Shipping is a core component of commerce that deeply influences customer satisfaction and operational success. When businesses falter in their shipping processes, the consequences can be immediate and tangible. Delays, unexpected costs, and dissatisfied customers often result from seemingly small mistakes that compound over time, eroding trust and efficiency within the supply chain.
Identifying common pitfalls reveals how various aspects of shipping can hinder performance. From packaging inefficiencies to disorganized inventory or mismanagement of multi-item orders, each mistake can ripple through operations. Addressing these issues can not only streamline processes but also enhance the overall experience for customers.
The Hidden Costs of Inefficient Packaging
Bad packaging habits can drive up shipping costs and create headaches for operations. Using oversized boxes for small items means paying more for shipping because of size-based pricing, while underfilled boxes can lead to damaged products and expensive returns. Poorly designed packaging also needs extra padding and materials, which adds costs and makes shipping harder.
Mislabeling or incorrect documentation only compounds these challenges, leading to significant delays. Adopting fulfillment kitting services presents an effective strategy to standardize packaging and improve operational workflows. By making certain products are packaged consistently and correctly, businesses can reduce errors and enhance efficiency in the shipping process.
Addressing Inventory Chaos
A disorganized inventory contributes to operational delays, with employees struggling to find items along cluttered aisles or shelves. This chaos not only impedes the speed of order fulfillment but also frustrates staff, leading to diminished productivity. When time is lost searching for products, the entire shipping process takes a hit, ultimately affecting customer satisfaction.
Inaccurate stock counts exacerbate these issues, leading to fulfillment bottlenecks that slow down processing times. Introducing kitting practices significantly enhances organization by grouping related items together, streamlining the process of picking and packing. This approach not only quickens operations but also can improve accuracy in fulfilling orders without running into inventory discrepancies.
Solving Multi-Item Order Complexities
Multi-item order processing can easily lead to mistakes. Incorrectly grouped or missing items slow down operations and create extra work for employees who have to fix the errors. These delays can frustrate customers waiting for their orders, reducing their overall satisfaction. For example, if a part is missing from an electronics order, employees may need to search through inventory and update the system, wasting valuable time.
Kitting services simplify handling multi-item orders by pre-packing related items into bundles. This keeps everything organized and reduces mistakes like missing or mismatched items. For example, packing all pieces of a DIY furniture set together helps customers get everything they need, avoiding incomplete orders.
Streamlining Complicated Workflows
Inefficient workflows in shipping often include redundant steps like repetitive data entry, unclear task assignments, and unoptimized picking routes within warehouses. These issues slow down fulfillment rates and lead to misunderstandings between teams in different locations. Without clear guidelines or consistent training, employees may unknowingly follow conflicting processes, creating delays that directly impact customer delivery timelines.
Simplifying workflows through effective strategies significantly cuts down on these issues. Integrating kitting into the process reduces the number of steps and standardizes procedures, allowing for quicker and more accurate order fulfillment. Streamlining these tasks can result in noticeable improvements in efficiency and customer satisfaction—establishing a smoother shipping experience.
Overcoming Seasonal Challenges
Busy seasons make shipping harder for businesses because of the sudden spike in orders. The rush can overwhelm systems, causing delays that leave customers waiting longer. On top of that, having too few staff or not enough space in warehouses makes things worse, slowing down the process of packing and shipping. These delays can upset customers and lead to bad reviews or lost sales.
Fulfillment kitting services provide a scalable solution for handling fluctuating shipping demands during peak seasons. These services allow businesses to pre-assemble related products into kits, simplifying the order fulfillment process. Organizing inventory ahead of time reduces the workload on staff and optimizes warehouse space utilization.
Fixing shipping problems is key to running your business smoothly and keeping customers happy. Start by using packaging that fits your products—this cuts costs and avoids damage during delivery. Organize your inventory with systems like kitting, which groups related items together to make picking and packing faster. For orders with multiple items, bundling products reduces mistakes and keeps things moving. Simplify workflows by cutting out extra steps and standardizing processes to avoid delays. During busy seasons, using kitting services can help you handle more orders efficiently. These simple steps can save time, cut costs, and improve customer satisfaction.
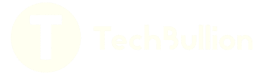