Metal Injection Molding (MIM) has been in China for more than ten years, and the MIM industry has been developing in China for more than 10 years. With the rapid growth of demand for metal injection molding products in the global market, and the global manufacturing industry shift to Asia, the Asian MIM industry will continue to grow. Then, how about the development of main MIM transfer—-China’s MIM industry?
First of all, let’s have a view of China’s MIM industry: Most MM factories in China are small ones with low production capacity. Most of the sales are below 10 million yuan. In China, less than 10 MIM companies with an annual output value of more than 10 million yuan. The annual output value of more than 20 million yuan of enterprises can be described as rare. Even if barely more than 20 million yuan, is because of large investment. From the perspective of investment income, the cost is too expensive to pay, and did not achieve a good return on investment results.
MIM enterprises in a sense is a high-tech money-waste industry. From the world famous MIM business success trajectory, only three consecutive years of annual output value of more than 50 million are in line with this burning High – Tech industry’s investment return.
Second, a few factors restricting the development of MIM enterprises. From the external market environment, the rapid development of various manufacturing industries offer MIM industry large demand market. It is true. However, it is difficult for MIM enterprise to break the existing scale. The reason is that the lack of market development capability, the inherent high threshold of the industry itself and lack of MIM professional talents.
Third, the feeding in MIM process rely on foreign import for long time since MIM was introduced to China, which is a problem in MIM factories. Because the domestic wax material from the mixing system start is not stable, it influences the MIM enterprise industrialization and China MIM enterprises have paid a lot for the lesson.
In the end, low level of standardization of the production process and weak production line can also restrict the development of the entire MIM industry.
China’s MIM Shuffle And Coming Opportunity
First, after over 10years development, lots of leader companies has begun to take shape.
Secondly, some industry standards of the standard industry have been improved gradually, and the professional network platform of the whole service industry can better transmit the latest information of the industry so that the MIM industry in China can synchronize with the well-known enterprises at home and abroad as quickly as possible.
Thirdly, the feed production of domestic production level continuously improve. A number of domestic factories will import foreign feed production equipments and production lines. With the catalytic debonding equipments and domestic feed gradually being accepted, MIM industry is facing a huge reshuffle.
MIM industry is facing the standardization of production, the development of intensive opportunities. With this opportunity, only those who are willing to cooperate with domestic and foreign industry experts to adapt to the market and the environment, innovative MIM companies, can seize the opportunity to become the biggest winner in the reshuffle.
MIM Technology Living Example
At Present in the market, the demand for various parts of the product size range is generally greater than 10mm, and the minimum thickness is between 10 ~ 30mm. If MIM products can reach 30mm size range, MIM applications will be greatly widened, especially in the field of firearms, automobiles, precision machinery, such as submachine guns, machine guns, artillery, automotive engines, mechanical arm parts etc.. Metal injection molding technology ± 0.3% to 0.5% dimensional accuracy, although is better than precision casting products, but cannot compared with powder metallurgy pressing / sintering CNC machining.
If the size can be increased to ± 0.1% ~ 0.05%, close to the traditional powder metallurgy pressing / sintering process’ dimensional accuracy, and the level of CNC machining, MIM technology and vitality will greatly expand. On the other hand, although MIM has been used in various materials system, but regarding to the market sales point, most majority of products focused on low-alloy steel, stainless steel products which have low requirement on the mechanical properties.
In Japan, for example, 67% of MIM products in 2002 were low-alloy steel and stainless steel products, and less than 15% were defect-sensitive tools with high mechanical properties such as Ti-alloy, high-speed steel and hard alloy. These materials are very difficult to process and very suitable for MIM. However, due to their sensitivity to defects, traditional MIM technology is prone to introduce various defects in various process steps, so far MIM technology has been used in these materials very few applications.
If there is defect-free and high-performance MIM technology, MIM material types will greatly expand, so as to the material market. At present, the international community has paid attention to the limitations of the existing MIM technology. A few units started in a particular area of research. Such as the French company, Impace, has developed a new technology called Quickset binderless MIM. Only 5% of the traditional MIM binder content, which breaks the traditional MIM product quality and size restrictions. By this process, with a powder particle size of 74 μm allows preparation of articles up to 20 mm in thickness and up to 800 g in weight. US company Thermat, has developed a new PMIM process, using different size powder mix, making the product size accuracy of ± 0.1%. The University of Pennsylvania is researching MIM processes for cemented carbide, high speed steel and ceramic cutting tools.
In addition, in the aspect of injection molding and other emerging advanced technology, the United States and Europe are also carrying out a variety of work, such as injection molding technology and microwave sintering technology, a variety of materials system hybrid injection, injection molding technology and microelectronics production Technology and the integration of highly automated control of the introduction of chemical production equipment.
Harber Metal Ltd. is a powder metallurgy manufacturing company created since 2014, with good production facilities and advanced technology, and is now into the production of iron-based powder metallurgy and stainless steel powder metallurgy. The company covers an area of 5,000 square meters, with 1,600 square meters of workshop, and dozens of sets of automatic presses from 100 tons to 5 tons for powder metallurgy. There are dozens of sets of automatic presses for powder metallurgy ranging from 100 tons to 5 tons, as well as complete product testing equipment and matching powder metallurgy mold processing equipment. Now the company has an annual output of 500 tons, about 5 million pieces of powder metallurgy products. products per year.
https://www.harbermetal.com/
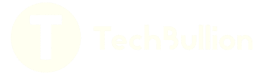