially given the six-month lock-in period for FAB supply. During this period, flexibility is limited, making precise demand forecasting imperative. Tight integration between sales and operations can help achieve this by locking in purchase orders (POs) and leaving room for high-margin business opportunities. Avoiding bottlenecks in backend manufacturing is equally important for maintaining efficiency. Any delays in this process can lead to significant costs, as wafer inventory depreciates over time. Strategies such as capacity planning and smart inventory placement can help mitigate these risks, ensuring a smooth production flow.
Reddy’s model also facilitates swift scenario planning regarding long-term fab mix, thus empowering critical business decisions like future fab investments or setting long-term product sales targets. This model’s unique approach allows for the swift transition from demand forecasting to supply planning, a significant departure from traditional methodologies in the industry. By incorporating these modifications, he has provided a pivotal decision-making tool for corporate-level strategy, showcasing a significant advancement in the strategic planning processes within semiconductor manufacturing.
Redefining long-term planning in semiconductor manufacturing involves optimizing the conversion process from fab output to finished products. By maximizing yield, accurately forecasting demand, and minimizing bottlenecks, semiconductor manufacturers can navigate the complexities of the industry and stay ahead in the competitive market landscape. Anurag Reddy’s contributions exemplify how innovative approaches and strategic planning can lead to substantial improvements in efficiency and cost management in the semiconductor sector. The continued evolution of these models will undoubtedly play a crucial role in shaping the future of the semiconductor industry, driving innovation, and maintaining a competitive edge in a rapidly changing technological landscape.
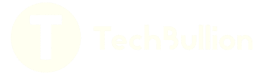